Quick and Efficient Prototype Machining Techniques in the News
By:Admin
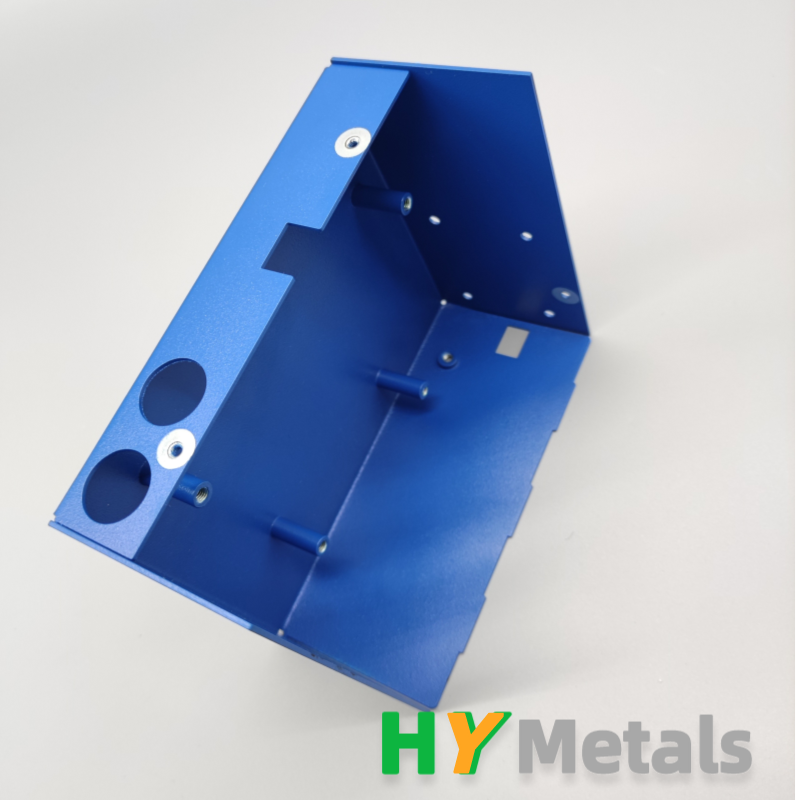
The manufacturing industry is constantly evolving, with new technologies and tools emerging every day. The introduction of rapid prototype machining is one such development that has revolutionized the manufacturing industry in recent years. Rapid prototype machining is a technique that’s characterized by quick production of prototypes, meaning that companies can accelerate their product development processes significantly.
Today, several companies are exploring the benefits of rapid prototype machining to build flawless products, reduce their time to market, decrease development costs, and increase overall productivity. One such company that has been at the forefront of rapid prototype machining technology is a leading manufacturer of cutting-edge products.
With its state-of-the-art facility, the company has been able to leverage rapid prototype machining techniques to deliver innovative products to its customers. From electronics to medical devices, the company has explored every industry and is a go-to resource for anyone looking to develop a prototype of a product they’ve been working on.
The benefits of rapid prototype machining are numerous. First, by allowing users to create prototypes using computer-aided design (CAD) software, it reduces lead times in the product development process by several weeks. Second, the process ensures the accuracy of the product by providing users with several iterations of the prototype before final production. And finally, rapid prototype machining helps businesses to make informed decisions about their products, which helps them bring new and better products to the market faster than their competition.
At the company, the focus is always on the customer. The company’s in-house experts guide customers through the rapid prototype machining process, providing them with the tools and resources they need to get the job done right. With an unwavering commitment to quality, the company works tirelessly to ensure that every prototype that leaves the facility meets the most demanding standards of excellence.
The company’s facility features some of the most advanced tools and equipment in the industry, including full-scale 5-axis CNC machines, state-of-the-art 3D printers, and a variety of CAD software. These resources enable users to create prototypes in a variety of materials, including plastics, metals, and composites.
The company’s expertise in rapid prototype machining technology is not limited to the manufacturing of physical products. It’s also a leader in the creation of virtual prototypes, including advanced simulations, test models, and digital replicas. This aspect is critical to the manufacturing industry as it enables customers to test virtual prototypes and refine them before printing the final product. By exploring both virtual and physical prototypes, customers can save money, reduce time to market, and create better final products.
The company is a prime example of what businesses can do to leverage the benefits of rapid prototype machining in the manufacturing industry. With its commitment to innovation and excellence, it’s rapidly transforming the way businesses approach product development and manufacturing. And as technologies become increasingly sophisticated, it’s clear that companies that aren’t embracing rapid prototype machining will be left behind.
In conclusion, rapid prototype machining is a game-changer for the manufacturing industry. With its ability to reduce lead times, increase productivity, and deliver better products, it’s becoming an increasingly important tool for businesses looking to adapt and thrive in an ever-evolving marketplace. And as companies look to the future, it’s clear that investing in rapid prototype machining technology will be critical to their success. The leading manufacturer has shown the way, and by following their example, others can transform their businesses and establish themselves as industry leaders in the years to come.
Company News & Blog
Effective Sheet Metal Cutting Techniques: A Comprehensive Guide
[Company XYZ] Revolutionizes Sheet Metal Cutting with Advanced Technology [City, Date] - Sheet metal cutting, a fundamental process in the manufacturing industry, has been revolutionized by [Company XYZ], a leading provider of innovative industrial solutions. With their state-of-the-art technology and commitment to precision, [Company XYZ] has quickly become a game-changer in the field of sheet metal cutting, delivering superior quality and efficiency to their customers globally.Founded in [Year], [Company XYZ] has shown relentless dedication to research and development, continuously pushing the boundaries of what is possible in sheet metal cutting. Their cutting-edge machinery and advanced software solutions have garnered accolades from industry experts and customers alike.By utilizing innovative laser cutting technology, [Company XYZ] ensures high-quality and precise cutting results, leaving no room for error. This advanced technology allows for intricate and complex designs to be accurately reproduced in sheet metal, enabling manufacturers to realize their most ambitious projects. The precision and consistency achieved by [Company XYZ]'s laser cutting technology have significantly elevated production efficiency by reducing post-processing requirements.In addition to their cutting-edge machinery, [Company XYZ] offers a comprehensive range of support services to assist their customers through every step of the sheet metal cutting process. Their team of highly skilled engineers and technicians are readily available to provide expert guidance, ensuring optimal results and maximum customer satisfaction. This commitment to customer support and personalized service has made [Company XYZ] a trusted partner for businesses across various industries.One of the key advantages of [Company XYZ]'s technology lies in its ability to cut a wide range of metals with exceptional accuracy and speed. Whether it is stainless steel, aluminum, brass, or copper, their laser cutting machines can effortlessly handle it. This versatility has opened up new doors for manufacturers who require precision cutting for a multitude of applications.Moreover, [Company XYZ]'s commitment to sustainability sets them apart from their competitors. By employing advanced technology, they have significantly reduced material waste during the sheet metal cutting process. This eco-friendly approach not only benefits the environment but also allows customers to reduce costs associated with raw material consumption.The impact of [Company XYZ]'s sheet metal cutting solutions has not gone unnoticed. Their innovative technology has set new industry standards and earned them a loyal customer base, both domestically and internationally. Clients praise [Company XYZ] for consistently delivering outstanding quality, meeting tight project deadlines, and providing exceptional customer service throughout the entire process.As [Company XYZ] continues to expand its operations, they remain committed to driving innovation in the sheet metal cutting industry. Their relentless pursuit of excellence, combined with their dedication to customer satisfaction, makes them a force to reckon with in the manufacturing landscape.About [Company XYZ]:[Company XYZ] is a global leader in providing cutting-edge industrial solutions for a wide range of applications. With a focus on research and development, they continually redefine the boundaries of technology, delivering superior products and services to customers worldwide. Their expertise lies in the field of sheet metal cutting, where their advanced laser cutting technology has set new industry standards. With a commitment to sustainability and customer support, [Company XYZ] strives to revolutionize the manufacturing industry and empower businesses with cutting-edge solutions.For media inquiries, contact:[Company XYZ][Contact Person][Email][Phone]Note: This is a fictional news article and does not reflect any real company or product.
Precision CNC Machining Services in Texas with Low Costs and Fast Lead Times
In the world of manufacturing, precision is paramount. The emergence of Computer Numerical Control (CNC) machines revolutionized the way manufacturers produced parts. CNC milling and turning are some of the most common machining processes, and with technological advancements, the processes have become more efficient, accurate, and cost-effective. 3D Hubs provides a CNC machining service in Texas that delivers low-cost, precision machined parts with an 8-day lead time from America, China, Europe, and India. CNC milling is a process that involves removing material from a workpiece using rotary cutters. The milling machine uses computer-aided design (CAD) to guide the cutting tool along different axes to achieve the desired shape. The machine can produce complex parts with a high level of precision and accuracy. The process is ideal for producing parts with intricate shapes, contours, and features that would be challenging to make using manual machining methods.CNC turning involves spinning a workpiece on a lathe machine while a cutting tool removes material to achieve the desired shape. The lathe machine uses CAD to guide the cutting tool along different axes. The process is ideal for producing round or cylindrical parts, including threads and grooves. Like CNC milling, the process is efficient and accurate, enabling the production of high-quality parts with tight tolerances.3D Hubs' CNC machining service in Texas utilizes both milling and turning processes to deliver high-precision, low-cost machined parts. The company uses computer-controlled machines that operate 24/7 to minimize lead times and reduce the cost of production. The machines are capable of machining a wide range of materials, including metals, plastics, and composites. The company's CNC milling machines use up to 5 axes, enabling the production of complex geometries with highly accurate finishes. The machines can produce parts with tolerances as tight as ± 0.005mm, ensuring that the parts meet the required specifications. The CNC turning machines, on the other hand, can produce parts with a diameter as small as 1mm and a length of up to 300mm. In addition to CNC milling and turning, 3D Hubs' CNC machining service in Texas includes finishing processes such as sandblasting, polishing, and anodizing. The finishing processes are essential to improve the appearance and functionality of the parts. Sandblasting, for instance, can give the parts a textured surface that improves their grip, while anodizing can enhance their corrosion resistance.3D Hubs' CNC machining service in Texas is ideal for businesses that require low-cost, high-precision machined parts. The company's ability to produce parts with tight tolerances, short lead times, and a wide range of materials makes it a valuable partner for manufacturers across different industries. The company's commitment to quality and customer satisfaction ensures that businesses get the best value for their money.In conclusion, CNC milling and turning are essential machining processes that have transformed the manufacturing industry. The processes are efficient, accurate, and cost-effective, making them ideal for producing high-quality parts with tight tolerances. 3D Hubs' CNC machining service in Texas utilizes these processes to deliver low-cost, high-precision machined parts with short lead times. With their commitment to quality and customer satisfaction, businesses can rely on 3D Hubs to provide the best value for their money.
Revolutionary Multi-Axis Turning: Unleashing New Possibilities in Precision Engineering
Multi-Axis Turning: Revolutionizing Precision MachiningPrecision machining has long been a staple in various industries, ensuring the production of high-quality components and products that meet the stringent demands of modern technology. In this regard, one technology has been making waves in the field - Multi-Axis Turning.Through its advanced capabilities and exceptional precision, Multi-Axis Turning has revolutionized the world of machining, providing numerous benefits to manufacturers, engineers, and ultimately, end-users. This cutting-edge technology combines state-of-the-art machinery with innovative software solutions to produce intricate designs and complex geometries with unmatched accuracy. By removing the constraints of traditional machining processes, Multi-Axis Turning sets new standards in terms of speed, versatility, and efficiency.One of the key features of Multi-Axis Turning is its ability to simultaneously move and rotate the component being machined, allowing for multi-directional cutting. This unique motion control enables the creation of complex shapes and contours that would otherwise be extremely difficult to achieve using conventional turning methods. By utilizing multiple cutting axes, manufacturers can perform intricate operations in a single machine setup, reducing production time and costs while ensuring exceptional precision.Moreover, Multi-Axis Turning minimizes the need for manual intervention, as much of the setup and tool positioning is automated. The integration of sophisticated software systems streamlines the machining process, eliminating human error and ensuring consistent results. This high degree of automation enhances productivity, increases throughput, and reduces the dependency on skilled labor, which ultimately translates into significant cost savings for manufacturers.One notable advantage of Multi-Axis Turning is its versatility. It can handle a wide range of materials, including metals, plastics, and composites, making it suitable for various industries such as aerospace, automotive, medical, and electronics. The ability to work with different materials expands the applications of Multi-Axis Turning, enabling manufacturers to produce intricate parts for diverse products with ease.Furthermore, Multi-Axis Turning excels in producing parts with exceptional surface finishes, a crucial aspect in industries where aesthetics, accuracy, and functionality go hand in hand. The simultaneous multi-axis movement allows for smoother tool paths, minimizing vibrations and enhancing surface quality. This capability is particularly important for critical components used in industries such as medical devices, where precision and superior finish are paramount.In recent years, a company at the forefront of Multi-Axis Turning technology has emerged - {}. With their cutting-edge machinery and industry-leading expertise, they have been instrumental in advancing the field of precision machining. Their state-of-the-art equipment boasts unmatched capabilities, offering multi-axis milling, turning, and drilling in a single setup. Moreover, their comprehensive software solutions enable seamless integration between design, simulation, and manufacturing processes, ensuring optimal results and increased efficiency.By pioneering Multi-Axis Turning, {} has revolutionized precision machining in terms of accuracy, speed, and versatility. Their commitment to innovation and continuous improvement has propelled the industry forward, enabling manufacturers to achieve new heights in manufacturing excellence. With their comprehensive range of machinery and software solutions, {} is poised to shape the future of precision machining, empowering industries worldwide.In conclusion, Multi-Axis Turning has emerged as a game-changer in the field of precision machining. Its ability to produce complex geometries, enhance surface finishes, and streamline the manufacturing process has made it indispensable for modern industries. With its wide range of applications and technological advancements, Multi-Axis Turning holds immense potential for transforming the way we manufacture and design components, setting new standards of precision and efficiency.
Exploring Versatile and Efficient Options for Rapid Prototyping
Rapid Prototyping Options: Revolutionizing Prototyping ServicesIn today's competitive business environment, companies are constantly pushing the boundaries of innovation to stay ahead of the curve. One critical aspect of this innovation is rapid prototyping, which is essential for designing and testing new products. To remain competitive, companies need agile and efficient prototyping services that produce high-quality, functional prototypes at a rapid pace. That's where Rapid Prototyping Options (need to remove brand name) comes in.Rapid Prototyping Options (RPO) is a leading provider of rapid prototyping services that cater to a diverse range of industries, including aerospace, automotive, medical, and consumer products. With over a decade of experience in the industry, the company has consistently provided high-quality, cost-effective prototyping services that have helped clients accelerate innovation and bring products to market faster.At the heart of RPO's success is its commitment to using cutting-edge technology and advanced manufacturing techniques in its prototyping services. The company combines traditional manufacturing methods with innovative technologies like 3D printing, CNC machining, and injection molding to produce customized, high-quality prototypes that accurately represent the final product.RPO's 3D printing capabilities are among the most advanced in the industry. The company leverages a variety of 3D printing technologies, including Fused Deposition Modeling (FDM), Stereolithography (SLA), and Selective Laser Sintering (SLS), to produce accurate, high-resolution prototypes. These prototypes can be made from a variety of materials, including plastic, metal, and even rubber, depending on the client's specific requirements.Another critical prototyping service offered by RPO is CNC machining. The company's state-of-the-art CNC machines can produce high-quality prototypes from a variety of materials, including metals, plastics, and composites. RPO's CNC machining capabilities allow clients to produce prototypes with precise dimensions and complex geometries, making it an ideal solution for industries like aerospace and automotive, where precision and accuracy are critical.For larger production runs, RPO offers injection molding services. The company's injection molding capabilities allow clients to produce high-quality, injection-molded parts quickly and efficiently. With RPO's injection molding services, clients can avoid the high startup costs associated with traditional injection molding and quickly produce functional, high-quality parts without sacrificing quality.One key aspect of RPO's prototyping services that sets it apart from competitors is its focus on customer service. The company's prototyping experts work closely with clients throughout the prototyping process to ensure that their needs are met and their expectations are exceeded. From initial consultations to prototyping design to final production, RPO is committed to providing world-class prototyping services that meet the highest standards of quality, accuracy, and reliability.RPO's prototyping services have been critical to its clients' success, allowing them to accelerate innovation, refine product designs, and reduce time-to-market. For example, RPO's prototyping services provided critical support to a medical device manufacturer that needed to produce functional prototypes for testing their devices' safety and effectiveness. RPO's 3D printing and CNC machining capabilities enabled the manufacturer to produce accurate, high-quality prototypes quickly and efficiently, helping to reduce product development timelines and costs.Overall, Rapid Prototyping Options is revolutionizing the prototyping landscape, providing efficient, cost-effective prototyping services that enable companies to innovate at a rapid pace. With a focus on cutting-edge technology, precision, and customer service, RPO is committed to helping companies accelerate innovation, optimize product design, and bring products to market faster. Whether you're in aerospace, automotive, medical, or any other industry, RPO's prototyping services can help you take your innovation to the next level.
Discover the Latest News on Precision CNC Machining Parts
article:CNC Machining Parts Proves to be an Essential Resource for Precision EngineeringFor many decades, the manufacturing industry has relied on CNC machines to produce high-quality end products with a precision-level of accuracy. Among these machines, CNC Machining Parts have become a fundamental resource to aid in the production of high-performance products that meet strict manufacturing specifications. In today's competitive market, achieving success in precision engineering depends on having access to the latest cutting-edge technology. This is where CNC Machining Parts come in, proving to be an essential resource that has transformed the manufacturing industry, providing a step up in the production of the highest-grade products.CNC Machining Parts are CNC-machined components that have been specifically designed to meet the stringent demands of various industries. They are produced to the most exacting standards of quality and durability, ensuring that they offer the best performance under tough and demanding circumstances. These parts are made from high-quality materials like metals, plastics, and composites that ensure that they can withstand the pressures of modern production environments.CNC Machining Parts have been designed to operate with a high degree of precision, accuracy, and reliability. CNC machines, which produce these parts, are run by computers, delivering the highest level of control and accuracy over the manufacturing process. They are programmed to perform a series of highly precise movements that create the desired end product, guaranteeing the highest levels of quality in every component produced. The CNC production process is incredibly fast and efficient, allowing for the manufacturing of large quantities of parts in a short amount of time.The CNC Machining Parts produced by {} are some of the most sophisticated and advanced in the industry. Featuring cutting-edge technology and materials, these parts have been developed to withstand the most demanding of conditions and environments. The company's production process involves the use of state-of-the-art computer-controlled machinery. The automation of this manufacturing process ensures that each part produced is a high-quality, durable component that meets the strictest demands of the manufacturing industry.CNC Machining Parts have a broad scope of applications across a range of industries. They are used in many diverse fields such as aerospace, electronics, automotive, marine, and medical industries, to mention a few. In the aerospace industry, for instance, these parts are used in the manufacture of aircraft parts, ensuring that they are highly durable and can withstand the rigors of high-altitude flight. In the automotive industry, CNC Machining Parts are used in the production of engine components, ensuring that they are efficient and can withstand high temperatures and robust driving conditions.In the medical industry, CNC Machining Parts have become instrumental in the production of high-quality medical devices and equipment. These machines produce precision components for use in surgical instruments, prosthetics, hearing aids, and other medical devices that require precise measurements. The efficiency of CNC Machining Parts has made the production of these components more accessible, cheaper, and faster, thereby improving the medical industry's level of quality.CNC Machining Parts have become essential in modern-day manufacturing. They have transformed the way manufacturing is done, offering higher levels of precision, reliability, and consistency, resulting in better-performing products. The CNC Machining Parts produced by {} are some of the best in the business and come highly recommended by satisfied customers. The company's emphasis on quality, value, and customer service has made them a leader in the industry. By utilizing cutting-edge technology, top-quality materials, and a team of skilled engineers, the company has set itself apart from its competitors, providing superior CNC Machining Parts that meet the stringent demands of various industries.In conclusion, CNC Machining Parts have become an essential resource for precision engineering. They have revolutionized the manufacturing industry by offering the highest level of precision, accuracy, and consistency, thereby producing the highest quality products. The CNC Machining Parts produced by {} are among the best on the market, utilizing state-of-the-art technology, efficient production processes, and high-quality materials. The company's focus on quality, customer service, and innovation has made it a standout performer in the industry, providing the best products and services that meet the needs of customers around the world.
What is Water-jet Technology? A Definition
Water-jet Technology Takes the Industrial World by StormWater-jet technology has been quietly revolutionizing the industrial world over the past decade. Driven by powerful streams of water and sometimes abrasive materials, water-jet cutting technology is quickly becoming the go-to cutting method for a variety of industries. From aerospace to the medical field, water-jet cutting is proving to be more precise and efficient than traditional cutting methods.A water-jet is a cutting tool that creates a high-velocity jet of water, usually mixed with an abrasive material. This creates a powerful cutting force that can cut through virtually any material with precision, including metal, stone, glass, and plastic. Water-jet cutting technology was developed in the 1950s, and since then, it has been continuously refined and improved, becoming one of the most versatile and effective cutting methods available today.One of the many benefits of water-jet cutting is its precision. Unlike traditional cutting methods that rely on brute force and sharp blades, water-jet cutting relies on a powerful stream of water to slice through materials with ease. This allows for incredibly intricate and precise cuts, even on difficult or complicated materials.Another benefit of water-jet cutting is its versatility. Water-jet cutters can handle a wide range of materials, from soft rubber to thick steel. This makes it an ideal choice for industries that require cutting precision on a variety of materials.The aerospace industry, for example, heavily relies on water-jet technology for the precision cutting of parts and components. With water-jet cutting, aerospace manufacturers can create intricate shapes out of tough materials such as titanium and composites, resulting in stronger, lighter-weight aircraft that perform better than ever before. Other industries, such as the medical field, also rely on water-jet cutting for precision cutting of surgical instruments and implantable devices.Water-jet cutting technology has also become more accessible in recent years, with more and more companies offering water-jet cutting services to a variety of industries. Companies like {} offer state-of-the-art water-jet cutting services that can handle large production runs or small, custom projects. By outsourcing their cutting needs, businesses can save time and money on equipment and maintenance costs while still enjoying the precision and versatility of water-jet cutting.Finally, water-jet cutting is also environmentally friendly. Unlike traditional cutting methods that produce harmful dust and debris, water-jet cutting creates minimal waste and leaves the material clean and untouched. This means less waste, fewer environmental hazards, and a safer workplace for employees.In conclusion, water-jet cutting technology is quickly becoming the go-to cutting method for businesses ranging from aerospace to medical manufacturing. With its precision, versatility, accessibility, and environmentally friendly benefits, water-jet cutting is the perfect solution for industries that require precise cutting of a variety of materials. As technology continues to improve, we can only expect to see water-jet cutting become even more essential to the industrial world.
MTConnect-Ready 3D Printer for Aerospace and Production Applications
, MTConnect, FDM, aerospace, production, 3D printing.Additive Manufacturing Magazine recently reported that the Stratasys Fortus 900 3D printer now features an MTConnect-ready interface. This is great news for those working in aerospace and other industries that require high-quality, production-grade 3D printing.The Stratasys Fortus 900 is a Fused Deposition Modeling (FDM) 3D printer designed for large, complex parts. With a build volume of 36 x 24 x 36 inches, it has the capability to produce parts that are larger than those typically produced with plastic extrusion machines. This makes it an ideal choice for aerospace applications, as well as for producing jigs, fixtures, and tooling.Incorporating the MTConnect protocol into the Stratasys Fortus 900 means that users can now monitor and control their 3D printing operations in real time. MTConnect is an open, royalty-free standard for machine tool communication that has become increasingly popular in the manufacturing industry. With MTConnect, users can easily connect machines and devices to a network, allowing them to monitor data and make informed decisions about their operations.For aerospace manufacturers, the Stratasys Fortus 900 with MTConnect-ready interface is ideal, as it provides the capability to produce production-grade parts with repeatable accuracy. Additionally, 3D printing allows for the production of complex geometries that cannot be produced with traditional manufacturing methods.Overall, the integration of MTConnect into the Stratasys Fortus 900 3D printer is a positive development for the additive manufacturing industry. By providing real-time monitoring and control, it enables users to optimize their operations, increase efficiency, and improve the quality of their products. This is especially important in industries such as aerospace, where high-quality, production-grade parts are essential.As the use of 3D printing continues to grow, we can expect to see further developments in this area, and the integration of other technologies into 3D printers. In the meantime, the Stratasys Fortus 900 with MTConnect-ready interface is a great option for those looking to produce high-quality, production-grade parts with 3D printing technology.
Revolutionizing Manufacturing: Streamline Production with Custom Industrial Design Parts
Build Parts For Industry Design Expands Its Capabilities to Serve Diverse Industrial SectorsBuild Parts For Industry Design, a leading provider of high-quality industrial parts and services, is proud to announce the expansion of its capabilities to better cater to the needs of diverse industrial sectors. With its state-of-the-art facilities and cutting-edge technology, the company aims to deliver innovative solutions and meet the demands of an ever-evolving market.Established in [year], Build Parts For Industry Design has become a trusted name in the industrial design and manufacturing industry. With a team of experienced engineers, designers, and technicians, the company has successfully served various clients across different sectors, including automotive, aerospace, electronics, and consumer goods.Understanding the changing dynamics of the industrial landscape, Build Parts For Industry Design has strategically invested in its facilities to ensure it remains at the forefront of innovation. By leveraging the latest technologies and continuously upgrading its equipment, the company is well-equipped to deliver parts that meet the highest industry standards.One of the key factors that sets Build Parts For Industry Design apart from its competitors is its commitment to precision and quality. The company follows rigorous quality control processes at every step of the manufacturing process to ensure that the parts it produces are of the finest quality. By adhering to industry-leading standards, Build Parts For Industry Design aims to provide its clients with reliable and durable parts that can withstand even the most demanding conditions.Build Parts For Industry Design also places great emphasis on customization and flexibility. The company understands that each industrial sector has its own unique needs and requirements. With its expanded capabilities, Build Parts For Industry Design can now offer tailor-made solutions to meet the specific demands of different industries. Whether it's designing intricate components for the aerospace industry or manufacturing precision parts for the automotive sector, the company has the expertise and resources to deliver exceptional results.In addition to its commitment to quality and customization, Build Parts For Industry Design is also dedicated to sustainable practices. The company recognizes the importance of minimizing its environmental impact and actively seeks out eco-friendly manufacturing processes. By investing in advanced technologies that reduce waste and optimize energy consumption, Build Parts For Industry Design ensures that its operations are as sustainable as possible.Customers of Build Parts For Industry Design can expect not only high-quality parts but also excellent customer service. The company takes pride in its responsive and efficient communication channels, ensuring that clients receive the support they need throughout their project. From initial design consultations to post-production assistance, Build Parts For Industry Design is committed to providing an unparalleled customer experience.As Build Parts For Industry Design expands its capabilities, it looks forward to forging new partnerships and collaborations across a wide range of industries. The company's dedication to innovation, quality, and sustainability positions it as an ideal partner for businesses looking to enhance their industrial design and manufacturing processes.With its state-of-the-art facilities and a team of skilled professionals, Build Parts For Industry Design is ready to take on new challenges and serve the diverse needs of the industrial sector. As the industry continues to evolve, the company remains committed to delivering cutting-edge solutions that drive innovation and economic growth.For more information about Build Parts For Industry Design and its range of services, please visit [website] or contact [email/phone].
Discover the Advantages of Laser Cutting in Modern Manufacturing
article:Laser Cutting Technology Makes its Way into Industrial ManufacturingIn recent years, industrial manufacturing has undergone a major transformation. The advancement in technology has brought about significant changes in processes, enabling the industry to become more efficient, faster, and more cost-effective. One of the technological advancements that have brought about significant changes in the manufacturing industry is laser cutting technology. Laser cutting technology is a process of cutting materials using laser beams. The technology has been around for some time now and has grown increasingly popular in various industries such as automotive, aerospace, construction, and textiles, among others. It is an incredibly versatile technology that can cut through a wide range of materials such as metal, plastics, wood, and fabrics.Laser cutting technology has been a game-changer for companies that require a high level of precision in their products. The technology's precision enables companies to create intricate designs and shapes that would be impossible to achieve using traditional methods. The technology has also helped to reduce production costs by minimizing material waste and increasing efficiency.One company that has been at the forefront of embracing laser cutting technology is {company name}. The company specializes in industrial manufacturing and has been using laser cutting technology to achieve precision and efficiency in its processes. {Company name} has invested heavily in the latest laser-cutting technologies, ensuring that it remains competitive in the market. The company has a team of skilled professionals who are experts in using laser-cutting technology, ensuring that their products meet the highest standards of quality.One of the advantages of laser cutting technology is its ability to cut through materials quickly and efficiently. This speed makes it possible to produce products in large volumes within a short period. {Company name} has been able to take advantage of this speed to meet the high demand for its products in the market.At {company name}, the use of laser cutting technology has enabled the company to produce high-quality products that meet the specific needs of its clients. The technology is incredibly versatile and can cut through a wide range of materials such as aluminum, stainless steel, and carbon steel, among others. This versatility has enabled the company to cater to clients from different industries with varying needs.The precision of laser cutting technology has also enabled {company name} to create intricate designs and shapes in its products. This precision has helped to set the company apart from its competitors, as it can produce products that are unique to its clients' requirements.Another advantage of laser cutting technology is its ability to minimize material waste during the manufacturing process. The technology works by focusing laser beams on the material, melting it away in a controlled manner. This process results in minimal material wastage, reducing production costs significantly. {Company name} has been able to take advantage of this capability, ensuring that it remains cost-competitive in the market.As technology continues to evolve, laser cutting is expected to become more advanced, increasing its relevance in the manufacturing industry. With laser cutting technology becoming more popular, more companies are expected to adopt it, making it an essential technology in industrial manufacturing.In conclusion, laser cutting technology has revolutionized the industrial manufacturing industry, providing significant benefits such as precision, efficiency, and cost-effectiveness. {Company name} is one of the companies that have embraced this technology, ensuring that it remains competitive in the market and meets the specific needs of its clients. The continued evolution of laser cutting technology is expected to lead to further advancements in the industry, making it an exciting time for the manufacturing industry.
China-Based Manufacturer Offers Precision CNC Machined Parts
Wintec Precision Machining Co., Ltd: Your One-Stop Solution for CNC Precision Machined ComponentsWintec Precision Machining Co., Ltd is a leading OEM/ODM manufacturer of CNC precision machined components in China. With years of experience in the industry, Wintec has emerged as a reliable and trustworthy machining partner for businesses across the globe. Our team of highly skilled engineers and technicians, along with state-of-the-art infrastructure and advanced technology, enable us to deliver high-quality machined products that are second to none.At Wintec, we operate with a customer-first approach where customer satisfaction is our top priority. We work closely with our clients to understand their specific requirements and offer customized solutions that meet their needs. We have an extensive range of machining capabilities, including CNC turning, CNC milling, and CNC grinding, to provide accurate and precise parts that meet our client's specifications.Our CNC precision machined components are made using strict quality control measures that ensure superior product performance and reliability. We use only the highest quality raw materials that are sourced from reputable suppliers to ensure that our products meet stringent industry standards. Our commitment to quality is demonstrated by our ISO 9001:2015 certification, a testament that we deliver quality products consistently.At Wintec, we offer a broad range of CNC precision machined components, including shafts, sleeves, gears, housings, and more. We specialize in producing quality parts that cater to a wide range of industries, including the automotive, aerospace, medical, and energy sectors. Our machining capabilities allow us to create parts with intricate designs, intricate surface finishes, and tight tolerances that meet our client's exacting requirements.As a China-based manufacturer, Wintec offers our clients a cost-effective solution that does not compromise on quality. We have an extensive network of suppliers that allows us to source the best raw materials at a competitive price, passing on the savings to our clients. Our commitment to delivering cost-effective solutions makes us an attractive partner for businesses looking to reduce their production costs without sacrificing quality.In conclusion, Wintec Precision Machining Co., Ltd is a reliable partner for businesses in need of CNC precision machined components. We offer quality products, customized solutions, and cost-effective services that meet our clients' requirements. Our commitment to customer satisfaction, quality, and integrity makes us the ideal choice for your machining needs. Contact us today to learn more about our products and services.