How steel bending is revolutionizing the manufacturing industry
By:Admin
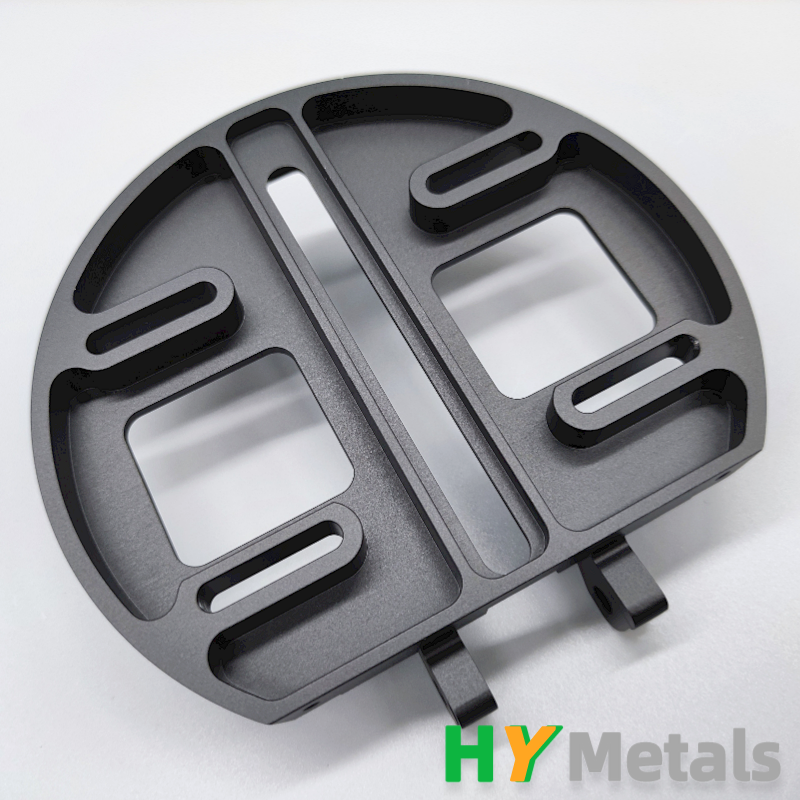
{} is proud to announce a groundbreaking innovation in the steel industry with the introduction of a revolutionary steel bending technology. This new development promises to revolutionize the way steel is handled and shaped, setting a new standard for efficiency and precision in the manufacturing process.
The new steel bending technology, developed by a team of experts at {}, represents a major advancement in the industry. With this innovation, {}, a leading name in the steel manufacturing sector, is well-positioned to further solidify its position as a leader in the industry.
This cutting-edge technology allows for the bending of steel with unprecedented accuracy and efficiency, ensuring that each piece of steel is precisely shaped according to specifications. This level of precision is crucial in industries such as construction and manufacturing, where the structural integrity of steel components is paramount.
The new steel bending technology also offers significant advantages in terms of speed and cost-efficiency. By streamlining the bending process, {} can significantly reduce production times, leading to faster turnaround times for customer orders. This increased efficiency also translates to cost savings, allowing {} to offer competitive pricing without compromising on quality.
The introduction of this innovation underscores {}'s commitment to pushing the boundaries of what is possible in the steel industry. With a track record of delivering high-quality steel products to a wide range of industries, {} continues to invest in cutting-edge technologies that set new benchmarks for excellence.
In addition to the technological advancements, {}'s steel bending process is also environmentally friendly. By reducing waste and optimizing production processes, {} is minimizing its environmental footprint and contributing to sustainability efforts in the industry.
"We are thrilled to introduce this game-changing steel bending technology to the market," said {}'s CEO. "This innovation is a testament to our commitment to driving progress and delivering the best possible products to our customers. With this new technology, we are confident that we can meet the evolving needs of the industry and continue to raise the bar for excellence in steel manufacturing."
The introduction of this innovative steel bending technology comes at a time of rapid growth for {}. The company has been gaining momentum in the market, expanding its client base and strengthening its reputation as a trusted provider of high-quality steel products.
Looking ahead, {} plans to continue investing in research and development to further enhance its technological capabilities and maintain its competitive edge in the industry. By staying at the forefront of innovation, {} is well-positioned to lead the way in shaping the future of steel manufacturing.
With the introduction of this groundbreaking steel bending technology, {} is setting a new standard for precision, efficiency, and sustainability in the industry. As the company continues to push the boundaries of what is possible, it is poised to make a lasting impact on the steel manufacturing sector, delivering unparalleled value to its customers and driving progress across the industry.
Company News & Blog
Customized Heat Sink for Optimal Performance: A Guide to Choosing the Best Option
[Company Name]'s Innovative Customized Heatsink Part Revolutionizes Cooling Solutions[City, Date] - [Company Name], a leader in the field of thermal management solutions, has unveiled its game-changing customized heatsink part. This innovative product is set to revolutionize the industry by providing a highly efficient cooling solution for a wide range of applications.With the continuous advancement of electronic systems and the subsequent increase in power densities, efficient heat dissipation has become paramount. [Company Name] recognized this need and dedicated its resources to developing a state-of-the-art heatsink that offers superior cooling performance.The key to [Company Name]'s custom heatsink lies in its cutting-edge design and advanced materials. Utilizing innovative engineering techniques, the company has created a part that maximizes heat dissipation while minimizing space and weight requirements. This makes it an ideal solution for applications where size and weight are critical, such as aerospace, automotive, and military industries.The customized heatsink is manufactured using high-performance materials that excel in thermal dissipation. These materials ensure that heat is efficiently spread out throughout the heatsink, preventing hotspots from forming and ensuring optimum cooling performance. [Company Name]'s dedication to quality is evident in the precision manufacturing processes employed, guaranteeing consistent performance, durability, and reliability.Furthermore, [Company Name] has an experienced team of engineers and thermal management specialists who work closely with clients to provide customized solutions tailored to their specific requirements. By collaborating with customers, the company ensures that its custom heatsink precisely caters to the unique demands of the application, be it shape, size, or performance requirements."The introduction of our customized heatsink is a watershed moment for the industry," says [Company Name]'s CEO. "We have conducted extensive research and development to create a product that not only meets but exceeds expectations. Its impressive cooling capabilities, combined with its compact design, make it a game-changer for a multitude of industries."The benefits of [Company Name]'s custom heatsink extend beyond superior cooling performance. Its lightweight construction and compact design result in lowered power consumption and increased energy efficiency. This not only reduces costs for end-users but also contributes to a greener and more sustainable future.One of the significant applications for [Company Name]'s custom heatsink is in electric vehicles (EVs). The automotive industry is rapidly transitioning to EVs, and the demand for efficient thermal management solutions is growing exponentially. By utilizing [Company Name]'s custom heatsink, EV manufacturers can ensure optimal cooling of crucial components, leading to enhanced vehicle performance, extended battery life, and increased overall vehicle safety.The aerospace industry is another sector set to benefit significantly from [Company Name]'s breakthrough heatsink technology. In aircraft, where weight is a critical factor, [Company Name]'s lightweight, compact custom heatsink provides an ideal solution to cool critical electronic components, ensuring reliable operation even in demanding environments.In addition to EVs and aircraft, [Company Name]'s custom heatsink has the potential to find applications in various other industries, including telecommunications, data centers, medical equipment, and consumer electronics.[Company Name] has already received positive feedback from early adopters of its custom heatsink. Companies across various industries have praised the product's performance, compact design, and ability to cater to specific application requirements.With its commitment to innovation, quality, and customer satisfaction, [Company Name] is well-positioned to redefine the thermal management landscape. Their customized heatsink part represents a significant step forward in providing efficient and reliable cooling solutions across a range of industries, ensuring enhanced performance and longevity for critical electronic systems. By harnessing this groundbreaking technology, companies can stay ahead in the competitive market, delivering products that excel in performance and efficiency.For more information about [Company Name] and their revolutionary customized heatsink part, please visit [website] or contact [contact information].About [Company Name]:[Company Name] is a leading global provider of thermal management solutions. With a focus on research, development, and manufacturing, the company is committed to delivering innovative products that ensure optimal cooling and reliability for electronic systems. [Company Name]'s team of experts collaborates closely with clients to provide customized solutions tailored to their specific requirements.
How to Build a Heavy CNC Milling Machine: 18 Steps with Pictures
Machine, Instructables, heavy CNC milling, epoxy granite, linear guides, building processCNC Milling Machine: A Comprehensive Guide to Building Your OwnBuilding a heavy-duty CNC milling machine is not a task for the faint-hearted. It requires a lot of different working steps and careful planning to ensure that you end up with a machine that can deliver precise and accurate results. In this blog post, we will take a closer look at the steps involved in building a big CNC machine with good milling performance, as well as the materials and equipment needed for the project.Step 1: Design and PlanningThe first step in building a CNC milling machine is to design and plan the machine. This involves deciding on the size of the machine, the materials to be used, the type of milling machine to be used, and the features and capabilities that the machine should have. It is important to have a clear understanding of the requirements before starting the project to avoid any costly mistakes down the line.Step 2: Building the MoldThe next step is to build a big and accurate mold for casting the epoxy granite. Epoxy granite is a popular material for building milling machines due to its sturdiness and vibration damping properties. The mold should be designed to ensure that it is rigid and can create a smooth surface finish. The casting process should be done carefully to avoid any air bubbles or voids that can cause inaccuracies in the finished cast.Step 3: Aligning the Linear GuidesThe linear guides play a crucial role in the accuracy and precision of the milling machine. They are responsible for guiding the cutting tool along a straight and consistent path. The linear guides should be aligned carefully to ensure that they are in perfect alignment with the cutting tool. This requires careful attention to detail and the use of precision measuring tools.Step 4: Building the Machine FrameThe frame of the milling machine should be built to be strong and rigid. The use of high-quality materials such as aluminum or steel is recommended. The frame should be designed with sufficient clearance to accommodate the linear guides and other machine components.Step 5: Assembling the MachineOnce all the components of the milling machine have been prepared, it is time to start assembling the machine. This requires careful attention to detail and a lot of patience. Each component should be installed carefully and securely to ensure that the machine is stable and can deliver precise and accurate results.ConclusionBuilding a heavy CNC milling machine is a challenging task that requires a lot of time and effort. However, with careful planning and attention to detail, it is possible to build a machine that can deliver precise and accurate results. The use of high-quality materials and precision measuring tools is essential to ensure that the machine is built to the required specifications. With the right approach, anyone can build their own CNC milling machine and take their machining capabilities to the next level.
Top Precision CNC Machining Parts Suppliers in China for Quality Products
China’s CNC Precision Machining Parts Industry Thrives Amidst Growing DemandChina’s CNC precision machining parts industry has been growing steadily over the past few years due to the increasing demand for such products across various industries. With this rise, hundreds of companies have emerged as prominent manufacturers and suppliers of high-quality CNC precision machining parts. One such company leading the way is WEIMI, a professional manufacturer of CNC precision machining parts in China.WEIMI is a well-known company with a reputation for reliability, high-quality products, and excellent customer service. The company has been operating in the CNC machining parts industry for more than ten years and has extensive experience and technical expertise in designing and manufacturing a wide range of CNC precision machining parts.The company has a team of experts who are skilled and experienced in using the latest technology to create top-quality products at competitive prices. They have helped WEIMI establish itself as a leading supplier of CNC machining parts, serving industries ranging from automotive, industrial machinery, aerospace, electronics, communications, and many others.WEIMI’s CNC precision machining parts production facility is equipped with the latest machinery and technology to ensure that the highest quality products are produced. The company uses advanced software and machines such as CAD/CAM, CNC lathes, milling machines, and others to produce precision components that meet the most stringent quality standards.One of the advantages of working with WEIMI is that they provide customized CNC precision machining parts to meet specific customer requirements. The company has a team of experts who work with clients to understand their needs and create products that meet those needs. This service has helped companies across various industries to improve the efficiency and productivity of their operations.As the CNC machining parts industry in China continues to grow, WEIMI is well-positioned to remain a leader in the market. The company has a proven track record of designing and manufacturing quality products that meet the changing needs of its clients. Another factor that has helped the company to grow is China’s status as the world’s largest manufacturing hub. The country has established itself as a powerhouse in the global manufacturing industry. It boasts of a vast supply chain and highly skilled labor force, making it an ideal location for manufacturing companies.China’s government has also played a significant role in encouraging the growth of the CNC machining parts industry. The government has introduced several policies aimed at supporting the development of the manufacturing industry, including tax incentives, subsidies, and other support measures. These initiatives have helped to create a conducive environment for companies such as WEIMI to thrive.Overall, the CNC precision machining parts industry in China is expected to continue seeing growth in the coming years. As the world’s major economies continue to recover from the COVID-19 pandemic, the demand for precision parts and components across various industries is expected to increase. WEIMI is poised to play an essential role in meeting this demand, thanks to its commitment to quality, innovation, and custom production of CNC precision machining parts that meet the specific needs of its clients.In conclusion, the CNC precision machining parts industry in China is thriving thanks to the growing demand for such products across various industries. WEIMI and other companies are leading the way in designing and manufacturing high-quality CNC precision machining parts that meet the most stringent quality standards. With China’s government support and the country’s status as a global manufacturing hub, the prospects for the industry remain bright.
Fast and Reliable MP3 Downloads for the Best Wet Paint Songs Without Registration
Wet Paint Launches Exciting New Music DownloadsMusic lovers, rejoice! Wet Paint, a leading independent music platform, has just launched a new range of MP3 song downloads that are sure to get you grooving. The new collection features some of the biggest hits by the hottest artists of the moment, giving you access to the top tunes and latest tracks that are taking the music world by storm.Wet Paint has always been a reliable destination for music fans looking to stay on top of the latest trends in pop, rock, hip-hop, electronic, and indie music. The platform offers an extensive library of tracks from local and international artists, spanning a range of styles and genres. Whether you're a fan of classic rock bands, mainstream pop icons, or emerging indie acts, you're sure to find something to suit your musical tastes on Wet Paint.Now, with the launch of the new MP3 song downloads, music lovers will have even more options to explore. The downloads are fast, reliable, and secure, ensuring that you can quickly and conveniently get your hands on the latest tracks without any hassles.To celebrate the launch of the new MP3 downloads, Wet Paint is offering fans a special deal. For a limited time, users can get a discount on downloads by using a promo code provided by the platform. This is a great opportunity for music fans to access some of the hottest new tracks without breaking the bank.Wet Paint is committed to providing fans with a superior music experience, and the new MP3 downloads are just the latest offering in this regard. The platform is continually seeking to improve its service and expand its library, with a focus on offering the best content and features to users.In addition to its extensive collection of music tracks, Wet Paint also offers users a range of other features and resources. These include insightful music news, in-depth interviews with artists, and a lively social community where fans can connect with one another and share their love for music.Overall, the new MP3 downloads from Wet Paint are a welcome addition to the platform's impressive arsenal of music resources. With its focus on quality, variety, and user satisfaction, Wet Paint is quickly becoming one of the most trusted and popular destinations for music fans around the world. Whether you're a long-time fan of the platform or a new user, the new MP3 downloads are sure to offer hours of musical enjoyment and discovery. So what are you waiting for? Head to Wet Paint and start downloading the best tunes of the moment today!
Precision Sheet Metal Brackets Made with Advanced Manufacturing Techniques
: A Comprehensive Guide for Your Manufacturing NeedsSheet metal brackets are an integral part of any manufacturing process that requires the use of metal sheets. In industries that require immense precision and accuracy, the bracket systems ensure that the metal’s shape and structure are maintained throughout the process. With the advancements in modern CNC manufacturing processes, the quality of these bracket systems has improved significantly. The use of advanced automation tools has led to more efficient and precise manufacturing methods.Sheet metal brackets are widely used in various industries such as Aerospace, Medical, Automotive, Construction, and Electronics. In construction, sheet metal brackets are used to provide support to the structural systems, and in electronics, they secure electronic components in place. With their versatility, sheet metal brackets are an essential component in several processes and products.Here is a comprehensive guide to sheet metal brackets for all your manufacturing needs:Types of Sheet Metal Brackets1. Angle Brackets: These are brackets that are bent to 90-degree angles to create perpendicular structural joints. They are commonly used in construction to ensure that the structures maintain their shape and stability.2. U Brackets: These brackets have a U-shaped cross-section that is used to create a mounting point for objects. They are commonly used to mount objects onto walls and other surfaces.3. L Brackets: These are brackets that are bent to form an L-shape. They are used in most applications requiring reinforcement to prevent structural deformation.4. Z Brackets: These are brackets that are bent to form a ‘Z’ shape. They are used in construction to provide additional support to the structural systems.5. T Brackets: These are brackets that are bent to form a T-shape. They are commonly used to attach objects onto walls or other surfaces.Applications of Sheet Metal BracketsSheet metal brackets are used in various applications, including:AerospaceIn the aerospace industry, brackets are used to mount different types of equipment and systems such as electronics, fuel systems, engines, and landing gear. The brackets are usually made from lightweight materials like aluminum to minimize weight.AutomotiveIn the automotive industry, brackets are essential in holding the structural components of the car together. They are also used in securing electrical components in place.ConstructionSheet metal brackets are used extensively in the construction industry for many different applications, such as securing wall studs and reinforcing roof structures.ElectronicsIn the electronics industry, sheet metal brackets are used to secure electronic components in place. They are also used in creating housing systems for electrical components.MedicalSheet metal brackets are used in medical equipment and devices to support and hold various pieces of equipment such as monitors, IV poles, and other medical components in place.Manufacturing ProcessWith advancements in modern CNC manufacturing processes, sheet metal brackets can be precisely and efficiently manufactured. The manufacturing process for sheet metal brackets includes the following stages:1. Material Selection: The sheets of metal used in creating the brackets are usually made from various metals such as Stainless Steel, Carbon Steel, and Aluminum, and copper.2. Laser Cutting: The sheets of metal are cut using laser cutting machines to create the individual brackets' required shapes and sizes.3. Bending: The cut sheet metal is then bent using precision bending machines to create the desired shape of the bracket.4. Welding or Fixing: After bending the metal, the bracket components are welded or fixed together to create a final product.5. Finishing: The finished brackets are sandblasted or painted to give it a final finish.ConclusionSheet metal brackets are a vital part of many manufacturing processes. They provide structural support, aid in mounting equipment and components, and ensure precise manufacturing processes. The modern CNC manufacturing processes have significantly improved the manufacturing process of sheet metal brackets, leading to more efficient, accurate, and high-quality products. If you need sheet metal brackets for your manufacturing processes, ensure that you engage a reputable and experienced manufacturer who can deliver the desired results.
Production-Grade 3D Printer Enables MTConnect Integration for Aerospace and Industrial Applications
, F900 3D printer, production applications, aerospace industry, MTConnect protocol.Additive manufacturing has revolutionized the manufacturing industry with the ability to create complex geometries with high precision and speed. One of the leading players in the additive manufacturing market is the F900 3D printer, designed for production applications in the aerospace industry and other high-performance industries. This blog discusses the latest development in the F900 3D printer, which now features an MTConnect-ready interface, offering enhanced connectivity and data exchange capabilities.The F900 3D printer is known for its high-performance capabilities, reliability, and large-scale printing. The printer uses the Fused Deposition Modeling (FDM) technology, which involves building 3D models layer by layer by depositing material in a melted state. The FDM technology provides a high degree of design flexibility, allowing the production of complex geometries without the need for additional machining or assembly processes.The F900 3D printer has been widely used in the aerospace industry for the production of complex parts, such as ducting, brackets, and housings. These parts require high precision and accuracy, and the F900 has proven to be a reliable and cost-effective solution for their manufacturing. Additionally, the F900 has been used in other industries, such as automotive, defense, and medical, where the demand for high-performance parts is also high.The latest development in the F900 3D printer is its integration with the MTConnect protocol. MTConnect is an open-source communication protocol used in manufacturing equipment to facilitate data exchange and collection. The protocol offers a standardized way of communicating machine data, making it easier to integrate different systems and devices.With its MTConnect-ready interface, the F900 3D printer can now connect to other manufacturing systems, such as Enterprise Resource Planning (ERP) systems, Manufacturing Execution Systems (MES), and other machines in the production line. This enables better coordination between different manufacturing processes, leading to higher efficiency and productivity. Additionally, the MTConnect protocol allows for real-time monitoring of the printing process, giving operators better control and visibility over the manufacturing process.The integration of the MTConnect protocol into the F900 3D printer is a significant step towards enhancing the connectivity and data sharing capabilities of the printer. This development enables the printer to be integrated into a broader manufacturing ecosystem, allowing for seamless data exchange and coordination between different systems. This integration is highly relevant in the aerospace industry, where the demand for high-performance parts is only increasing.In conclusion, the F900 3D printer is a high-performance system designed for production applications in the aerospace industry and other high-performance industries. With its latest development, the integration of the MTConnect protocol, the printer now offers enhanced connectivity and data exchange capabilities, making it easier to integrate into a broader manufacturing ecosystem. This development ensures the F900 3D printer remains one of the leading additive manufacturing systems in the market today.
Discover the Excellence of Custom Metal Work for Your Projects
[Company Name] Introduces Innovative Custom Metal Work Solutions for Wide-Ranging Industries[City], [State] - [Date][Company Name], a renowned provider of advanced metal fabrication services, proudly announces the launch of its new line of custom metal work solutions. With a deep understanding of the unique requirements of various industries, [Company Name] aims to deliver tailor-made solutions to meet the evolving needs of its clients.For decades, [Company Name] has been at the forefront of the metal fabrication industry, garnering a reputation for excellence and precision. With its state-of-the-art facilities and a team of skilled craftsmen, the company has successfully completed numerous projects across a diverse range of sectors, including manufacturing, construction, automotive, and aerospace.The custom metal work solutions offered by [Company Name] encompass a wide array of products, each meticulously designed and crafted to meet the highest standards of quality. From small intricate components to large-scale structural elements, the company's expert team can handle projects of any complexity with utmost precision and efficiency.One of the key factors that set [Company Name] apart from its competitors is its commitment to employing cutting-edge technology throughout the fabrication process. By harnessing the power of advanced software and machinery, the company ensures consistent quality, accuracy, and fast turnaround times for its custom metal work solutions. This technology-driven approach enables [Company Name] to meet the ever-increasing demands of its clients while maintaining competitiveness in the market.The team at [Company Name] understands that no two projects are alike, and as such, they emphasize close collaboration with clients to develop tailor-made solutions that precisely match their unique requirements. From concept development to final delivery, the company's dedicated staff works closely with clients, ensuring effective communication, continuous updates, and seamless execution of the project."Our goal is to provide our clients with custom metal work solutions that not only meet but exceed their expectations," said [Spokesperson], [Company Name]'s spokesperson. "We take immense pride in our ability to embrace innovation and leverage technological advancements to deliver outstanding results. Our team of highly skilled craftsmen is committed to maintaining the highest standards of quality and precision, ensuring that our clients receive superior products that cater to their specific needs."With a proven track record of delivering exceptional custom metal work solutions, [Company Name] has garnered a loyal client base consisting of industry-leading players. The company's commitment to excellence, reliability, and customer satisfaction has made it the preferred choice for clients looking for customized metal fabrication services.As [Company Name] embarks on this new venture, it seeks to expand its reach into new markets and strengthen its position as a leader in the metal fabrication industry. With an unwavering focus on innovation, quality, and customer-centric solutions, the company is well-positioned to achieve continued growth and success."By introducing our new line of custom metal work solutions, we aim to solidify our reputation as a versatile and reliable partner for clients across various industries," added [Spokesperson]. "We look forward to showcasing our expertise and demonstrating how our custom metal work solutions can enhance the performance and aesthetics of our clients' projects."About [Company Name]:[Company Name] is a renowned provider of advanced metal fabrication services. With state-of-the-art facilities and a team of skilled craftsmen, the company delivers custom metal work solutions that cater to the unique requirements of various industries. Through its commitment to technology-driven innovation, quality, and customer satisfaction, [Company Name] has become a trusted partner for clients aiming to incorporate precision metal components and structures into their projects.For media inquiries, please contact:[Media Contact][Company Name][Phone][Email]
MTConnect-Ready 3D Printer for Aerospace and Production Applications
, MTConnect, FDM, aerospace, production, 3D printing.Additive Manufacturing Magazine recently reported that the Stratasys Fortus 900 3D printer now features an MTConnect-ready interface. This is great news for those working in aerospace and other industries that require high-quality, production-grade 3D printing.The Stratasys Fortus 900 is a Fused Deposition Modeling (FDM) 3D printer designed for large, complex parts. With a build volume of 36 x 24 x 36 inches, it has the capability to produce parts that are larger than those typically produced with plastic extrusion machines. This makes it an ideal choice for aerospace applications, as well as for producing jigs, fixtures, and tooling.Incorporating the MTConnect protocol into the Stratasys Fortus 900 means that users can now monitor and control their 3D printing operations in real time. MTConnect is an open, royalty-free standard for machine tool communication that has become increasingly popular in the manufacturing industry. With MTConnect, users can easily connect machines and devices to a network, allowing them to monitor data and make informed decisions about their operations.For aerospace manufacturers, the Stratasys Fortus 900 with MTConnect-ready interface is ideal, as it provides the capability to produce production-grade parts with repeatable accuracy. Additionally, 3D printing allows for the production of complex geometries that cannot be produced with traditional manufacturing methods.Overall, the integration of MTConnect into the Stratasys Fortus 900 3D printer is a positive development for the additive manufacturing industry. By providing real-time monitoring and control, it enables users to optimize their operations, increase efficiency, and improve the quality of their products. This is especially important in industries such as aerospace, where high-quality, production-grade parts are essential.As the use of 3D printing continues to grow, we can expect to see further developments in this area, and the integration of other technologies into 3D printers. In the meantime, the Stratasys Fortus 900 with MTConnect-ready interface is a great option for those looking to produce high-quality, production-grade parts with 3D printing technology.
Discover the Art of Stamping Sheet Metal Parts for Enhanced Manufacturing Processes
Stamping Sheet Metal Parts Released by Leading ManufacturerThe leading manufacturer of high-quality sheet metal parts announces the launch of its new stamping sheet metal parts, designed and engineered with the cutting-edge technology to meet the unique needs of clients in different industries. The company leverages its expertise in sheet metal stamping to produce top-notch parts that offer exceptional durability, strength, and functionality.The company specializes in producing sheet metal components like brackets, enclosures, frames, and other parts used in various industries such as automotive, construction, electronics, and aerospace. They integrate the latest technology and equipment in the production process to deliver parts that are precise, accurate, and consistent in quality.With years of industry experience, the company has become renowned for engineering innovative solutions that solve complex problems. By using the best-in-class techniques for sheet metal stamping, this manufacturer emphasizes the importance of designing, prototyping, and testing the parts for a perfect fit before mass production.Their stamping sheet metal parts undergo rigorous quality control checks, ensuring that only high-quality parts are manufactured. The manufacturer keeps the environment in mind while creating these products and ensures they are environmentally friendly, safe, and legal.Their extensive list of services ranges from designing and creating custom sheet metal parts to engineering and prototyping for a perfect fit. The manufacturer also provides assembly and finishing services requiring precision and consistency in the final part output, including welding, grinding, deburring, painting, and plating.Some of their clients include major companies such as General Electric, BMW, Eaton, Caterpillar, and many others. They offer a competitive pricing model and guarantee customer satisfaction with their top-notch parts designed to withstand stresses and tests.Sheet metal parts manufactured by this leading manufacturer undergo precise engineering and are always delivered on-time. The company leverages its stamping sheet metal technology to manufacture parts that meet international industrial standards.In addition, the company strives for excellence and encourages R&D to develop better products that meet the ever-changing technological advancements in the industry. The company's stamping sheet metal parts feature intricate designs, precision cuts, and close tolerances, making them suitable for a wide range of industrial applications.“We are thrilled to announce the launch of our new stamping sheet metal parts. Our engineering and manufacturing teams have been working hard to perfect these parts, ensuring that they meet the high standards we set as a company,” said the company representative. “Our mission has always been to provide our clients with high-quality parts that match their specific requirements, and our stamping sheet metal parts are no exception. We look forward to continuing to innovate and deliver exceptional service to our clients.”In conclusion, the leading manufacturer of high-quality sheet metal parts is proud to announce the release of its new stamping sheet metal parts designed for clients across a range of industries. They leverage the latest technology and equipment in the production process to deliver parts with exceptional durability, strength, and functionality. With years of industry experience and expertise, the company has become renowned for engineering innovative solutions that solve complex problems. Their stamping sheet metal parts undergo rigorous quality control checks, ensuring that only high-quality parts are manufactured. The company emphasizes the importance of designing, prototyping, and testing parts for a perfect fit before mass production. Satisfied clients range from renowned companies to smaller businesses in different industries.
Advanced Machining Techniques for Precision Milling Operations
Machining Milling, a prominent player in the machining industry, is revolutionizing the landscape of precision manufacturing. With their unwavering commitment to quality and innovation, the company has firmly established itself as a frontrunner in the market. Through their cutting-edge technologies and customer-centric approach, Machining Milling has become a go-to partner for businesses aiming to achieve superior quality and precision.Founded with a vision to redefine the machining industry, Machining Milling brings years of expertise and experience. Their team of highly skilled professionals is dedicated to producing exceptional results, adhering to strict quality control measures at every phase of the manufacturing process. By employing state-of-the-art machinery and sophisticated software, they ensure that each product meets the highest industry standards.One of the cornerstones of Machining Milling's success is their commitment to continuous improvement. The company constantly invests in research and development to stay ahead of technological advancements and meet the evolving needs of their customers. This allows them to provide tailor-made solutions, ensuring that every project is executed with precision and efficiency.Machining Milling's diverse range of services caters to a wide array of industries including aerospace, automotive, medical, and energy sectors. From concept to completion, their comprehensive manufacturing solutions encompass precision machining, milling, turning, and assembly. By utilizing cutting-edge techniques like computer numerical control (CNC) machining, they are able to deliver complex and intricate components with unparalleled accuracy.The company's dedication to customer satisfaction is evident in their personalized approach. Machining Milling works closely with each client, understanding their unique requirements, and providing customized solutions to meet their specific needs. Their team of experts collaborates with clients throughout the entire process, ensuring effective communication and a seamless manufacturing experience.One of the notable factors that distinguish Machining Milling from its competitors is their strong emphasis on quality assurance. The company adheres to stringent quality control protocols, ensuring that each product undergoes meticulous inspection and testing. This commitment to quality has earned Machining Milling numerous certifications, reflecting their unwavering dedication to excellence.Furthermore, Machining Milling recognizes the importance of sustainability in today's manufacturing landscape. The company is committed to minimizing its environmental impact by adopting environmentally friendly practices. They prioritize the use of eco-friendly materials and implement energy-efficient measures throughout their operations.Machining Milling's exceptional track record and commitment to excellence have earned them a loyal customer base. With a reputation for delivering on time and exceeding expectations, they have forged long-term partnerships with industry giants. Their commitment to continuous improvement and customer satisfaction sets them apart in the highly competitive machining industry.Looking to the future, Machining Milling aims to further expand their capabilities and technological prowess. By embracing the latest advancements, they continue to enhance their efficiency and precision, providing innovative solutions to meet the evolving demands of the market.In conclusion, Machining Milling has emerged as a leading name in the machining industry. With their commitment to quality, innovation, and customer satisfaction, they have redefined precision manufacturing. Through cutting-edge technologies, personalized approaches, and unwavering dedication to excellence, Machining Milling continues to set the benchmark for superior machining services.