Understanding the Benefits of Rapid Tooling for Manufacturing
By:Admin
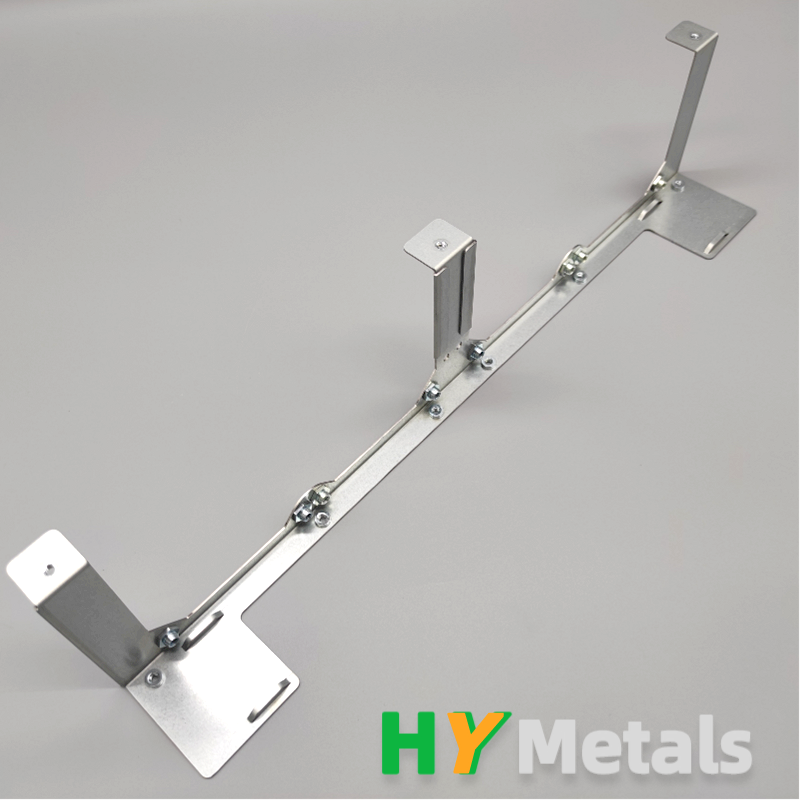
In the fast-paced world of manufacturing, having the ability to quickly produce high-quality tooling is a game-changer. This is where Rapid Tooling (RT) technology comes into play, offering a revolutionary approach to creating tooling for a wide range of manufacturing processes. With the breakthrough technology offered by the industry-leading company {}, manufacturers now have access to advanced RT solutions that significantly shorten production lead times and reduce costs, ultimately improving overall efficiency and competitiveness in the global market.
Company Introduction: {}
Established in the early 2000s, {} has been at the forefront of innovation in the manufacturing industry, offering a comprehensive range of cutting-edge solutions for tooling, prototyping, and production. With a strong focus on research and development, the company has continuously pushed the boundaries of technology to provide its customers with the most advanced and reliable tools and services. With a team of highly skilled engineers and technicians, {} has built a solid reputation for delivering superior quality products and unparalleled customer support.
Advanced Rapid Tooling Solutions
The traditional process of producing tooling for manufacturing purposes involves time-consuming and costly methods such as CNC machining and injection molding. These methods often require extensive lead times and significant financial investments, making it challenging for manufacturers to keep up with the demands of today's rapidly changing market.
However, with the introduction of RT technology, manufacturers now have access to a more efficient and cost-effective alternative. Rapid Tooling utilizes state-of-the-art 3D printing and additive manufacturing techniques to quickly produce high-precision tooling components, allowing for the rapid iteration of designs and the production of complex geometries that were previously unachievable.
By leveraging the advanced capabilities of RT technology, companies can significantly reduce lead times, accelerate product development cycles, and bring new products to market faster. This gives manufacturers a competitive edge by allowing them to respond more quickly to customer demands and adapt to changing market conditions.
The Benefits of Rapid Tooling
The adoption of RT technology offers a wide range of benefits for manufacturers across various industries. These include:
- Reduced lead times: RT technology allows for the quick production of tooling components, significantly reducing lead times compared to traditional manufacturing methods. This enables manufacturers to speed up their product development cycles and bring new products to market faster.
- Cost savings: By utilizing RT technology, manufacturers can save on tooling costs and minimize the need for expensive production equipment. This results in significant cost savings and a more efficient allocation of resources.
- Increased design flexibility: RT technology allows for the rapid iteration of designs and the production of complex geometries, giving manufacturers greater design flexibility and the ability to create innovative products with unique features.
- Improved quality: The advanced capabilities of RT technology ensure the production of high-precision tooling components with excellent surface finish and mechanical properties, contributing to improved overall product quality.
- Environmental sustainability: RT technology promotes sustainable manufacturing practices by minimizing material waste and energy consumption, contributing to a more environmentally friendly production process.
Looking to the Future
With the continuous advancement of RT technology, the future of manufacturing is set to undergo a significant transformation. The adoption of RT solutions will become increasingly prevalent in various industries, leading to a new era of efficiency, agility, and innovation. As pioneers in the field of Rapid Tooling, {} is committed to remaining at the forefront of this technological revolution, continually developing new and innovative solutions to meet the evolving needs of manufacturers worldwide.
By harnessing the power of RT technology, manufacturers can expect to see substantial improvements in their production processes, cost efficiencies, and overall competitiveness. With the support and expertise of pioneering companies like {}, the future of manufacturing looks brighter than ever, paving the way for a new era of growth and prosperity in the industry.
Company News & Blog
Expert Sheet Metal Box Fabrication Services for Your Business
Sheet metal box fabrication is a crucial process in the manufacturing industry, and it requires precision and skill to create durable and functional boxes for various applications. Sheet metal box fabrication involves cutting, bending, and assembling sheet metal to create a box that meets the specific requirements of the customer. The process is often used in industries such as automotive, aerospace, electronics, and healthcare, where custom-made boxes are needed to house delicate equipment or components.This is where {Company Name} comes in. With years of experience in sheet metal fabrication, {Company Name} has established itself as a leader in the industry, offering high-quality and cost-effective solutions for its customers. The company prides itself on its ability to take on complex fabrication projects and deliver superior results.{Company Name} utilizes advanced machinery and equipment to ensure precision and accuracy in the sheet metal box fabrication process. The company's team of skilled engineers and technicians work closely with customers to understand their specific requirements and design custom solutions that meet their needs. Whether it's a simple junction box or a complex enclosure, {Company Name} has the expertise to deliver.In addition to its technical capabilities, {Company Name} is committed to maintaining the highest standards of quality and efficiency in its operations. The company adheres to stringent quality control measures to ensure that every sheet metal box meets the necessary specifications and standards. With a focus on continuous improvement, {Company Name} constantly seeks ways to enhance its processes and deliver even better results to its customers.{Company Name}'s dedication to customer satisfaction has earned it a reputation for reliability and excellence in the sheet metal fabrication industry. The company has worked with a diverse range of clients, providing custom solutions for their unique requirements. By collaborating with {Company Name}, customers can expect a seamless and efficient process, from initial design to final production.One of the key factors that sets {Company Name} apart from its competitors is its ability to offer cost-effective solutions without compromising on quality. The company understands the importance of delivering value to its customers, and it strives to optimize its processes to ensure competitive pricing for its services. This commitment to affordability has made {Company Name} a preferred partner for many businesses seeking sheet metal box fabrication services.As the demand for custom sheet metal boxes continues to grow across various industries, {Company Name} remains at the forefront of innovation and excellence. The company is constantly investing in technology and skills development to stay ahead of the curve and meet the evolving needs of its customers. Whether it's adopting new fabrication techniques or embracing emerging trends, {Company Name} is dedicated to staying relevant in a rapidly changing industry.In conclusion, sheet metal box fabrication is a critical process that requires expertise and precision to deliver superior results. With its technical capabilities, commitment to quality, and customer-focused approach, {Company Name} has established itself as a leading provider of sheet metal fabrication solutions. For businesses looking for reliable and cost-effective services, {Company Name} is the partner of choice for all their sheet metal box fabrication needs.
High-Quality Precision Milling Parts for Various Industries
Milling Parts is a leading multinational corporation that specializes in producing and supplying high-quality mechanical parts for various industries such as automotive, aerospace, medical, and more. The company has a mission to meet the needs of its customers by providing the best products and services possible. Milling Parts has recently announced a significant expansion of its operations, which will enable the company to enhance its production capacity and supply chain efficiency. This expansion includes the construction of a new state-of-the-art plant that will be equipped with advanced technologies to enable the production of more complex and high-quality parts. According to the company officials, this new plant will be the largest Milling Parts production facility, and it will be strategically located to serve both domestic and international customers. The facility will include multiple production lines, quality control and testing facilities, warehouses, and administrative offices. The CEO of Milling Parts stated that this expansion is part of the company's long-term growth strategy, and it reflects the commitment to meeting the increasing demands of its customers. He further added that the company aims to increase its market share and become a key player in the global mechanical parts industry. Milling Parts is known for its innovative and customer-focused approach to business. The company has an experienced team of engineers and technicians who work closely with customers to understand their needs and provide customized solutions. The company also invests heavily in research and development to stay at the forefront of technological advancements in the industry. Milling Parts is committed to ensuring the highest quality standards in all its products and services. The company has implemented a comprehensive quality management system that includes strict adherence to international standards such as ISO 9001 and AS9100. This ensures that all products and services meet or exceed customer expectations and comply with regulatory requirements. Milling Parts has a strong presence in the global market and serves customers in more than 50 countries. The company has established a network of partners and distributors worldwide, which enables it to provide efficient logistics and supply chain services. Milling Parts is also committed to sustainability and operates with a focus on minimizing its environmental impact. The company has implemented various initiatives to reduce energy consumption, waste generation, and carbon emissions. Milling Parts has a positive reputation in the industry, and it has received numerous awards and certifications for its excellence in quality, innovation, and customer service. The company has also been recognized for its role in creating job opportunities and contributing to economic growth in the regions where it operates. The expansion of Milling Parts operations is expected to create additional job opportunities and contribute to the development of the local economy. The company has stated that it will prioritize the recruitment of local talent and provide training and career development opportunities. In conclusion, Milling Parts is a leading mechanical parts manufacturer with a commitment to innovation, quality, and customer service. The company's expansion of operations is a reflection of its long-term growth strategy and commitment to meeting the needs of its customers. The new state-of-the-art plant will enable Milling Parts to enhance production capacity, supply chain efficiency, and become a key player in the global mechanical parts industry.
Durable and Versatile Aluminum Bending Bracket for Various Applications
Aluminum Bending Bracket Supplier Reaches New MilestoneIn the world of manufacturing, precision is key. Every detail matters, and every part must be crafted with care and expertise. This is especially true in the aerospace and automotive industries, where the demand for high-quality components is at an all-time high.One company that has been meeting and exceeding these demands is [Company Name]. With a proven track record of providing top-notch aluminum bending brackets to some of the biggest names in the industry, [Company Name] has recently reached a new milestone in their journey towards manufacturing excellence.Specializing in the production of aluminum bending brackets, [Company Name] has been a major player in the manufacturing industry for many years. Their parts are known for their precision, durability, and reliability, making them the go-to choice for companies in need of high-quality components.The team at [Company Name] is made up of dedicated professionals who are passionate about their work. With a commitment to delivering the best possible products to their customers, they have built a reputation for excellence and reliability. This has allowed them to forge strong partnerships with some of the most respected companies in the industry, cementing their status as a leading supplier of aluminum bending brackets.Their manufacturing process is second to none, with a focus on quality and precision at every step. From the initial design phase to the final inspection, every part is meticulously crafted to ensure that it meets the highest standards. This dedication to quality has set [Company Name] apart from the competition, making them a trusted name in the industry.Recently, [Company Name] announced that they have reached a new milestone in their production capabilities. Thanks to their continued investment in cutting-edge technology and their unwavering commitment to excellence, they have expanded their manufacturing capacity, allowing them to produce even more high-quality aluminum bending brackets than ever before.This milestone is a testament to [Company Name]'s dedication to innovation and progress. By investing in state-of-the-art equipment and staying ahead of the curve when it comes to manufacturing techniques, they have positioned themselves as a leader in the industry. This expanded capacity will allow them to better serve their customers and meet the growing demand for their products.In addition to their commitment to quality and innovation, [Company Name] also prioritizes sustainability in their manufacturing processes. They understand the importance of minimizing their environmental impact and have taken steps to ensure that their operations are as eco-friendly as possible. This dedication to sustainability has not gone unnoticed, and has further solidified [Company Name]'s reputation as a responsible and forward-thinking supplier.As the demand for high-quality aluminum bending brackets continues to grow, [Company Name] is well-positioned to meet and exceed the needs of their customers. With their expanded production capacity and unwavering commitment to excellence, they are ready to take on new challenges and continue to provide top-notch components to the aerospace and automotive industries.In conclusion, [Company Name] has reached a new milestone in their journey towards manufacturing excellence. With a focus on quality, innovation, and sustainability, they have solidified their position as a leading supplier of aluminum bending brackets. Their dedication to precision and their commitment to meeting the needs of their customers make them a trusted partner for companies in need of high-quality components. As they continue to invest in their capabilities and expand their production capacity, [Company Name] is poised to remain at the forefront of the industry for years to come.
High-Quality Steel Machined Parts for Various Applications
Steel Machined Parts is a leading manufacturer of precision machined components for a wide range of industries. With a reputation for delivering high quality products and exceptional customer service, the company has established itself as a trusted partner for businesses in need of reliable and efficient manufacturing solutions.Founded in 1998, Steel Machined Parts has grown from a small workshop into a state-of-the-art manufacturing facility, equipped with the latest CNC machining technology and a team of highly skilled engineers and machinists. Over the years, the company has continued to invest in new equipment and training to ensure that they can meet the evolving needs of their customers and maintain their position as a leader in the industry.Steel Machined Parts serves a diverse customer base, including companies in the automotive, aerospace, defense, and medical industries. Their ability to produce complex components with tight tolerances has made them a trusted supplier for manufacturers producing critical parts for various applications. Whether it's precision gears for aircraft engines or specialized medical implants, Steel Machined Parts has the expertise and capabilities to deliver the highest quality machined parts.One of the key factors that sets Steel Machined Parts apart from their competitors is their commitment to continuous improvement and innovation. The company has a strong focus on research and development, constantly exploring new techniques and materials to enhance their manufacturing processes. This dedication to innovation has allowed Steel Machined Parts to stay ahead of the curve and provide their customers with cutting-edge solutions to their machining needs.In addition to their technical expertise, Steel Machined Parts is also known for their dedication to customer satisfaction. The company works closely with each client to understand their specific requirements and provide tailored solutions to meet their needs. From prototype development to full-scale production, Steel Machined Parts offers a comprehensive suite of services to support their customers at every stage of the manufacturing process.Most recently, Steel Machined Parts has announced the launch of a new line of steel machined parts that will further expand their product offerings. This expansion is expected to provide customers with even more options for their machining needs, further solidifying Steel Machined Parts' position as a leading provider of precision machined components."We are excited to introduce our new line of steel machined parts to the market," said [Company Spokesperson]. "With our state-of-the-art manufacturing capabilities and commitment to excellence, we are confident that these new products will meet the needs of a wide range of industries and continue to uphold our reputation for quality and reliability."The new steel machined parts are designed to offer the same level of precision and performance that customers have come to expect from Steel Machined Parts. Whether it's hardened steel shafts, precision milled components, or custom steel fittings, the company's expanded product line will provide businesses with a wider range of options for their machining needs.As Steel Machined Parts continues to grow and evolve, they remain dedicated to upholding the highest standards of quality and service for their customers. With their focus on innovation, dedication to customer satisfaction, and the launch of new products, the company is poised to remain a leader in the precision machining industry for years to come.
How steel bending is revolutionizing the manufacturing industry
Steel Bending Innovation: A New Milestone for {}{} is proud to announce a groundbreaking innovation in the steel industry with the introduction of a revolutionary steel bending technology. This new development promises to revolutionize the way steel is handled and shaped, setting a new standard for efficiency and precision in the manufacturing process.The new steel bending technology, developed by a team of experts at {}, represents a major advancement in the industry. With this innovation, {}, a leading name in the steel manufacturing sector, is well-positioned to further solidify its position as a leader in the industry.This cutting-edge technology allows for the bending of steel with unprecedented accuracy and efficiency, ensuring that each piece of steel is precisely shaped according to specifications. This level of precision is crucial in industries such as construction and manufacturing, where the structural integrity of steel components is paramount.The new steel bending technology also offers significant advantages in terms of speed and cost-efficiency. By streamlining the bending process, {} can significantly reduce production times, leading to faster turnaround times for customer orders. This increased efficiency also translates to cost savings, allowing {} to offer competitive pricing without compromising on quality.The introduction of this innovation underscores {}'s commitment to pushing the boundaries of what is possible in the steel industry. With a track record of delivering high-quality steel products to a wide range of industries, {} continues to invest in cutting-edge technologies that set new benchmarks for excellence.In addition to the technological advancements, {}'s steel bending process is also environmentally friendly. By reducing waste and optimizing production processes, {} is minimizing its environmental footprint and contributing to sustainability efforts in the industry."We are thrilled to introduce this game-changing steel bending technology to the market," said {}'s CEO. "This innovation is a testament to our commitment to driving progress and delivering the best possible products to our customers. With this new technology, we are confident that we can meet the evolving needs of the industry and continue to raise the bar for excellence in steel manufacturing."The introduction of this innovative steel bending technology comes at a time of rapid growth for {}. The company has been gaining momentum in the market, expanding its client base and strengthening its reputation as a trusted provider of high-quality steel products.Looking ahead, {} plans to continue investing in research and development to further enhance its technological capabilities and maintain its competitive edge in the industry. By staying at the forefront of innovation, {} is well-positioned to lead the way in shaping the future of steel manufacturing.With the introduction of this groundbreaking steel bending technology, {} is setting a new standard for precision, efficiency, and sustainability in the industry. As the company continues to push the boundaries of what is possible, it is poised to make a lasting impact on the steel manufacturing sector, delivering unparalleled value to its customers and driving progress across the industry.
Sheet Metal Bending Tools: Dies, Press Brakes, Tube & Wire Bending
Sheet metal bending is a process that involves creating a bend in a metal sheet to give it a certain shape or form. This process is done using specialized tools and equipment such as bending dies, press brakes, and tube & wire bending machines.Bending dies are the main tool used for sheet metal bending. They are used to apply force to the metal to create a bend. These dies come in different shapes and sizes depending on the shape and size of the bend required. The dies can be used with a stamping press or press brakes.Stamping presses are machines that are used to apply pressure to the metal sheet to create the desired shape. The press brake is another machine that is used for sheet metal bending. It is a large machine that uses a hydraulic system to apply force to the metal sheet. The press brake can create several bends in the metal sheet at once.There are several types of bending dies that can be used for sheet metal bending. The most common type of bending die is the progressive bending die. This die allows multiple bends to be created simultaneously, which makes the process faster and more efficient. Other types of bending dies include the wiping die, rotary die, and the air-bending die.Wire bending machines are used to create bends in wire or rod-shaped materials. These machines use specialized dies to create precise bends in the wire. The bending process is done using a combination of force and heat to create the desired shape.Tube bending machines are used for creating bends in tubes and pipes. These machines use mandrels and dies to create precise bends in the tube. The mandrel is a rod that is placed inside the tube to prevent it from collapsing during the bending process.When it comes to sheet metal bending, it is important to use the right tools and equipment to ensure that the sheet metal is bent correctly. Bending dies and tools are crucial in this process. With the right tools and equipment, it is possible to create precise bends that will meet the desired requirements.In conclusion, sheet metal bending is a complex process that requires specialized tools and equipment like bending dies, press brakes, tube & wire bending machines. Each of these pieces of equipment plays a crucial role in the bending process and is designed to create precise bends. When used correctly, these tools can help you achieve the desired shape and form for your sheet metal project.
Precision CNC Machining for Small Parts: What You Need to Know
In today's fast-paced manufacturing industry, precision and efficiency are crucial elements for success. This is where CNC machining comes into play, providing the capability to produce small parts with a high degree of accuracy and repeatability. One company that has been at the forefront of this technology is {Company Name}, a leading provider of precision machining services.{Company Name} is a world-class precision machining company that has been in the business for over 20 years. With state-of-the-art facilities and a team of highly skilled machinists, they have built a reputation for delivering high-quality products to a wide range of industries, including aerospace, automotive, medical, and more.One of the key services offered by {Company Name} is CNC machining of small parts. This process involves using computer-controlled machines to remove material from a workpiece, resulting in the production of intricate and precise components. With their advanced CNC equipment and expertise, {Company Name} has the capability to machine a wide variety of small parts, from prototypes to high-volume production runs.The company's CNC machining capabilities are particularly well-suited for producing small parts that require tight tolerances and complex geometries. This includes components such as gears, bushings, connectors, and many others. Their ability to work with a wide range of materials, including metals, plastics, and composites, further expands the possibilities for small part machining.In addition to their technical capabilities, {Company Name} also focuses on providing exceptional customer service. They work closely with their clients to understand their specific needs and requirements, ensuring that the machined parts meet the highest standards of quality and accuracy. This collaborative approach has allowed them to build long-standing relationships with their customers, who rely on {Company Name} for their precision machining needs.With the increasing demand for small, intricate parts across various industries, {Company Name} continues to invest in the latest CNC machining technologies to stay ahead of the curve. Their commitment to innovation and continuous improvement has made them a trusted partner for companies seeking high-quality small parts for their products.In a recent development, {Company Name} has made significant investments in their CNC machining capabilities, including the acquisition of new equipment and the implementation of advanced software solutions. This has further enhanced their ability to produce small parts with unmatched precision and efficiency, reinforcing their position as a leader in the precision machining industry.One of the key advantages of working with {Company Name} for CNC machining of small parts is their ability to handle complex projects with quick turnaround times. Their advanced equipment and experienced machinists allow them to optimize production processes, minimizing lead times and ensuring timely delivery of machined parts to their customers.Overall, {Company Name} has solidified its position as a top-tier provider of CNC machining services for small parts, catering to the diverse needs of industries that demand precision and reliability. With their unwavering commitment to quality and customer satisfaction, they continue to be the go-to choice for businesses looking for a trusted partner in precision machining.As the manufacturing industry continues to evolve, the demand for high-quality small parts will only increase. With {Company Name}'s dedication to excellence and continuous investment in CNC machining technologies, they are well-positioned to meet the evolving needs of their customers and maintain their leadership in the precision machining sector.
A Guide to Heat Sink Extrusion: What You Need to Know
Heat Sink Extrusion - The Ultimate Solution for Thermal ManagementIn today's fast-paced world of technology, electronic devices are becoming more powerful and compact, which inevitably leads to an increase in heat generation. This rise in temperature can have detrimental effects on the performance and longevity of electronic components. To combat this issue, the use of heat sinks has become indispensable in the field of thermal management. Among various types of heat sinks available in the market, heat sink extrusions have proven to be a superior solution for effective heat dissipation.{Company name}, a leading manufacturer of heat sink extrusions, has been at the forefront of developing innovative thermal management solutions for a wide range of applications. With a strong focus on research and development, the company has continuously pushed the boundaries of heat sink technology to meet the evolving needs of the electronics industry.Heat sink extrusions are aluminum-based heat sinks that are created through an extrusion process, which involves pushing a solid aluminum billet through a die to produce the desired shape. This method allows for the creation of complex and efficient heat sink designs that are both lightweight and cost-effective. The extrusion process also enables the incorporation of various features such as fins, channels, and mounting holes, providing flexibility in design and performance.One of the key advantages of heat sink extrusions is their superior thermal conductivity. Aluminum, the most commonly used material for heat sink extrusions, offers excellent thermal conductivity, allowing for efficient heat transfer from the electronic components to the surrounding environment. This property is crucial in preventing the overheating of electronic devices and ensuring their reliable operation.In addition to thermal conductivity, the lightweight nature of aluminum makes heat sink extrusions an ideal choice for applications where weight reduction is a consideration. The ease of machining and surface treatment further enhances the versatility of aluminum heat sink extrusions, allowing for customized solutions to meet specific thermal management requirements.{Company name} has been instrumental in optimizing the design and manufacturing processes of heat sink extrusions to deliver top-quality solutions to its customers. By leveraging advanced simulation and analysis tools, the company can accurately predict the thermal performance of its heat sink designs, ensuring that they meet the stringent requirements of modern electronics.Furthermore, {Company name} has established stringent quality control measures to guarantee the consistency and reliability of its heat sink extrusions. The company's state-of-the-art manufacturing facilities are equipped with the latest machinery and technology, allowing for precise and efficient production of heat sink extrusions that adhere to the highest industry standards.The applications of heat sink extrusions are diverse, ranging from consumer electronics and telecommunications to automotive and industrial equipment. Their ability to effectively dissipate heat makes them essential components in electronic devices such as power supplies, LED lighting, computer systems, and motor drives, among others. With the increasing demand for high-performance electronics, the need for efficient thermal management solutions has never been greater, making heat sink extrusions an indispensable technology.As the electronics industry continues to advance, the role of heat sink extrusions in thermal management will become even more critical. {Company name} is committed to staying at the forefront of heat sink technology, continuously innovating and refining its products to meet the evolving demands of the market.In conclusion, heat sink extrusions have emerged as a game-changing solution for thermal management, with their superior thermal conductivity, lightweight nature, and design flexibility. {Company name} has been a driving force in the development and manufacturing of high-quality heat sink extrusions, catering to a wide range of industries. With a focus on innovation and excellence, {Company name} is well-positioned to address the evolving thermal management needs of the electronics industry.
Versatile 3-Axis Milling Machine for Diverse Applications
Milling is a versatile machining process that involves removing material from a workpiece using rotary cutters. It is a critical process in manufacturing, and it has wide-ranging applications. Whether creating new parts or repairing existing ones, milling precision parts is essential. To achieve precision, you need a reliable milling machine. One such machine is the 3-axis MILL E Series by GF Machining Solutions.The MILL E Series is a universal milling machine that sets standards in the industry. It has a high-precision spindle and advanced controller technology that provides accuracy and efficiency. The machine's design also allows for versatility, as it can handle various workpiece sizes and shapes. Additionally, the machine's user-friendly interface makes it easy to operate, reducing operator error and ensuring consistent precision.One of the most significant advantages of the MILL E Series is its ability to handle a range of materials. Whether you are machining aluminum, steel, or plastics, this milling machine can get the job done. It also has a flexible automatic tool changer, which can accommodate various tool types, and the machine's software can optimize cutting parameters for the specific material being machined. This ensures precision and quality in every job.In the VMC category, the MILL E Series sets the standard for milling precision parts. With its 3-axis design, it can produce complex, high-precision parts that meet tight tolerances. Moreover, the machine's high spindle speed and rigidity make it possible to maintain high precision even under heavy cutting loads. This capability makes the milling machine an excellent choice for challenging milling applications.In die and mold construction, the MILL E Series is also a valuable tool for smoothing surface finishes. When using a round-head cutter, the milling machine can deliver precise and polished surfaces, making it ideal for finishing workpieces. This capability makes the milling machine an essential tool for injection mold manufacturing, which requires smooth and polished finishes for the final product.ConclusionMilling precision parts is essential in the manufacturing industry, and having a reliable milling machine is critical in achieving precision and efficiency. GF Machining Solutions' MILL E Series offers versatile applications, high-performance, and precision in milling. Its 3-axis design, high spindle speed, and tool-changing capabilities make it ideal for milling precision parts of varying shapes, sizes, and materials. It also allows for excellent surface finishes, making it an invaluable tool in die and mold construction. So, if you are in the market for a milling machine that can deliver precision, efficiency, and versatility, consider the MILL E Series from GF Machining Solutions.
High-Quality CNC Machined Parts for Precision Engineering
CNC Machined Parts are at the heart of the manufacturing industry, and they play a crucial role in the production of a wide range of products. From automotive components to aerospace parts, CNC machined parts are essential in creating precision-engineered products. One company that is at the forefront of providing top-quality CNC machined parts is {}. With a strong focus on precision and quality, {} has become a trusted partner for many leading companies in various industries.{} specializes in the production of CNC machined parts using the latest technology and advanced machining techniques. The company's state-of-the-art facilities are equipped with high-precision CNC machines that can produce complex and intricate parts with exceptional accuracy. Whether it's a simple prototype or a high-volume production run, {} has the capabilities to meet the most demanding requirements.The company prides itself on its ability to deliver precision-engineered parts with quick turnaround times. By utilizing advanced CAD/CAM software and highly skilled machinists, {} can efficiently program and manufacture CNC machined parts to meet tight deadlines. This rapid production capability has made {} a preferred supplier for companies that require fast and reliable machining services.In addition to its cutting-edge manufacturing capabilities, {} places a strong emphasis on quality control. The company follows strict quality assurance protocols to ensure that each part meets the highest standards of accuracy and consistency. By employing advanced inspection equipment and rigorous quality checks, {} ensures that its CNC machined parts are of the highest quality before they are delivered to customers.As a customer-centric company, {} is committed to providing exceptional customer service and support. The company works closely with its clients to understand their specific needs and requirements, and it offers customized solutions to meet their unique challenges. Whether it's providing design assistance, optimizing manufacturing processes, or offering technical advice, {} goes above and beyond to ensure that its customers receive the best possible service.In addition to its focus on precision and quality, {} is also dedicated to sustainability and environmental responsibility. The company has implemented eco-friendly practices in its manufacturing processes to reduce its environmental impact. By using efficient machining techniques and minimizing waste, {} strives to operate in an environmentally conscious manner.With its unwavering commitment to excellence, {} has established itself as a leading provider of CNC machined parts. The company's dedication to precision, quality, and customer satisfaction has earned it a stellar reputation in the manufacturing industry. Whether it's producing intricate components for the aerospace industry or creating custom parts for the automotive sector, {} continues to set the standard for excellence in CNC machining.In conclusion, CNC machined parts are an integral part of modern manufacturing, and {} is a standout leader in the industry. With its advanced capabilities, stringent quality control, and unwavering commitment to customer satisfaction, {} has become the go-to partner for companies seeking top-quality CNC machined parts. As the manufacturing sector continues to evolve, {} remains at the forefront, delivering precision-engineered parts that meet the highest standards of excellence.