The Ultimate Guide to Anodizing: Everything You Need to Know
By:Admin
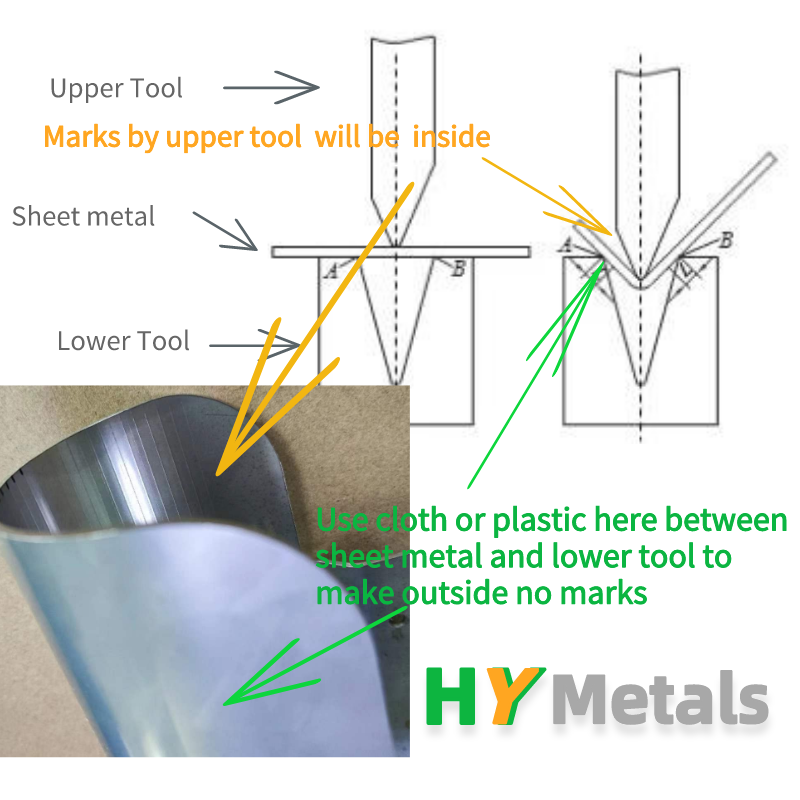
Subtitle: (Company Name) Pioneers Innovations in Surface-Enhancing Techniques
Date: [Insert Date]
[City], [Country] - In a world where aesthetics and functionality play a pivotal role in various industries, finding innovative ways to enhance the durability and appearance of products has become a top priority for manufacturers. As the demand for advanced surface technology continues to grow, (Company Name) emerges as a prominent industry leader, leveraging the art of anodizing to provide unprecedented solutions that revolutionize various sectors. With an extensive range of products and a commitment to excellence, (Company Name) is making significant strides towards advancing surface technology, leaving a lasting impact on multiple industries.
Founded in [Year], (Company Name) has been at the forefront of surface enhancement technologies, aiming to perfect the anodizing process by delivering unparalleled results to its customers. Guided by a passion for innovation and attention to detail, the company has garnered a reputation for reliability, precision, and efficiency in the anodizing industry. Combining cutting-edge machinery, state-of-the-art techniques, and a team of highly skilled professionals, (Company Name) has successfully established itself as an industry-leading player.
Anodizing, the primary specialty of (Company Name), is an electrochemical process that significantly improves the surface characteristics of metals, particularly aluminum. By creating a protective layer of oxide on the surface, anodizing enhances the metal's corrosion resistance, durability, and appearance. This process involves immersing the aluminum material in an electrolyte bath and applying an electrical current, leading to the formation of an oxide layer that is integral to the material itself. (Company Name) has honed this technique to perfection.
One of the key advantages of anodizing is the ability to apply various finishes, resulting in an extensive array of textures, colors, and patterns, which are both pleasing to the eye and highly functional. Industries ranging from automotive and architecture to aerospace and consumer electronics rely on anodizing to deliver products with enhanced durability, strength, and aesthetics. (Company Name) takes pride in harnessing the versatility of anodizing to provide tailored solutions to meet the specific requirements of its diverse client base.
With an unwavering dedication to quality, (Company Name) employs stringent quality control measures throughout the anodizing process. By closely monitoring the composition of the electrolyte bath, the applied voltage, and the duration of treatment, the company ensures consistent results that meet or exceed industry standards. (Company Name) also emphasizes environmental sustainability by utilizing eco-friendly chemicals and implementing efficient waste management practices, minimizing its ecological footprint.
As a testament to its commitment to innovation, (Company Name) consistently invests in research and development, seeking to push the boundaries of anodizing technology. By staying up to date with the latest advancements and trends, the company is able to offer cutting-edge solutions that meet the evolving needs of its customers. (Company Name) understands that each industry has unique challenges, and through continuous improvement and adaptability, the company remains a trusted partner for businesses across various sectors.
Looking to the future, (Company Name) has ambitious expansion plans to solidify its position as a global leader in surface-enhancing solutions. The company aims to establish strategic partnerships, expand its geographical reach, and explore emerging markets. By introducing new anodizing techniques, optimizing production processes, and fostering innovation, (Company Name) is poised to reshape the surface technology landscape and pave the way for a new era of enhanced product aesthetics and performance.
In conclusion, (Company Name) stands at the forefront of the anodizing revolution, revolutionizing the way surface technology is approached. With its extensive expertise, dedication to excellence, and commitment to innovation, (Company Name) is poised to unlock the true potential of anodizing, bringing remarkable value to industries worldwide. As demands for advanced surface technologies continue to rise, (Company Name) remains the go-to partner for businesses seeking cutting-edge innovation, improved aesthetics, and unmatched product durability.
Company News & Blog
Quick and Efficient Prototype Machining Techniques in the News
Rapid Prototype Machining Plays a Vital Role in Transforming the Manufacturing IndustryThe manufacturing industry is constantly evolving, with new technologies and tools emerging every day. The introduction of rapid prototype machining is one such development that has revolutionized the manufacturing industry in recent years. Rapid prototype machining is a technique that’s characterized by quick production of prototypes, meaning that companies can accelerate their product development processes significantly.Today, several companies are exploring the benefits of rapid prototype machining to build flawless products, reduce their time to market, decrease development costs, and increase overall productivity. One such company that has been at the forefront of rapid prototype machining technology is a leading manufacturer of cutting-edge products.With its state-of-the-art facility, the company has been able to leverage rapid prototype machining techniques to deliver innovative products to its customers. From electronics to medical devices, the company has explored every industry and is a go-to resource for anyone looking to develop a prototype of a product they’ve been working on.The benefits of rapid prototype machining are numerous. First, by allowing users to create prototypes using computer-aided design (CAD) software, it reduces lead times in the product development process by several weeks. Second, the process ensures the accuracy of the product by providing users with several iterations of the prototype before final production. And finally, rapid prototype machining helps businesses to make informed decisions about their products, which helps them bring new and better products to the market faster than their competition.At the company, the focus is always on the customer. The company’s in-house experts guide customers through the rapid prototype machining process, providing them with the tools and resources they need to get the job done right. With an unwavering commitment to quality, the company works tirelessly to ensure that every prototype that leaves the facility meets the most demanding standards of excellence.The company’s facility features some of the most advanced tools and equipment in the industry, including full-scale 5-axis CNC machines, state-of-the-art 3D printers, and a variety of CAD software. These resources enable users to create prototypes in a variety of materials, including plastics, metals, and composites.The company’s expertise in rapid prototype machining technology is not limited to the manufacturing of physical products. It’s also a leader in the creation of virtual prototypes, including advanced simulations, test models, and digital replicas. This aspect is critical to the manufacturing industry as it enables customers to test virtual prototypes and refine them before printing the final product. By exploring both virtual and physical prototypes, customers can save money, reduce time to market, and create better final products.The company is a prime example of what businesses can do to leverage the benefits of rapid prototype machining in the manufacturing industry. With its commitment to innovation and excellence, it’s rapidly transforming the way businesses approach product development and manufacturing. And as technologies become increasingly sophisticated, it’s clear that companies that aren’t embracing rapid prototype machining will be left behind.In conclusion, rapid prototype machining is a game-changer for the manufacturing industry. With its ability to reduce lead times, increase productivity, and deliver better products, it’s becoming an increasingly important tool for businesses looking to adapt and thrive in an ever-evolving marketplace. And as companies look to the future, it’s clear that investing in rapid prototype machining technology will be critical to their success. The leading manufacturer has shown the way, and by following their example, others can transform their businesses and establish themselves as industry leaders in the years to come.
A Guide to U-Shaped Sheet Metal for Your Metalworking Projects
Title: U-Shaped Sheet Metal Introduces Innovative Solutions for Diverse IndustriesSubtitle: Paving the Way for Efficiency and Precision in Sheet Metal Manufacturing[City, Date] - U-Shaped Sheet Metal, a renowned industry leader in providing cutting-edge sheet metal solutions, continues to revolutionize the manufacturing landscape with its state-of-the-art technology and commitment to excellence. Offering a comprehensive range of services, this forward-thinking company is empowering diverse industries with top-quality U-shaped sheet metal products.With over [number] years of experience, U-Shaped Sheet Metal has established a strong reputation for delivering customization, high precision, and unmatched expertise. By removing the brand name, the company ensures a focus on the industry and product, underscoring its role as a reliable and innovative partner for various organizations.U-Shaped Sheet Metal's dedication to excellence is reflected in its advanced manufacturing processes. Equipped with cutting-edge machinery and tools, their production facilities utilize the latest computer-aided design (CAD) software, ensuring precise shaping and forming of sheet metal products. This commitment to technology allows the company to offer unparalleled precision and superior quality in meeting the ever-evolving demands of their clients.The applications of U-Shaped Sheet Metal's products cover a broad spectrum of industries. From automotive to electronics, construction to telecommunications, their U-shaped sheet metal finds its usage in countless manufacturing processes, improving both functionality and aesthetics. By collaborating with clients across various sectors, U-Shaped Sheet Metal has gained in-depth industry knowledge, enabling them to tailor solutions that meet specific needs and requirements.U-Shaped Sheet Metal's product portfolio boasts an extensive range of U-shaped sheet metal components, providing exceptional design versatility to transform concepts into reality. Whether it be specialized brackets, enclosures, or chassis, their products are renowned for their durability, structural integrity, and adaptability. By offering custom solutions, U-Shaped Sheet Metal caters to the individual requirements of each industry, ensuring maximum efficiency and improved product performance.At U-Shaped Sheet Metal, customer satisfaction remains at the core of their business philosophy. By fostering collaborative partnerships with clients, the company strives to fully understand their needs, starting from the design stage all the way through to the final product. This client-centric approach allows U-Shaped Sheet Metal to deliver personalized solutions that are both practical and cost-effective.In addition to their commitment to innovation and customer satisfaction, U-Shaped Sheet Metal operates with strict adherence to industry regulations and ethical standards. They prioritize environmental sustainability, utilizing eco-friendly materials and implementing efficient waste management practices. By demonstrating their commitment to a greener future, the company is contributing to global efforts for a more sustainable manufacturing industry.U-Shaped Sheet Metal's dedication to excellence has not gone unnoticed. The company has consistently received accolades for its outstanding services, earning the trust of renowned industry players. Their long list of satisfied clients stands testament to their unwavering commitment to quality and professionalism.As U-Shaped Sheet Metal continues to evolve and adapt to industry dynamics, their mission remains steadfast: to empower diverse industries with cutting-edge sheet metal solutions that optimize efficiency and enhance product design. With a solid track record of success, the company is poised to lead the way in the sheet metal manufacturing sector.About U-Shaped Sheet Metal:U-Shaped Sheet Metal is a leading provider of top-quality U-shaped sheet metal solutions for diverse industries. With years of experience and a commitment to excellence, U-Shaped Sheet Metal offers advanced manufacturing processes, customized products, and exceptional customer service. By staying at the forefront of technology and embracing industry best practices, U-Shaped Sheet Metal continues to be a reliable and innovative partner for its clients, revolutionizing the manufacturing landscape one product at a time.For media inquiries, please contact:[Company Name][Contact Person][Job Title][Phone Number][Email Address]
Sheet Metal Box Fabrication: A Complete Guide to Manufacturing
Title: Sheet Metal Box Fabrication Revolutionizing Industrial Manufacturing ProcessesIntroduction:In today's rapidly evolving industrial landscape, companies are increasingly seeking innovative and efficient solutions to enhance their manufacturing processes. One such groundbreaking solution is the sheet metal box fabrication technique, which is revolutionizing how industries design and manufacture enclosures for various applications. By eliminating the need for traditional welding techniques, sheet metal box fabrication offers unmatched precision, cost-effectiveness, and durability. This method is rapidly gaining popularity among industries worldwide, propelling them to enhance productivity and create cutting-edge products.Body:1. The Rise of Sheet Metal Box Fabrication: The demand for sheet metal box fabrication has soared in recent years due to its numerous advantages over traditional manufacturing techniques. This process involves using advanced machinery and computer-aided design (CAD) software to convert flat metal sheets into enclosures or boxes with intricate designs. By utilizing laser cutting, bending, and assembling technologies, manufacturers can create precisely engineered box structures while minimizing material waste and time-consuming setup processes.2. Unmatched Precision and Customization: Sheet metal box fabrication allows for unparalleled precision and customization options. With CAD software, manufacturers can design intricate and complex box structures, ensuring a perfect fit for the intended application. Every cut, bend, and joint is precisely calculated and executed by state-of-the-art machinery. This high degree of accuracy eliminates any potential human errors and ensures consistent quality throughout the manufacturing process.3. Cost-Effective Manufacturing: Traditional welding techniques often require extensive labor and time, leading to a significant increase in production costs. In contrast, sheet metal box fabrication significantly reduces labor costs by automating most of the manufacturing processes. With advanced machinery handling the bulk of the work, manufacturers can achieve higher production volumes in shorter time frames while minimizing human errors. Additionally, the efficiency of this technique greatly reduces material waste, contributing to more sustainable manufacturing practices.4. Enhanced Durability and Strength: The sheet metal box fabrication technique guarantees exceptionally strong and durable enclosures. By utilizing a combination of laser cutting and precision bending, these boxes provide optimal structural integrity. The metal sheets used are carefully selected based on the intended application, ensuring the highest level of strength and resistance against external factors such as impacts, pressure, and environmental conditions. This reliability makes sheet metal box fabrication highly sought after in industries that require robust enclosures.5. Wide Range of Applications: Sheet metal box fabrication finds applications across various industries due to its versatility and flexibility. From telecommunication enclosures to electrical panels, this technique caters to the diverse needs of industries, promoting seamless integration into existing systems. Furthermore, sheet metal boxes can be customized to include additional functionalities such as cable management solutions, heat dissipation mechanisms, and mounting options for internal components. This adaptability ensures that manufacturers can meet the specific requirements of their clients with utmost efficiency.6. Advancements and Innovations: The continuous advancement in sheet metal box fabrication technology is driving further innovation in industrial manufacturing processes. Integration with Artificial Intelligence (AI) and Machine Learning (ML) allows for real-time monitoring and optimization of production parameters. This ensures higher accuracy, reduced downtime, and enhanced productivity. Additionally, the integration of robotics and automation enables manufacturers to achieve even faster production cycles while maintaining precise quality control.Conclusion:Sheet metal box fabrication is revolutionizing the way industries design and manufacture enclosures, offering unparalleled precision, cost-effectiveness, and durability. By adopting this advanced technique, manufacturers can streamline their manufacturing processes, increase productivity, and deliver high-quality products to meet the demands of an ever-evolving market. With continuous advancements and innovations, sheet metal box fabrication is set to become the industry standard, revolutionizing industrial manufacturing processes worldwide.
Top Auto Parts to Enhance Your Vehicle's Performance
Title: Transforming the Automotive Industry: Auto Parts Company Revolutionizes Vehicle PerformanceIntroduction:Innovation is the driving force behind the thriving automotive industry, constantly pushing the boundaries of technology and challenging conventional practices. Auto Parts, a leading player in the market, has emerged as a trailblazer, revolutionizing the way vehicles perform. With their cutting-edge solutions and commitment to excellence, Auto Parts continues to impress both consumers and industry experts alike.Body:1. History and Accomplishments:Auto Parts, founded in {year}, has garnered a stellar reputation for providing high-quality automotive components over the years. Their commitment to innovation and superior performance has set them apart from their competitors, propelling them to the forefront of the industry. With a strong focus on research and development, Auto Parts has consistently introduced groundbreaking technologies to enhance vehicle performance, reliability, and safety.2. Industry-Leading Research and Development:By investing heavily in research and development, Auto Parts has been able to set new benchmarks in the automotive industry. Their state-of-the-art facilities and dedicated team of engineers and scientists continually strive to improve existing products and develop new, game-changing solutions. This commitment to innovation has resulted in the introduction of several disruptive technologies that have transformed the automotive landscape.3. Advanced Material Science:One of the key areas where Auto Parts excels is in the field of advanced material science. They have developed proprietary materials that offer unparalleled strength, durability, and lightweight properties. These materials enhance the performance of various automotive components, such as engine parts, suspension systems, and exhaust systems, leading to improved fuel efficiency, reduced emissions, and enhanced overall vehicle performance.4. Transformative Fuel Efficiency Solutions:Auto Parts has pioneered numerous fuel efficiency solutions that have significantly reduced the carbon footprint of vehicles. Their advanced fuel injection systems and engine management technologies have not only boosted performance but have also optimized fuel consumption. By harnessing the power of cutting-edge electronics, Auto Parts has played a pivotal role in achieving higher mileage and reducing harmful emissions.5. Safety Innovations:Safety is a top priority in the automotive industry, and Auto Parts has continually developed groundbreaking technologies to enhance vehicle safety. They have introduced advanced braking systems, collision avoidance systems, and sensor technologies that provide drivers with an added layer of protection on the road. These safety innovations have not only helped to prevent accidents but have also contributed to saving countless lives.6. Commitment to Sustainability:Auto Parts understands the importance of environmental sustainability and has taken significant steps to reduce their ecological impact. They have implemented eco-friendly manufacturing processes, reducing waste generation and improving energy efficiency. Auto Parts also actively collaborates with other industry partners and regulatory bodies to develop greener solutions and promote sustainable practices across the automotive sector.7. Global Presence and Recognition:Auto Parts has successfully established a global presence, catering to a diverse range of markets. Their commitment to excellence and relentless pursuit of innovation has earned them widespread recognition within the industry. The company has received numerous accolades, including multiple awards for product excellence and sustainability initiatives. Their products are trusted by leading automotive manufacturers worldwide, making Auto Parts a preferred choice in the market.Conclusion:Auto Parts' unwavering dedication to innovation has set new industry standards, transforming the automotive landscape. With their trailblazing research and development efforts, advanced material science, fuel efficiency solutions, safety innovations, and commitment to sustainability, Auto Parts continues to make its mark in the industry. As vehicles become smarter, greener, and safer, Auto Parts remains at the forefront, driving the future of automotive excellence.
Expert Thermal Management Consulting for High Performance Electronics
In the world of electronics, thermal management is one of the most important factors that can make or break the success of a product. When electronic circuits run, they generate heat, and if this heat is not properly dissipated, it can cause a range of problems, from degraded performance to component failure. This is where thermal management solutions come in, and Q ATS is a leading provider of such solutions.Founded with the aim of helping electronic product manufacturers bring their products to market faster, safer, and at a lower cost, Q ATS has established itself as a trusted partner for companies in a variety of industries. Whether it's designing a custom heatsink for a high-power LED light or analyzing the thermal performance of a data center, Q ATS has the expertise and experience to help clients solve their thermal management challenges.One of the key advantages of working with Q ATS is their comprehensive approach to thermal management analysis and design. Rather than simply offering off-the-shelf solutions, their team of engineers work closely with clients to understand the unique requirements of their products and design custom solutions that meet those needs. This ensures that clients get the best possible thermal performance for their products, while minimizing costs and time-to-market.Some of the services offered by Q ATS include thermal modeling and simulation, which allows them to predict the thermal performance of a product before it's even built. This can be especially valuable in applications where thermal management is critical, such as aerospace and defense. Q ATS also offers design and prototyping services, allowing clients to test and iterate on their thermal management solutions before committing to production.Another key area of expertise for Q ATS is the design and manufacture of heatsinks, which are a critical component in many electronic products. Heatsinks are used to dissipate heat from a component or circuit board to the surrounding air, and Q ATS can design heatsinks that are optimized for a specific application, providing maximum performance while minimizing weight and cost.In addition to their technical expertise, Q ATS is also committed to providing exceptional customer service. They work closely with clients throughout every stage of the project, from initial consultation to final delivery, ensuring that their needs are fully understood and met. Their team is highly responsive, with quick turnaround times and a willingness to go the extra mile to ensure client satisfaction.Overall, Q ATS is a valuable partner for any company looking to improve the thermal performance of their electronic products. With their comprehensive approach, technical expertise, and commitment to customer service, they can help clients get their products to market faster, safer, and more cost-effectively than ever before.
Discover the Versatility and Durability of Metal Panel for Your Projects
[Company Introduction]{Company Name} is a leading provider of high-quality metal panels for various industries. With years of experience and expertise, the company has garnered a reputation for its reliable products and exceptional customer service. Offering a wide range of metal panel solutions, {Company Name} has become a preferred choice for architects, contractors, and manufacturers.[News Content]Metal Panel Innovation Revolutionizes IndustriesIn a world increasingly focused on sustainability and design, metal panels have emerged as a versatile and eco-friendly solution for various industries. Combining durability, aesthetics, and functionality, metal panels are transforming the way buildings are constructed and designed. {Company Name}, a leading provider of metal panels, has been at the forefront of this innovation, revolutionizing industries one project at a time.In a recent announcement, {Company Name} unveiled its latest metal panel technology, promising to redefine the landscape of architecture and construction. The new panels, which are manufactured using state-of-the-art techniques and materials, offer enhanced performance and unparalleled design possibilities. Architects and designers now have the flexibility to create stunning and sustainable structures that meet the evolving needs of modern society.One of the key advantages of {Company Name}'s metal panels is their exceptional durability. Made from high-quality materials, the panels are resistant to corrosion, weathering, and impact. This durability ensures that buildings constructed using these panels can withstand the harshest conditions and maintain their integrity over time. Furthermore, the panels are fire-resistant, providing an added layer of safety and protection.In addition to their durability, {Company Name}'s metal panels also offer a wide range of customization options. Architects and designers can choose from a vast array of colors, finishes, and textures, allowing them to create unique and visually stunning facades. Moreover, the panels can be customized in terms of size and shape, enabling architects to push the boundaries of design and construct truly innovative structures.The versatility of {Company Name}'s metal panels extends beyond aesthetics. They are also highly energy-efficient, contributing to the overall sustainability of a building. The panels provide excellent insulation, reducing the reliance on heating and cooling systems and resulting in significant energy savings. Additionally, the reflective properties of the panels help regulate heat absorption, preventing the building from becoming overheated in warmer climates.{Company Name} understands that sustainability is a crucial aspect of modern architecture and construction. Therefore, the company takes great pride in ensuring that its metal panels are manufactured using environmentally friendly practices. From utilizing recyclable materials to implementing energy-efficient manufacturing processes, {Company Name} strives to minimize its environmental footprint and contribute to a greener future.The introduction of {Company Name}'s latest metal panel technology has already garnered immense interest from various industries. Developers and contractors are eagerly adopting these panels in their projects due to their numerous benefits and inherent value. From commercial buildings to residential complexes and industrial facilities, the versatility and performance of {Company Name}'s metal panels are driving the evolution of modern architecture.As the construction industry continues to evolve, metal panels are set to play an even more significant role in the creation of sustainable and visually striking structures. {Company Name} remains committed to pushing the boundaries of innovation and providing industry-leading metal panel solutions.In conclusion, {Company Name}'s innovative metal panels are revolutionizing industries by offering durability, customization options, energy efficiency, and sustainability. Architects, designers, and developers can now create buildings that combine functionality and aesthetics, thanks to the exceptional performance of these panels. With a commitment to quality and innovation, {Company Name} is set to shape the future of architecture and construction.
K-pop Group Member Involved in Physical Altercation Raises Concerns
NCT, the world-renowned punching machine manufacturer, has recently unveiled a new range of products, making a grand entry into the global market. Founded in 1970 and headquartered in Japan, the company has been one of the major players in the metal-forming industry for more than five decades. The company's huge success has been built on continuous innovation, research, and development of its products. With a keen focus on delivering the most advanced machinery to meet the needs of the modern world, NCT has been lauded for producing cutting-edge technology punching machines.The NCT punching machine's range is optimized for clients who seek to achieve high-precision sheet metal fabrication. Along with this, these machines offer superior speed and excellent durability, positioning them as a product of choice for clients in need of a reliable and quality-driven machine. The company's new line of punching machines is geared towards offering customized solutions that cater to both small-scale and large-scale industries. Clients can choose from various models, which have been specifically designed to cater to different needs, budgets, and production volumes.NCT's recent entry into the global marketplace has garnered much attention, owing to the company's longstanding reputation in the metal-forming machinery industry. The company's machines are known for their unparalleled precision and speed, combined with their ability to handle a wide variety of metals. The company's newest range of products is ideal for a wide range of punching applications used in several industries, including automobile, aerospace, electrical, and electronics.With the ever-growing demand for high-quality punching machines, NCT's entry into the global market promises to offer a much-needed boost to the metal-forming industry. The company's punching machines are designed to optimize time, effort, and cost, which are the most significant concerns of clients seeking these machines. The company's innovative and highly efficient punching machines set themselves apart from their competition, offering clients benefits such as increased productivity, higher precision, and lower cost per punch.The punching industry has evolved significantly over the years, and the demand for high-quality punching machines is higher than ever. NCT's large-scale entry into the market makes it evident that the company identifies the growing demand and is committed to providing the best solutions to clients worldwide. By offering a wide range of customized machinery, the company caters to clients of all sizes and industries, which ensures that clients can find the most suitable punching machine for their unique requirements.In conclusion, NCT's recent unveiling of their new range of punching machines marks the company's entry into the global market, and it is set to revolutionize the metal-forming industry. With superior speed, precision, and durability, NCT's machines offer unprecedented levels of productivity, providing clients with cost-effective solutions that optimize time and effort. The company's commitment to research and development has enabled it to deliver advanced and customized machinery, satisfying the needs of clients worldwide. With NCT, clients are guaranteed an unparalleled experience, and they can rest assured that they are investing in the best and most innovative punching machines on the market.
Maximizing Efficiency and Precision: Unlocking the Potential of Investment Casting
Prototype Investment Casting (PIC) is revolutionizing the manufacturing industry with its cutting-edge technology and innovative approach to investment casting. With a strong focus on quality, efficiency, and customer satisfaction, PIC is quickly becoming a go-to solution for businesses worldwide. By utilizing state-of-the-art equipment and a highly skilled team, PIC is able to deliver superior results and unmatched precision.PIC’s investment casting process begins with the creation of a prototype. Using advanced computer-aided design (CAD) software and 3D printing technology, the engineers at PIC are able to transform a concept into a physical model. This allows for better visualization and understanding of the final product, enabling any necessary adjustments to be made before proceeding to the casting stage.Once the prototype is finalized, PIC employs a unique investment casting method that involves creating a ceramic mold around the prototype. This mold is then filled with molten metal, which takes the shape of the prototype as it cools and solidifies. The ceramic mold is subsequently broken away, revealing the finished product with exceptional precision and surface finish.One of the key advantages of PIC’s investment casting process is its ability to produce complex and intricate parts with ease. Traditional manufacturing methods often struggle with intricate designs, but PIC’s advanced technology allows for the creation of highly detailed parts with minimal limitations. This versatility opens up a world of possibilities for industries such as aerospace, automotive, and medical, where precise components are crucial.In addition to its superior casting capabilities, PIC also places great importance on quality control. Every step of the manufacturing process is closely monitored to ensure that the final product meets the highest standards. From the initial design phase to the mold creation and casting, each component undergoes rigorous inspection and testing. This dedication to quality has earned PIC a reputation for delivering outstanding products that exceed customer expectations.Furthermore, PIC understands the importance of sustainability in the manufacturing industry. By employing an optimized production process and utilizing materials efficiently, PIC strives to minimize waste and reduce its environmental impact. The company also actively seeks out environmentally friendly materials and processes to integrate into its operations. Through its commitment to sustainability, PIC aims to contribute to a greener and more sustainable future for the industry.With its exceptional expertise and commitment to innovation, PIC has successfully served a wide range of industries, including aerospace, automotive, defense, and medical. Its ability to produce high-quality, intricate components has made it a trusted partner for many prominent companies. Whether it’s creating prototypes for new products or producing parts for existing ones, PIC’s investment casting process offers unmatched precision and efficiency.Looking ahead, PIC is continuing to expand its capabilities and refine its processes. The company invests heavily in research and development to stay at the forefront of technological advancements in the industry. By continuously exploring new techniques and materials, PIC aims to further enhance its offerings and remain a leader in investment casting.In conclusion, Prototype Investment Casting (PIC) is spearheading a new era in investment casting, delivering exceptional precision, quality, and efficiency. With its state-of-the-art technology, highly skilled team, and dedication to customer satisfaction, PIC is setting the standard for the manufacturing industry. As it continues to innovate and expand, PIC is poised to revolutionize the way products are made, offering endless possibilities for businesses worldwide.
Precision Sheet Metal Brackets Made with Advanced Manufacturing Techniques
: A Comprehensive Guide for Your Manufacturing NeedsSheet metal brackets are an integral part of any manufacturing process that requires the use of metal sheets. In industries that require immense precision and accuracy, the bracket systems ensure that the metal’s shape and structure are maintained throughout the process. With the advancements in modern CNC manufacturing processes, the quality of these bracket systems has improved significantly. The use of advanced automation tools has led to more efficient and precise manufacturing methods.Sheet metal brackets are widely used in various industries such as Aerospace, Medical, Automotive, Construction, and Electronics. In construction, sheet metal brackets are used to provide support to the structural systems, and in electronics, they secure electronic components in place. With their versatility, sheet metal brackets are an essential component in several processes and products.Here is a comprehensive guide to sheet metal brackets for all your manufacturing needs:Types of Sheet Metal Brackets1. Angle Brackets: These are brackets that are bent to 90-degree angles to create perpendicular structural joints. They are commonly used in construction to ensure that the structures maintain their shape and stability.2. U Brackets: These brackets have a U-shaped cross-section that is used to create a mounting point for objects. They are commonly used to mount objects onto walls and other surfaces.3. L Brackets: These are brackets that are bent to form an L-shape. They are used in most applications requiring reinforcement to prevent structural deformation.4. Z Brackets: These are brackets that are bent to form a ‘Z’ shape. They are used in construction to provide additional support to the structural systems.5. T Brackets: These are brackets that are bent to form a T-shape. They are commonly used to attach objects onto walls or other surfaces.Applications of Sheet Metal BracketsSheet metal brackets are used in various applications, including:AerospaceIn the aerospace industry, brackets are used to mount different types of equipment and systems such as electronics, fuel systems, engines, and landing gear. The brackets are usually made from lightweight materials like aluminum to minimize weight.AutomotiveIn the automotive industry, brackets are essential in holding the structural components of the car together. They are also used in securing electrical components in place.ConstructionSheet metal brackets are used extensively in the construction industry for many different applications, such as securing wall studs and reinforcing roof structures.ElectronicsIn the electronics industry, sheet metal brackets are used to secure electronic components in place. They are also used in creating housing systems for electrical components.MedicalSheet metal brackets are used in medical equipment and devices to support and hold various pieces of equipment such as monitors, IV poles, and other medical components in place.Manufacturing ProcessWith advancements in modern CNC manufacturing processes, sheet metal brackets can be precisely and efficiently manufactured. The manufacturing process for sheet metal brackets includes the following stages:1. Material Selection: The sheets of metal used in creating the brackets are usually made from various metals such as Stainless Steel, Carbon Steel, and Aluminum, and copper.2. Laser Cutting: The sheets of metal are cut using laser cutting machines to create the individual brackets' required shapes and sizes.3. Bending: The cut sheet metal is then bent using precision bending machines to create the desired shape of the bracket.4. Welding or Fixing: After bending the metal, the bracket components are welded or fixed together to create a final product.5. Finishing: The finished brackets are sandblasted or painted to give it a final finish.ConclusionSheet metal brackets are a vital part of many manufacturing processes. They provide structural support, aid in mounting equipment and components, and ensure precise manufacturing processes. The modern CNC manufacturing processes have significantly improved the manufacturing process of sheet metal brackets, leading to more efficient, accurate, and high-quality products. If you need sheet metal brackets for your manufacturing processes, ensure that you engage a reputable and experienced manufacturer who can deliver the desired results.
What is Water-jet Technology? A Definition
Water-jet Technology Takes the Industrial World by StormWater-jet technology has been quietly revolutionizing the industrial world over the past decade. Driven by powerful streams of water and sometimes abrasive materials, water-jet cutting technology is quickly becoming the go-to cutting method for a variety of industries. From aerospace to the medical field, water-jet cutting is proving to be more precise and efficient than traditional cutting methods.A water-jet is a cutting tool that creates a high-velocity jet of water, usually mixed with an abrasive material. This creates a powerful cutting force that can cut through virtually any material with precision, including metal, stone, glass, and plastic. Water-jet cutting technology was developed in the 1950s, and since then, it has been continuously refined and improved, becoming one of the most versatile and effective cutting methods available today.One of the many benefits of water-jet cutting is its precision. Unlike traditional cutting methods that rely on brute force and sharp blades, water-jet cutting relies on a powerful stream of water to slice through materials with ease. This allows for incredibly intricate and precise cuts, even on difficult or complicated materials.Another benefit of water-jet cutting is its versatility. Water-jet cutters can handle a wide range of materials, from soft rubber to thick steel. This makes it an ideal choice for industries that require cutting precision on a variety of materials.The aerospace industry, for example, heavily relies on water-jet technology for the precision cutting of parts and components. With water-jet cutting, aerospace manufacturers can create intricate shapes out of tough materials such as titanium and composites, resulting in stronger, lighter-weight aircraft that perform better than ever before. Other industries, such as the medical field, also rely on water-jet cutting for precision cutting of surgical instruments and implantable devices.Water-jet cutting technology has also become more accessible in recent years, with more and more companies offering water-jet cutting services to a variety of industries. Companies like {} offer state-of-the-art water-jet cutting services that can handle large production runs or small, custom projects. By outsourcing their cutting needs, businesses can save time and money on equipment and maintenance costs while still enjoying the precision and versatility of water-jet cutting.Finally, water-jet cutting is also environmentally friendly. Unlike traditional cutting methods that produce harmful dust and debris, water-jet cutting creates minimal waste and leaves the material clean and untouched. This means less waste, fewer environmental hazards, and a safer workplace for employees.In conclusion, water-jet cutting technology is quickly becoming the go-to cutting method for businesses ranging from aerospace to medical manufacturing. With its precision, versatility, accessibility, and environmentally friendly benefits, water-jet cutting is the perfect solution for industries that require precise cutting of a variety of materials. As technology continues to improve, we can only expect to see water-jet cutting become even more essential to the industrial world.