Advancements in Additive Manufacturing: A Look into the Future of 3D Printing
By:Admin
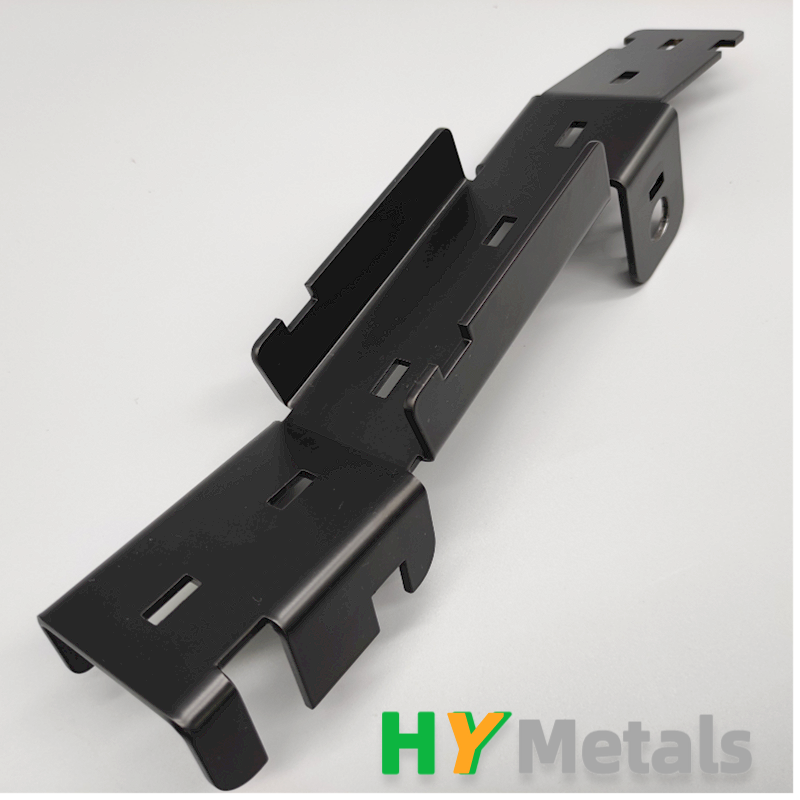
Additive manufacturing, also known as 3D printing, has been making waves in various industries as a revolutionary technology that is transforming the production process. This innovative method allows for the creation of complex and intricate designs by adding material layer by layer, as opposed to traditional subtractive manufacturing techniques. As a result, additive manufacturing has become increasingly popular in industries such as aerospace, automotive, healthcare, and consumer goods.
One company at the forefront of this additive manufacturing revolution is {}. Founded in 2010, {} has quickly become a leading provider of additive manufacturing solutions, offering a wide range of 3D printing technologies and materials to meet the diverse needs of its customers. With a mission to enable the world to innovate and create faster, more affordable, and sustainable solutions, {} has been instrumental in pushing the boundaries of what is possible with additive manufacturing.
One of the key advantages of additive manufacturing is its ability to produce intricate and complex designs that would be difficult, if not impossible, to create using traditional manufacturing methods. This has led to significant advancements in product design and development, allowing for faster prototyping and iteration of designs. Additionally, additive manufacturing has the potential to reduce material waste and energy consumption, making it a more sustainable option for production.
In the aerospace industry, additive manufacturing has revolutionized the way aircraft components are produced. With the ability to create lightweight and highly durable parts, aircraft manufacturers are able to improve fuel efficiency and reduce overall costs. This has led to an increase in the adoption of additive manufacturing technologies across the aerospace sector, with companies like {} playing a pivotal role in driving these advancements.
In healthcare, additive manufacturing has opened up new possibilities for the production of customized medical devices and implants. By using 3D scanning technology to create precise digital models of patients' anatomy, medical professionals are able to design and produce personalized implants that fit the patient perfectly. This has led to improved patient outcomes and reduced recovery times, demonstrating the potential of additive manufacturing to revolutionize the healthcare industry.
The automotive industry has also seen significant benefits from additive manufacturing, with the ability to produce lightweight and complex parts that can improve performance and fuel efficiency. Additionally, additive manufacturing has allowed for the production of customized and limited-edition parts for vehicles, giving automotive manufacturers more flexibility in their design and production processes.
As additive manufacturing continues to evolve, companies like {} are leading the way in developing new materials and technologies that push the boundaries of what is possible. By investing in research and development, {} has been able to offer cutting-edge solutions that enable its customers to take full advantage of the benefits of additive manufacturing.
In addition to its technological advancements, {} has also focused on providing comprehensive support and training to its customers, ensuring that they are able to leverage additive manufacturing to its full potential. With a team of experts and a global network of partners and distributors, {} is committed to helping its customers succeed in the rapidly evolving world of additive manufacturing.
With its dedication to innovation and customer success, {} has positioned itself as a key player in the additive manufacturing industry. As the demand for 3D printing technologies continues to grow, {} will undoubtedly play a crucial role in shaping the future of manufacturing across various industries. With a commitment to sustainability, innovation, and customer satisfaction, {} is well-positioned to lead the way in the additive manufacturing revolution.
Company News & Blog
Top Precision CNC Machining Parts Suppliers in China for Quality Products
China’s CNC Precision Machining Parts Industry Thrives Amidst Growing DemandChina’s CNC precision machining parts industry has been growing steadily over the past few years due to the increasing demand for such products across various industries. With this rise, hundreds of companies have emerged as prominent manufacturers and suppliers of high-quality CNC precision machining parts. One such company leading the way is WEIMI, a professional manufacturer of CNC precision machining parts in China.WEIMI is a well-known company with a reputation for reliability, high-quality products, and excellent customer service. The company has been operating in the CNC machining parts industry for more than ten years and has extensive experience and technical expertise in designing and manufacturing a wide range of CNC precision machining parts.The company has a team of experts who are skilled and experienced in using the latest technology to create top-quality products at competitive prices. They have helped WEIMI establish itself as a leading supplier of CNC machining parts, serving industries ranging from automotive, industrial machinery, aerospace, electronics, communications, and many others.WEIMI’s CNC precision machining parts production facility is equipped with the latest machinery and technology to ensure that the highest quality products are produced. The company uses advanced software and machines such as CAD/CAM, CNC lathes, milling machines, and others to produce precision components that meet the most stringent quality standards.One of the advantages of working with WEIMI is that they provide customized CNC precision machining parts to meet specific customer requirements. The company has a team of experts who work with clients to understand their needs and create products that meet those needs. This service has helped companies across various industries to improve the efficiency and productivity of their operations.As the CNC machining parts industry in China continues to grow, WEIMI is well-positioned to remain a leader in the market. The company has a proven track record of designing and manufacturing quality products that meet the changing needs of its clients. Another factor that has helped the company to grow is China’s status as the world’s largest manufacturing hub. The country has established itself as a powerhouse in the global manufacturing industry. It boasts of a vast supply chain and highly skilled labor force, making it an ideal location for manufacturing companies.China’s government has also played a significant role in encouraging the growth of the CNC machining parts industry. The government has introduced several policies aimed at supporting the development of the manufacturing industry, including tax incentives, subsidies, and other support measures. These initiatives have helped to create a conducive environment for companies such as WEIMI to thrive.Overall, the CNC precision machining parts industry in China is expected to continue seeing growth in the coming years. As the world’s major economies continue to recover from the COVID-19 pandemic, the demand for precision parts and components across various industries is expected to increase. WEIMI is poised to play an essential role in meeting this demand, thanks to its commitment to quality, innovation, and custom production of CNC precision machining parts that meet the specific needs of its clients.In conclusion, the CNC precision machining parts industry in China is thriving thanks to the growing demand for such products across various industries. WEIMI and other companies are leading the way in designing and manufacturing high-quality CNC precision machining parts that meet the most stringent quality standards. With China’s government support and the country’s status as a global manufacturing hub, the prospects for the industry remain bright.
High-Quality Deep Drawn Sheet Metal Components for Your Metal Fabrication Projects
[Company Name], a leading manufacturer of deep drawn sheet metal components, has recently announced the launch of its new product line. These components are designed to meet the growing demand for high-quality, custom-made metal parts in various industries such as automotive, aerospace, electronics, and more.With over [number of years] years of experience in the industry, [Company Name] has established itself as a reliable and innovative supplier of deep drawn sheet metal components. The company’s state-of-the-art manufacturing facilities and cutting-edge technology allow them to produce complex and precise metal parts that meet the strictest industry standards. Their commitment to quality and customer satisfaction has helped them build a strong reputation in the market.The new product line includes a wide range of deep drawn sheet metal components, such as enclosures, housings, brackets, and connectors. These components are manufactured using advanced deep drawing processes that ensure superior dimensional accuracy and surface finish. [Company Name] employs a team of skilled engineers and technicians who work closely with customers to develop custom solutions that meet their specific requirements.One of the key advantages of deep drawn sheet metal components is their ability to achieve complex geometries and tight tolerances, making them ideal for applications where precision and reliability are crucial. The components are also highly durable and cost-effective, offering a unique combination of strength and lightweight design. This makes them suitable for various applications, including automotive components, electronic enclosures, sensor housings, and more.[Company Name]’s deep drawn sheet metal components are manufactured using a variety of materials, including stainless steel, aluminum, copper, and brass. These materials are selected based on the specific requirements of each application, ensuring that the components meet the necessary performance and durability standards. In addition, the company is also able to provide various surface finishes and coatings to further enhance the functionality and appearance of the components.In addition to the new product line, [Company Name] offers a range of value-added services to support their customers throughout the entire product development and manufacturing process. These services include design assistance, prototyping, tooling design and fabrication, and in-house testing and inspection. This comprehensive approach allows [Company Name] to deliver cost-effective and high-quality solutions that meet the most demanding industry requirements.With the launch of the new product line, [Company Name] aims to further expand its presence in the global market and strengthen its position as a leading provider of deep drawn sheet metal components. The company’s commitment to innovation, quality, and customer satisfaction will continue to drive its success in the industry, as it strives to meet the evolving needs of its customers and deliver exceptional value through its products and services.Looking ahead, [Company Name] is poised to continue its growth and investment in new technologies and capabilities to further enhance its ability to meet the demands of its customers. By staying at the forefront of industry trends and advancements, the company is well-positioned to remain a reliable and innovative partner for deep drawn sheet metal components across a wide range of industries.
What is Water-jet Technology and How Does it Work?
Water-jet technology has evolved significantly over the years, providing a versatile and efficient solution for a range of industrial applications. This technology involves the use of a high-pressure pump to create a stream of water that can be used to cut, clean, and shape different materials. Water-jet technology is fast becoming the go-to option for many employers in varied industries.The process of water-jet cutting starts by using a high-pressure pump that pumps water through a nozzle, which produces a super-fast stream of water that is directed onto the material to be cut. The water pressure can be adjusted to suit the type of material being cut, from soft materials like plastic, rubber, and foam to hard materials like metals, ceramics, and glass.One of the most significant benefits of water-jet technology is its ability to perform intricate cuts without creating heat-affected zones (HAZ). Thermal distortion, discoloration, and other undesirable effects are often seen when traditional cutting methods are used, like plasm cutting. However, water-jet cutting ensures material integrity through cold cutting, making it ideal for precision machining, intricate architectural designs, medical equipment, aerospace, and automotive parts.Traditional cutting methods such as laser and plasma can produce toxic fumes or debris that can be dangerous to the environment and human health. In contrast, water-jet cutting is eco-friendly and safe. The water used in this process can be recycled and reused, and the cutting operation produces no hazardous waste, allowing companies to reduce their environmental footprint considerably.Moreover, water-jet technology requires no special tooling, which means changing between different materials and designs is a breeze. This makes water-jet cutting an even more attractive option for manufacturers who need to switch between various production requirements quickly. Additionally, with advancements in technology, 5-axis cutting technology and robotics can be utilized, allowing greater flexibility and increased accuracy in cutting, ensuring more efficient and cost-effective production.The benefits of water-jet technology are not limited to cutting and shaping applications, as it has other uses too. Water-jet cleaning is another application of this technology. It involves the use of high-pressure water streams to remove dirt and grime from surfaces, making it an effective cleaning option for many businesses. Cleaning using a water-jet is particularly useful in the food and beverage industry, where sanitation is critical.Another advantage of using water-jet technology in cleaning is that it does not require any chemicals to aid the cleaning process. This, in turn, ensures that the cleaned surfaces are safe for human consumption, eliminating the need for chemical-based cleaning agents harmful to the environment and humans. The use of water-jet technology in cleaning can significantly reduce washing times and increase production efficiency, making it an ideal solution for many businesses.In conclusion, water-jet technology presents an innovative and eco-friendly solution for many manufacturing and cleaning applications. Its benefits are unrivaled when compared to traditional cutting and cleaning technologies. From increased production efficiency to reduced environmental footprint to the ability to perform intricate and precise cuts, water-jet technology has fast become a sought-after option for many businesses looking to improve their bottom line. Companies that have not yet implemented this technology in their operations are urged to give it a try and discover the numerous cost and time-saving benefits it can offer.
Sheet Metal: A Fundamental Form in Metalworking
Title: Sheet Metal Flat: Revolutionizing Industrial Fabrication ProcessesIntroduction:(sheet metal flat logo)Sheet Metal Flat is a renowned leader in the field of sheet metal fabrication. With a commitment to innovation and quality, the company continues to revolutionize the manufacturing industry. Their expertise lies in the production of thin, flat pieces of metal that can be easily cut and shaped into various forms. This article delves into the significance of sheet metal fabrication, explores the various applications, and highlights Sheet Metal Flat's contributions to this field.Importance of Sheet Metal Fabrication:Sheet metal fabrication plays a pivotal role in numerous industries, making it one of the fundamental forms used in metalworking. By utilizing industrial processes, sheet metal is transformed into thin, flat pieces which can then be molded into a variety of shapes. This versatility enables the creation of countless everyday objects that are an integral part of our lives.Applications of Sheet Metal:The applications of sheet metal fabrication are vast and diverse. From the automotive sector to construction, aerospace, and even household appliances, sheet metal is an essential component in the production of various products. It is widely used in the manufacturing of automobile parts, including body panels, chassis, and engine components due to its durability, strength, and resistance to corrosion.In the construction industry, sheet metal is utilized for roofing, facades, and structural elements due to its lightweight nature and high durability. The aerospace industry leverages sheet metal for aircraft structures, providing strength, stability, and resilience at high altitudes. In household appliances, sheet metal is employed in the manufacturing of refrigerators, stoves, and washing machines due to its ability to withstand high temperatures and repeated use.Sheet Metal Flat: Pioneers in Fabrication:Sheet Metal Flat has emerged as a reliable and innovative player in the sheet metal fabrication industry. The company's commitment to cutting-edge technology and exceptional quality has positioned them as a distinguished leader.Efficient Manufacturing Processes: Sheet Metal Flat employs state-of-the-art machinery and equipment to ensure precision and efficiency in their manufacturing processes. From laser cutting to stamping, bending, and welding, they have perfected every stage of fabrication. This enables them to deliver superior end products while ensuring timely production.Custom Solutions: Recognizing the unique requirements of each client, Sheet Metal Flat offers customized solutions tailored to suit their specific needs. Their team of experienced technicians works closely with customers, providing expert guidance and utilizing cutting-edge software to design and create flawless sheet metal components.Quality Assurance: Sheet Metal Flat is committed to delivering products of the highest quality. Rigorous quality control measures, including inspections at different stages of production, are in place to ensure that every piece meets the highest standards. By adhering to strict quality control protocols, Sheet Metal Flat has fostered long-lasting relationships with their clients.Environmental Responsibility: In an era of increasing environmental awareness, Sheet Metal Flat is committed to minimizing their carbon footprint. They have implemented eco-friendly practices such as recycling scrap metal, reducing waste generation, and incorporating energy-efficient machinery. By choosing Sheet Metal Flat, customers can align with their sustainability goals.Conclusion:Sheet Metal Flat's contribution to the sheet metal fabrication industry cannot be understated. With their innovative manufacturing processes, commitment to quality, and dedication to customer satisfaction, they have set new benchmarks in the field. As the demand for sheet metal continues to grow across various sectors, Sheet Metal Flat is poised to remain at the forefront, constantly pushing the boundaries of possibility and redefining the standards for industrial metalworking.
Custom Sheet Metal Parts: A Complete Guide to Manufacturing and Use
For more than 20 years, the dedicated team at [Company Name] has been a leader in the manufacturing of high-quality sheet metal parts for a wide range of industries. The company's commitment to excellence and customer satisfaction has earned them a stellar reputation in the industry. Recently, [Company Name] unveiled their latest innovation in sheet metal part manufacturing, which is set to revolutionize the industry. This new product offers enhanced durability, precision, and efficiency, making it a game-changer for their clients.The new sheet metal part is designed using state-of-the-art technology and advanced engineering techniques. It has been meticulously crafted to meet the highest industry standards and to exceed the expectations of even the most discerning customers. The result is a product that is not only incredibly durable but also incredibly precise, making it perfect for a wide range of applications.One of the key features of the new sheet metal part is its enhanced durability. This is achieved through the use of high-quality materials and the implementation of advanced manufacturing processes. This ensures that the part is able to withstand even the most demanding conditions, making it an ideal choice for industries such as automotive, aerospace, and construction.In addition to its durability, the new sheet metal part also offers unmatched precision. This is achieved through the use of cutting-edge technology and the company's commitment to quality control. Every part is meticulously inspected to ensure that it meets the strictest tolerances, resulting in a product that is incredibly precise and consistent.Furthermore, the new sheet metal part is also incredibly efficient. Its innovative design and manufacturing processes have been optimized to minimize waste and maximize productivity. This not only benefits the environment but also allows for cost savings, making it an attractive option for businesses looking to improve their bottom line.The introduction of this new sheet metal part further solidifies [Company Name]'s position as an industry leader. Their commitment to innovation and excellence has set them apart from their competitors, and this latest product is a testament to their dedication to providing the best possible solutions for their clients.In addition to their innovative products, [Company Name] also prides itself on its exceptional customer service. Their team of experts is always available to provide guidance and support, ensuring that their clients have everything they need to succeed.As the industry continues to evolve, [Company Name] remains at the forefront, consistently pushing the boundaries of what is possible in sheet metal part manufacturing. Their latest innovation is a testament to their commitment to excellence and their dedication to meeting the needs of their clients.In conclusion, the introduction of [Company Name]'s new sheet metal part is set to revolutionize the industry. With its enhanced durability, precision, and efficiency, it is sure to become the go-to choice for businesses across a wide range of industries. This latest innovation further solidifies [Company Name]'s position as an industry leader, and their dedication to excellence and customer satisfaction is sure to set them apart for years to come.
Sheet Metal Manufacturing for Prototypes and Production Runs of Various Metal Parts
Sheet Metal Die: Providing Top-Quality Sheet Metal Manufacturing ServicesSheet Metal Die is a leading provider of sheet metal manufacturing services, offering a wide range of high-quality solutions to meet the needs of businesses across various industries. The company has established a reputation for delivering exceptional accuracy, precision, and speed, all while maintaining a commitment to customer satisfaction.With over 20 years of experience in sheet metal manufacturing, Sheet Metal Die has developed a deep expertise in the production of custom sheet metal parts. Whether businesses need simple bent metal prototypes or complex, multi-part electro-mechanical assemblies, the company has the knowledge, technology, and equipment required to get the job done right.The company offers a range of sheet metal manufacturing services, including laser cutting, punching, forming, welding, and powder coating. These services are performed using state-of-the-art equipment and technology, ensuring that every part meets exact specifications and conforms to the highest quality standards.Sheet Metal Die also processes a wide range of materials, including aluminum, stainless steel, carbon steel, copper, brass, and galvanized steel. This versatility allows businesses to choose the ideal material for their specific application or industry needs.For businesses that need fast turnaround times, Sheet Metal Die offers quick-response services that provide rapid prototyping and short-run production capabilities. These services are ideal for projects that have tight deadlines or require fast turnaround times.Sheet Metal Die is also committed to providing exceptional customer service, beginning with a personalized consultation that takes into account a business's specific needs and goals. The company's experts work closely with clients to determine the best approach to their project, taking into account factors such as material choice, manufacturing timeline, and cost-effectiveness.The team at Sheet Metal Die is also dedicated to ongoing training and development, ensuring that all staff members are up-to-date with the latest industry trends and manufacturing techniques. Additionally, the company is committed to using environmentally sustainable practices, reducing waste and energy usage wherever possible.Overall, Sheet Metal Die is an ideal partner for businesses that require top-quality sheet metal manufacturing services. With its expertise, technology, and commitment to customer satisfaction and sustainable practices, the company is well-equipped to meet the needs of clients across a wide range of industries.
Custom Aluminium Extrusions for Your Specific Needs
In today's fast-paced and continuously developing modern world, businesses have to keep up with the growing needs of their clientele. One way to do that is through offering customized products, tailored to meet the specific requirements of the customer. Avocet Precision Metals has taken up that challenge, offering aluminum extrusion services that cater to the unique needs of the client.Avocet Precision Metals is a premier metals manufacturing company, located in the United Kingdom, known for its dedication to providing high-quality metal products and exceptional customer service. The firm utilizes cutting-edge technologies and equipment to provide unmatched precision in producing aluminum extrusions that meet the highest industry standards. With a workforce of highly skilled and experienced professionals well-versed in the latest practices of the extrusion industry, Avocet Precision Metals delivers results that surpass expectations.At its core, aluminum extrusion is a process by which manufacturers create complex shapes by forcing aluminum through a shaped opening. This process allows for customization of aluminum products to meet the exact specifications of clients. Avocet Precision Metals recognizes the importance of this process, making sure that all products conform to the customer's design, ensuring that products are manufactured to the highest quality standards.The company utilizes both hard and soft alloys of aluminum to match the specific requirements of the client. If the customer requires a particular combination of strength, corrosion resistance, and lightness, Avocet Precision Metals can deliver precisely what is needed. The company's aluminum extrusion services are highly versatile and can be used in a wide range of applications, including automotive, construction, machinery and much more.Avocet Precision Metals prides themselves in employing best practices, and quality measures to deliver the best customer experience. The company ensures that all the aluminum extrusion products are produced in an environmentally sustainable manner. The manufacturing process is regulated to ensure that it is as green as possible, minimizing the impact on the environment while ensuring that the customer receives high-quality products. Additionally, the company takes its customers' safety seriously and has worked hard to develop and implement safety and environmental protection policies.The high quality of the products that Avocet Precision Metals delivers is made possible by the company's continued investment in modern technology. This significantly reduces the production lead times and guarantees that the products are at the highest level of precision and quality. The company has installed cutting-edge CNC machines and presses that enable the team to manufacture high volumes of aluminum extrusions while reducing waste and maximizing efficiency.Avocet Precision Metals recognizes that customers have different budgets, and the company is always willing to work with clients to find a solution that works best for them. The company is committed to funding a team that supports its customers even after the sale is completed. They have an expert team of professionals on standby, ready to offer guidance and answer any queries that may arise.As a leading player in the aluminum extrusion industry, Avocet Precision Metals is continuously innovating and improving its processes to ensure they stay ahead of the competition. This continuous improvement mindset ensures that the company remains relevant in a market that is constantly changing. The firm's commitment to providing customers with the highest quality products and services has earned Avocet Precision Metals an excellent reputation among its customers and industry peers.In summary, Avocet Precision Metals is a top-tier manufacturer of aluminum extrusions that delivers high-quality and customized products according to clients' specifications. They are a company that prioritizes customer satisfaction and has invested in cutting-edge technology, skilled personnel, while staying environmentally conscious. These steps have enabled them to deliver on their promises while expanding their clientele base, and solidifying its position as a leading industry player.
Precision Sheet Metal Brackets Made with Advanced Manufacturing Techniques
: A Comprehensive Guide for Your Manufacturing NeedsSheet metal brackets are an integral part of any manufacturing process that requires the use of metal sheets. In industries that require immense precision and accuracy, the bracket systems ensure that the metal’s shape and structure are maintained throughout the process. With the advancements in modern CNC manufacturing processes, the quality of these bracket systems has improved significantly. The use of advanced automation tools has led to more efficient and precise manufacturing methods.Sheet metal brackets are widely used in various industries such as Aerospace, Medical, Automotive, Construction, and Electronics. In construction, sheet metal brackets are used to provide support to the structural systems, and in electronics, they secure electronic components in place. With their versatility, sheet metal brackets are an essential component in several processes and products.Here is a comprehensive guide to sheet metal brackets for all your manufacturing needs:Types of Sheet Metal Brackets1. Angle Brackets: These are brackets that are bent to 90-degree angles to create perpendicular structural joints. They are commonly used in construction to ensure that the structures maintain their shape and stability.2. U Brackets: These brackets have a U-shaped cross-section that is used to create a mounting point for objects. They are commonly used to mount objects onto walls and other surfaces.3. L Brackets: These are brackets that are bent to form an L-shape. They are used in most applications requiring reinforcement to prevent structural deformation.4. Z Brackets: These are brackets that are bent to form a ‘Z’ shape. They are used in construction to provide additional support to the structural systems.5. T Brackets: These are brackets that are bent to form a T-shape. They are commonly used to attach objects onto walls or other surfaces.Applications of Sheet Metal BracketsSheet metal brackets are used in various applications, including:AerospaceIn the aerospace industry, brackets are used to mount different types of equipment and systems such as electronics, fuel systems, engines, and landing gear. The brackets are usually made from lightweight materials like aluminum to minimize weight.AutomotiveIn the automotive industry, brackets are essential in holding the structural components of the car together. They are also used in securing electrical components in place.ConstructionSheet metal brackets are used extensively in the construction industry for many different applications, such as securing wall studs and reinforcing roof structures.ElectronicsIn the electronics industry, sheet metal brackets are used to secure electronic components in place. They are also used in creating housing systems for electrical components.MedicalSheet metal brackets are used in medical equipment and devices to support and hold various pieces of equipment such as monitors, IV poles, and other medical components in place.Manufacturing ProcessWith advancements in modern CNC manufacturing processes, sheet metal brackets can be precisely and efficiently manufactured. The manufacturing process for sheet metal brackets includes the following stages:1. Material Selection: The sheets of metal used in creating the brackets are usually made from various metals such as Stainless Steel, Carbon Steel, and Aluminum, and copper.2. Laser Cutting: The sheets of metal are cut using laser cutting machines to create the individual brackets' required shapes and sizes.3. Bending: The cut sheet metal is then bent using precision bending machines to create the desired shape of the bracket.4. Welding or Fixing: After bending the metal, the bracket components are welded or fixed together to create a final product.5. Finishing: The finished brackets are sandblasted or painted to give it a final finish.ConclusionSheet metal brackets are a vital part of many manufacturing processes. They provide structural support, aid in mounting equipment and components, and ensure precise manufacturing processes. The modern CNC manufacturing processes have significantly improved the manufacturing process of sheet metal brackets, leading to more efficient, accurate, and high-quality products. If you need sheet metal brackets for your manufacturing processes, ensure that you engage a reputable and experienced manufacturer who can deliver the desired results.
Get High-Quality CNC Automation Parts for Improved Efficiency and Precision
CNC Automation Solutions' Revolutionary New Parts Drive Improved Efficiency and Precision in ManufacturingCNC Automation Solutions is proud to announce the release of its latest CNC automation parts. After years of research and development, our team of engineers has created an innovative and cutting-edge solution that promises to drive unparalleled levels of efficiency and precision within the manufacturing industry.Our latest CNC automation parts have been designed to cater to the specific needs of the manufacturing industry, by integrating leading-edge technology and incorporating the latest industry standards. Our parts are custom-designed to offer exceptional speed, precision, and reliability, catering to a broad range of manufacturing processes. With our parts, manufacturers can produce high-quality products within a precise timeline without compromising on quality.In a statement, the CEO of CNC Automation Solutions, said, "We are delighted to bring our innovative and state-of-the-art CNC automation parts to the manufacturing sector. Our team of engineers has been working tirelessly to create a solution that maximizes efficiency while eliminating the risk of human error, leading to outstanding results. Our parts are designed to meet and exceed industry standards, and we are confident that they will be highly sought after by the manufacturing community."CNC Automation Solutions has built a name for itself by delivering innovative solutions that cater to the specific needs of the manufacturing industry. Our industry expertise, coupled with our commitment to providing excellent customer service, make us the go-to company when seeking automation solutions. Our revolutionary new parts are no exception, as they provide exceptional value to our customers. By reducing the time required for set-up and changeover, with parts that are adaptable to different kinds of equipment, our parts improve overall process efficiency, as manufacturers can produce more baskets with a lesser amount of resources and time.Our latest CNC automation parts are the result of years of collaboration and development. They incorporate advanced features like cutting-edge software, modular and scalable designs, and high-quality materials that lead to improved precision and accuracy. Our parts are highly customizable, and we work closely with our clients to ensure that our products are precisely tailored to their specific needs. Whether a manufacturer is operating a small workshop or a large-scale factory, our parts are designed to cater to all kinds of operations. This adaptability allows for greater flexibility, enabling manufacturers to scale their businesses with ease.Perhaps the biggest advantage of our parts is that they help minimize the risk of human error. Traditional manufacturing methods are prone to errors due to inaccuracy that could have an adverse impact on overall efficiency. However, with our automated parts, manufacturers no longer have to worry about such errors. This advantage translates to better product quality, a lessened need for manual labor, and ultimately a significant reduction in production costs.In conclusion, CNC Automation Solutions' latest CNC automation parts represent a significant step forward in the manufacturing industry. These innovative products are set to revolutionize the world of manufacturing, promising unparalleled levels of efficiency and precision. Our parts are designed to increase productivity, reduce costs, and minimize the risk of human error. We are confident that our new parts will be warmly embraced by the manufacturing community and look forward to working with our clients, to provide them with a solution that will have a tangible impact on their businesses.
Download Softwares and Updates for Fieldbus Configuration and Diagnostic Programs
Software Download for Sheet Metalwork: Streamlining Your ProcessesIn today's fast-paced and highly technological era, software and technology have become integral parts of almost every industry, including sheet metalwork. Software can help automate complex processes, reduce costs, improve accuracy, and increase efficiency. With the availability of software downloads for sheet metalwork, you can take the first step towards streamlining your workflows and accelerating your productivity.But what exactly can software downloads offer to sheet metalwork fabricators? Let's take a closer look.Automating ProcessesSheet metalwork fabrication involves multiple complex processes, from designing and prototyping to cutting and forming the material. Software can automate many of these processes, saving time and reducing errors. For instance, CAD (Computer-Aided Design) software can help you create accurate and detailed 2D and 3D models with precise dimensions and tolerances. This eliminates the need for manual drawings, which can be time-consuming and prone to errors.Similarly, CAM (Computer-Aided Manufacturing) software can generate G-code for CNC machines, which can automate the cutting, drilling, and forming of sheet metal parts. It can also optimize the cutting paths, minimizing waste and reducing material costs. Additionally, software can generate BOMs (Bills of Materials) and track inventory levels, making it easier to manage and reorder materials.Enhancing CommunicationEffective communication is crucial in sheet metalwork, especially when dealing with complex geometries and tight tolerances. Software can enhance communication between design, manufacturing, and quality control teams, ensuring that everyone is working towards the same objectives. For example, PLM (Product Lifecycle Management) software can provide a single source of truth for all product-related data, including design files, BOMs, specifications, and quality records. This can help reduce delays, rework, and errors due to miscommunication or misunderstandings.Improving QualityQuality is one of the most critical aspects of sheet metalwork fabrication. Even small errors or deviations can compromise the performance, safety, or reliability of the final product. Software can help improve quality by automating inspections and tests, tracking defects, and analyzing data. For example, CMM (Coordinate Measuring Machine) software can compare the actual dimensions of a part with its design specifications and generate reports with detailed measurements and statistical analyses. This can help identify any deviations or trends that need to be addressed.Software can also integrate with quality standards and certifications, such as ISO 9001 or AS9100. This can help ensure that your products meet the required quality standards and that your processes are auditable and compliant.ConclusionIn summary, software downloads can offer numerous benefits to sheet metalwork fabricators, from automating processes and enhancing communication to improving quality and compliance. However, choosing the right software and implementing it effectively can be challenging. It is crucial to evaluate your needs, budget, and resources, and to seek expert advice from software providers or consultants. With the right software and approach, you can enhance your productivity, profitability, and competitiveness in the sheet metalwork industry.