Get High-Quality CNC Automation Parts for Improved Efficiency and Precision
By:Admin
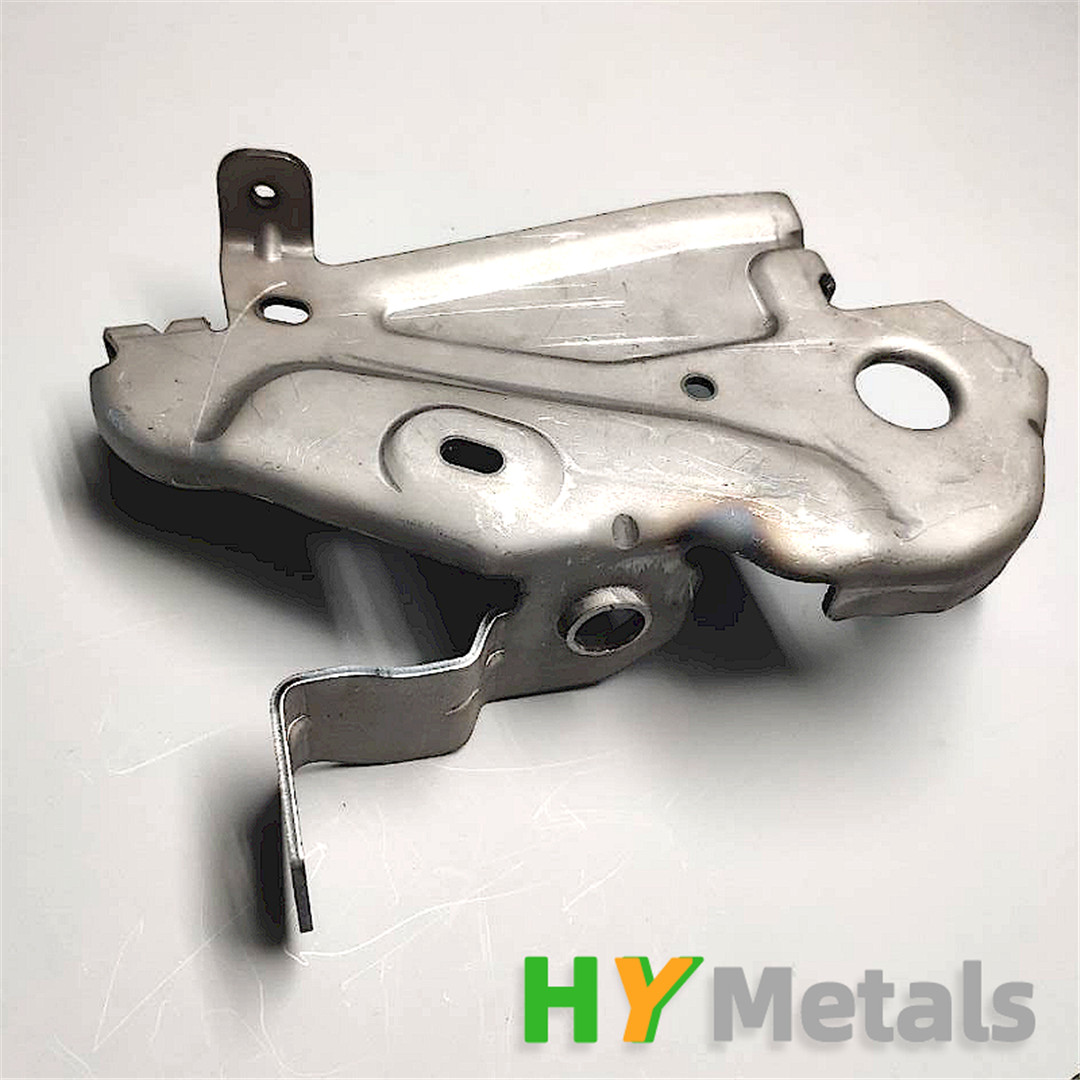
CNC Automation Solutions is proud to announce the release of its latest CNC automation parts. After years of research and development, our team of engineers has created an innovative and cutting-edge solution that promises to drive unparalleled levels of efficiency and precision within the manufacturing industry.
Our latest CNC automation parts have been designed to cater to the specific needs of the manufacturing industry, by integrating leading-edge technology and incorporating the latest industry standards. Our parts are custom-designed to offer exceptional speed, precision, and reliability, catering to a broad range of manufacturing processes. With our parts, manufacturers can produce high-quality products within a precise timeline without compromising on quality.
In a statement, the CEO of CNC Automation Solutions, said, "We are delighted to bring our innovative and state-of-the-art CNC automation parts to the manufacturing sector. Our team of engineers has been working tirelessly to create a solution that maximizes efficiency while eliminating the risk of human error, leading to outstanding results. Our parts are designed to meet and exceed industry standards, and we are confident that they will be highly sought after by the manufacturing community."
CNC Automation Solutions has built a name for itself by delivering innovative solutions that cater to the specific needs of the manufacturing industry. Our industry expertise, coupled with our commitment to providing excellent customer service, make us the go-to company when seeking automation solutions. Our revolutionary new parts are no exception, as they provide exceptional value to our customers. By reducing the time required for set-up and changeover, with parts that are adaptable to different kinds of equipment, our parts improve overall process efficiency, as manufacturers can produce more baskets with a lesser amount of resources and time.
Our latest CNC automation parts are the result of years of collaboration and development. They incorporate advanced features like cutting-edge software, modular and scalable designs, and high-quality materials that lead to improved precision and accuracy. Our parts are highly customizable, and we work closely with our clients to ensure that our products are precisely tailored to their specific needs. Whether a manufacturer is operating a small workshop or a large-scale factory, our parts are designed to cater to all kinds of operations. This adaptability allows for greater flexibility, enabling manufacturers to scale their businesses with ease.
Perhaps the biggest advantage of our parts is that they help minimize the risk of human error. Traditional manufacturing methods are prone to errors due to inaccuracy that could have an adverse impact on overall efficiency. However, with our automated parts, manufacturers no longer have to worry about such errors. This advantage translates to better product quality, a lessened need for manual labor, and ultimately a significant reduction in production costs.
In conclusion, CNC Automation Solutions' latest CNC automation parts represent a significant step forward in the manufacturing industry. These innovative products are set to revolutionize the world of manufacturing, promising unparalleled levels of efficiency and precision. Our parts are designed to increase productivity, reduce costs, and minimize the risk of human error. We are confident that our new parts will be warmly embraced by the manufacturing community and look forward to working with our clients, to provide them with a solution that will have a tangible impact on their businesses.
Company News & Blog
Advanced Machining Techniques for Precision Milling Operations
Machining Milling, a prominent player in the machining industry, is revolutionizing the landscape of precision manufacturing. With their unwavering commitment to quality and innovation, the company has firmly established itself as a frontrunner in the market. Through their cutting-edge technologies and customer-centric approach, Machining Milling has become a go-to partner for businesses aiming to achieve superior quality and precision.Founded with a vision to redefine the machining industry, Machining Milling brings years of expertise and experience. Their team of highly skilled professionals is dedicated to producing exceptional results, adhering to strict quality control measures at every phase of the manufacturing process. By employing state-of-the-art machinery and sophisticated software, they ensure that each product meets the highest industry standards.One of the cornerstones of Machining Milling's success is their commitment to continuous improvement. The company constantly invests in research and development to stay ahead of technological advancements and meet the evolving needs of their customers. This allows them to provide tailor-made solutions, ensuring that every project is executed with precision and efficiency.Machining Milling's diverse range of services caters to a wide array of industries including aerospace, automotive, medical, and energy sectors. From concept to completion, their comprehensive manufacturing solutions encompass precision machining, milling, turning, and assembly. By utilizing cutting-edge techniques like computer numerical control (CNC) machining, they are able to deliver complex and intricate components with unparalleled accuracy.The company's dedication to customer satisfaction is evident in their personalized approach. Machining Milling works closely with each client, understanding their unique requirements, and providing customized solutions to meet their specific needs. Their team of experts collaborates with clients throughout the entire process, ensuring effective communication and a seamless manufacturing experience.One of the notable factors that distinguish Machining Milling from its competitors is their strong emphasis on quality assurance. The company adheres to stringent quality control protocols, ensuring that each product undergoes meticulous inspection and testing. This commitment to quality has earned Machining Milling numerous certifications, reflecting their unwavering dedication to excellence.Furthermore, Machining Milling recognizes the importance of sustainability in today's manufacturing landscape. The company is committed to minimizing its environmental impact by adopting environmentally friendly practices. They prioritize the use of eco-friendly materials and implement energy-efficient measures throughout their operations.Machining Milling's exceptional track record and commitment to excellence have earned them a loyal customer base. With a reputation for delivering on time and exceeding expectations, they have forged long-term partnerships with industry giants. Their commitment to continuous improvement and customer satisfaction sets them apart in the highly competitive machining industry.Looking to the future, Machining Milling aims to further expand their capabilities and technological prowess. By embracing the latest advancements, they continue to enhance their efficiency and precision, providing innovative solutions to meet the evolving demands of the market.In conclusion, Machining Milling has emerged as a leading name in the machining industry. With their commitment to quality, innovation, and customer satisfaction, they have redefined precision manufacturing. Through cutting-edge technologies, personalized approaches, and unwavering dedication to excellence, Machining Milling continues to set the benchmark for superior machining services.
Expert Thermal Management Consulting for High Performance Electronics
In the world of electronics, thermal management is one of the most important factors that can make or break the success of a product. When electronic circuits run, they generate heat, and if this heat is not properly dissipated, it can cause a range of problems, from degraded performance to component failure. This is where thermal management solutions come in, and Q ATS is a leading provider of such solutions.Founded with the aim of helping electronic product manufacturers bring their products to market faster, safer, and at a lower cost, Q ATS has established itself as a trusted partner for companies in a variety of industries. Whether it's designing a custom heatsink for a high-power LED light or analyzing the thermal performance of a data center, Q ATS has the expertise and experience to help clients solve their thermal management challenges.One of the key advantages of working with Q ATS is their comprehensive approach to thermal management analysis and design. Rather than simply offering off-the-shelf solutions, their team of engineers work closely with clients to understand the unique requirements of their products and design custom solutions that meet those needs. This ensures that clients get the best possible thermal performance for their products, while minimizing costs and time-to-market.Some of the services offered by Q ATS include thermal modeling and simulation, which allows them to predict the thermal performance of a product before it's even built. This can be especially valuable in applications where thermal management is critical, such as aerospace and defense. Q ATS also offers design and prototyping services, allowing clients to test and iterate on their thermal management solutions before committing to production.Another key area of expertise for Q ATS is the design and manufacture of heatsinks, which are a critical component in many electronic products. Heatsinks are used to dissipate heat from a component or circuit board to the surrounding air, and Q ATS can design heatsinks that are optimized for a specific application, providing maximum performance while minimizing weight and cost.In addition to their technical expertise, Q ATS is also committed to providing exceptional customer service. They work closely with clients throughout every stage of the project, from initial consultation to final delivery, ensuring that their needs are fully understood and met. Their team is highly responsive, with quick turnaround times and a willingness to go the extra mile to ensure client satisfaction.Overall, Q ATS is a valuable partner for any company looking to improve the thermal performance of their electronic products. With their comprehensive approach, technical expertise, and commitment to customer service, they can help clients get their products to market faster, safer, and more cost-effectively than ever before.
Exploring Versatile and Efficient Options for Rapid Prototyping
Rapid Prototyping Options: Revolutionizing Prototyping ServicesIn today's competitive business environment, companies are constantly pushing the boundaries of innovation to stay ahead of the curve. One critical aspect of this innovation is rapid prototyping, which is essential for designing and testing new products. To remain competitive, companies need agile and efficient prototyping services that produce high-quality, functional prototypes at a rapid pace. That's where Rapid Prototyping Options (need to remove brand name) comes in.Rapid Prototyping Options (RPO) is a leading provider of rapid prototyping services that cater to a diverse range of industries, including aerospace, automotive, medical, and consumer products. With over a decade of experience in the industry, the company has consistently provided high-quality, cost-effective prototyping services that have helped clients accelerate innovation and bring products to market faster.At the heart of RPO's success is its commitment to using cutting-edge technology and advanced manufacturing techniques in its prototyping services. The company combines traditional manufacturing methods with innovative technologies like 3D printing, CNC machining, and injection molding to produce customized, high-quality prototypes that accurately represent the final product.RPO's 3D printing capabilities are among the most advanced in the industry. The company leverages a variety of 3D printing technologies, including Fused Deposition Modeling (FDM), Stereolithography (SLA), and Selective Laser Sintering (SLS), to produce accurate, high-resolution prototypes. These prototypes can be made from a variety of materials, including plastic, metal, and even rubber, depending on the client's specific requirements.Another critical prototyping service offered by RPO is CNC machining. The company's state-of-the-art CNC machines can produce high-quality prototypes from a variety of materials, including metals, plastics, and composites. RPO's CNC machining capabilities allow clients to produce prototypes with precise dimensions and complex geometries, making it an ideal solution for industries like aerospace and automotive, where precision and accuracy are critical.For larger production runs, RPO offers injection molding services. The company's injection molding capabilities allow clients to produce high-quality, injection-molded parts quickly and efficiently. With RPO's injection molding services, clients can avoid the high startup costs associated with traditional injection molding and quickly produce functional, high-quality parts without sacrificing quality.One key aspect of RPO's prototyping services that sets it apart from competitors is its focus on customer service. The company's prototyping experts work closely with clients throughout the prototyping process to ensure that their needs are met and their expectations are exceeded. From initial consultations to prototyping design to final production, RPO is committed to providing world-class prototyping services that meet the highest standards of quality, accuracy, and reliability.RPO's prototyping services have been critical to its clients' success, allowing them to accelerate innovation, refine product designs, and reduce time-to-market. For example, RPO's prototyping services provided critical support to a medical device manufacturer that needed to produce functional prototypes for testing their devices' safety and effectiveness. RPO's 3D printing and CNC machining capabilities enabled the manufacturer to produce accurate, high-quality prototypes quickly and efficiently, helping to reduce product development timelines and costs.Overall, Rapid Prototyping Options is revolutionizing the prototyping landscape, providing efficient, cost-effective prototyping services that enable companies to innovate at a rapid pace. With a focus on cutting-edge technology, precision, and customer service, RPO is committed to helping companies accelerate innovation, optimize product design, and bring products to market faster. Whether you're in aerospace, automotive, medical, or any other industry, RPO's prototyping services can help you take your innovation to the next level.
How to Build a Heavy CNC Milling Machine: 18 Steps with Pictures
Machine, Instructables, heavy CNC milling, epoxy granite, linear guides, building processCNC Milling Machine: A Comprehensive Guide to Building Your OwnBuilding a heavy-duty CNC milling machine is not a task for the faint-hearted. It requires a lot of different working steps and careful planning to ensure that you end up with a machine that can deliver precise and accurate results. In this blog post, we will take a closer look at the steps involved in building a big CNC machine with good milling performance, as well as the materials and equipment needed for the project.Step 1: Design and PlanningThe first step in building a CNC milling machine is to design and plan the machine. This involves deciding on the size of the machine, the materials to be used, the type of milling machine to be used, and the features and capabilities that the machine should have. It is important to have a clear understanding of the requirements before starting the project to avoid any costly mistakes down the line.Step 2: Building the MoldThe next step is to build a big and accurate mold for casting the epoxy granite. Epoxy granite is a popular material for building milling machines due to its sturdiness and vibration damping properties. The mold should be designed to ensure that it is rigid and can create a smooth surface finish. The casting process should be done carefully to avoid any air bubbles or voids that can cause inaccuracies in the finished cast.Step 3: Aligning the Linear GuidesThe linear guides play a crucial role in the accuracy and precision of the milling machine. They are responsible for guiding the cutting tool along a straight and consistent path. The linear guides should be aligned carefully to ensure that they are in perfect alignment with the cutting tool. This requires careful attention to detail and the use of precision measuring tools.Step 4: Building the Machine FrameThe frame of the milling machine should be built to be strong and rigid. The use of high-quality materials such as aluminum or steel is recommended. The frame should be designed with sufficient clearance to accommodate the linear guides and other machine components.Step 5: Assembling the MachineOnce all the components of the milling machine have been prepared, it is time to start assembling the machine. This requires careful attention to detail and a lot of patience. Each component should be installed carefully and securely to ensure that the machine is stable and can deliver precise and accurate results.ConclusionBuilding a heavy CNC milling machine is a challenging task that requires a lot of time and effort. However, with careful planning and attention to detail, it is possible to build a machine that can deliver precise and accurate results. The use of high-quality materials and precision measuring tools is essential to ensure that the machine is built to the required specifications. With the right approach, anyone can build their own CNC milling machine and take their machining capabilities to the next level.
What is Water-jet Technology and How Does it Work?
Water-jet technology has evolved significantly over the years, providing a versatile and efficient solution for a range of industrial applications. This technology involves the use of a high-pressure pump to create a stream of water that can be used to cut, clean, and shape different materials. Water-jet technology is fast becoming the go-to option for many employers in varied industries.The process of water-jet cutting starts by using a high-pressure pump that pumps water through a nozzle, which produces a super-fast stream of water that is directed onto the material to be cut. The water pressure can be adjusted to suit the type of material being cut, from soft materials like plastic, rubber, and foam to hard materials like metals, ceramics, and glass.One of the most significant benefits of water-jet technology is its ability to perform intricate cuts without creating heat-affected zones (HAZ). Thermal distortion, discoloration, and other undesirable effects are often seen when traditional cutting methods are used, like plasm cutting. However, water-jet cutting ensures material integrity through cold cutting, making it ideal for precision machining, intricate architectural designs, medical equipment, aerospace, and automotive parts.Traditional cutting methods such as laser and plasma can produce toxic fumes or debris that can be dangerous to the environment and human health. In contrast, water-jet cutting is eco-friendly and safe. The water used in this process can be recycled and reused, and the cutting operation produces no hazardous waste, allowing companies to reduce their environmental footprint considerably.Moreover, water-jet technology requires no special tooling, which means changing between different materials and designs is a breeze. This makes water-jet cutting an even more attractive option for manufacturers who need to switch between various production requirements quickly. Additionally, with advancements in technology, 5-axis cutting technology and robotics can be utilized, allowing greater flexibility and increased accuracy in cutting, ensuring more efficient and cost-effective production.The benefits of water-jet technology are not limited to cutting and shaping applications, as it has other uses too. Water-jet cleaning is another application of this technology. It involves the use of high-pressure water streams to remove dirt and grime from surfaces, making it an effective cleaning option for many businesses. Cleaning using a water-jet is particularly useful in the food and beverage industry, where sanitation is critical.Another advantage of using water-jet technology in cleaning is that it does not require any chemicals to aid the cleaning process. This, in turn, ensures that the cleaned surfaces are safe for human consumption, eliminating the need for chemical-based cleaning agents harmful to the environment and humans. The use of water-jet technology in cleaning can significantly reduce washing times and increase production efficiency, making it an ideal solution for many businesses.In conclusion, water-jet technology presents an innovative and eco-friendly solution for many manufacturing and cleaning applications. Its benefits are unrivaled when compared to traditional cutting and cleaning technologies. From increased production efficiency to reduced environmental footprint to the ability to perform intricate and precise cuts, water-jet technology has fast become a sought-after option for many businesses looking to improve their bottom line. Companies that have not yet implemented this technology in their operations are urged to give it a try and discover the numerous cost and time-saving benefits it can offer.
K-pop Group Member Involved in Physical Altercation Raises Concerns
NCT, the world-renowned punching machine manufacturer, has recently unveiled a new range of products, making a grand entry into the global market. Founded in 1970 and headquartered in Japan, the company has been one of the major players in the metal-forming industry for more than five decades. The company's huge success has been built on continuous innovation, research, and development of its products. With a keen focus on delivering the most advanced machinery to meet the needs of the modern world, NCT has been lauded for producing cutting-edge technology punching machines.The NCT punching machine's range is optimized for clients who seek to achieve high-precision sheet metal fabrication. Along with this, these machines offer superior speed and excellent durability, positioning them as a product of choice for clients in need of a reliable and quality-driven machine. The company's new line of punching machines is geared towards offering customized solutions that cater to both small-scale and large-scale industries. Clients can choose from various models, which have been specifically designed to cater to different needs, budgets, and production volumes.NCT's recent entry into the global marketplace has garnered much attention, owing to the company's longstanding reputation in the metal-forming machinery industry. The company's machines are known for their unparalleled precision and speed, combined with their ability to handle a wide variety of metals. The company's newest range of products is ideal for a wide range of punching applications used in several industries, including automobile, aerospace, electrical, and electronics.With the ever-growing demand for high-quality punching machines, NCT's entry into the global market promises to offer a much-needed boost to the metal-forming industry. The company's punching machines are designed to optimize time, effort, and cost, which are the most significant concerns of clients seeking these machines. The company's innovative and highly efficient punching machines set themselves apart from their competition, offering clients benefits such as increased productivity, higher precision, and lower cost per punch.The punching industry has evolved significantly over the years, and the demand for high-quality punching machines is higher than ever. NCT's large-scale entry into the market makes it evident that the company identifies the growing demand and is committed to providing the best solutions to clients worldwide. By offering a wide range of customized machinery, the company caters to clients of all sizes and industries, which ensures that clients can find the most suitable punching machine for their unique requirements.In conclusion, NCT's recent unveiling of their new range of punching machines marks the company's entry into the global market, and it is set to revolutionize the metal-forming industry. With superior speed, precision, and durability, NCT's machines offer unprecedented levels of productivity, providing clients with cost-effective solutions that optimize time and effort. The company's commitment to research and development has enabled it to deliver advanced and customized machinery, satisfying the needs of clients worldwide. With NCT, clients are guaranteed an unparalleled experience, and they can rest assured that they are investing in the best and most innovative punching machines on the market.
Precision Sheet Metal Brackets Made with Advanced Manufacturing Techniques
: A Comprehensive Guide for Your Manufacturing NeedsSheet metal brackets are an integral part of any manufacturing process that requires the use of metal sheets. In industries that require immense precision and accuracy, the bracket systems ensure that the metal’s shape and structure are maintained throughout the process. With the advancements in modern CNC manufacturing processes, the quality of these bracket systems has improved significantly. The use of advanced automation tools has led to more efficient and precise manufacturing methods.Sheet metal brackets are widely used in various industries such as Aerospace, Medical, Automotive, Construction, and Electronics. In construction, sheet metal brackets are used to provide support to the structural systems, and in electronics, they secure electronic components in place. With their versatility, sheet metal brackets are an essential component in several processes and products.Here is a comprehensive guide to sheet metal brackets for all your manufacturing needs:Types of Sheet Metal Brackets1. Angle Brackets: These are brackets that are bent to 90-degree angles to create perpendicular structural joints. They are commonly used in construction to ensure that the structures maintain their shape and stability.2. U Brackets: These brackets have a U-shaped cross-section that is used to create a mounting point for objects. They are commonly used to mount objects onto walls and other surfaces.3. L Brackets: These are brackets that are bent to form an L-shape. They are used in most applications requiring reinforcement to prevent structural deformation.4. Z Brackets: These are brackets that are bent to form a ‘Z’ shape. They are used in construction to provide additional support to the structural systems.5. T Brackets: These are brackets that are bent to form a T-shape. They are commonly used to attach objects onto walls or other surfaces.Applications of Sheet Metal BracketsSheet metal brackets are used in various applications, including:AerospaceIn the aerospace industry, brackets are used to mount different types of equipment and systems such as electronics, fuel systems, engines, and landing gear. The brackets are usually made from lightweight materials like aluminum to minimize weight.AutomotiveIn the automotive industry, brackets are essential in holding the structural components of the car together. They are also used in securing electrical components in place.ConstructionSheet metal brackets are used extensively in the construction industry for many different applications, such as securing wall studs and reinforcing roof structures.ElectronicsIn the electronics industry, sheet metal brackets are used to secure electronic components in place. They are also used in creating housing systems for electrical components.MedicalSheet metal brackets are used in medical equipment and devices to support and hold various pieces of equipment such as monitors, IV poles, and other medical components in place.Manufacturing ProcessWith advancements in modern CNC manufacturing processes, sheet metal brackets can be precisely and efficiently manufactured. The manufacturing process for sheet metal brackets includes the following stages:1. Material Selection: The sheets of metal used in creating the brackets are usually made from various metals such as Stainless Steel, Carbon Steel, and Aluminum, and copper.2. Laser Cutting: The sheets of metal are cut using laser cutting machines to create the individual brackets' required shapes and sizes.3. Bending: The cut sheet metal is then bent using precision bending machines to create the desired shape of the bracket.4. Welding or Fixing: After bending the metal, the bracket components are welded or fixed together to create a final product.5. Finishing: The finished brackets are sandblasted or painted to give it a final finish.ConclusionSheet metal brackets are a vital part of many manufacturing processes. They provide structural support, aid in mounting equipment and components, and ensure precise manufacturing processes. The modern CNC manufacturing processes have significantly improved the manufacturing process of sheet metal brackets, leading to more efficient, accurate, and high-quality products. If you need sheet metal brackets for your manufacturing processes, ensure that you engage a reputable and experienced manufacturer who can deliver the desired results.
Versatile 3-Axis Milling Machine for Diverse Applications
Milling is a versatile machining process that involves removing material from a workpiece using rotary cutters. It is a critical process in manufacturing, and it has wide-ranging applications. Whether creating new parts or repairing existing ones, milling precision parts is essential. To achieve precision, you need a reliable milling machine. One such machine is the 3-axis MILL E Series by GF Machining Solutions.The MILL E Series is a universal milling machine that sets standards in the industry. It has a high-precision spindle and advanced controller technology that provides accuracy and efficiency. The machine's design also allows for versatility, as it can handle various workpiece sizes and shapes. Additionally, the machine's user-friendly interface makes it easy to operate, reducing operator error and ensuring consistent precision.One of the most significant advantages of the MILL E Series is its ability to handle a range of materials. Whether you are machining aluminum, steel, or plastics, this milling machine can get the job done. It also has a flexible automatic tool changer, which can accommodate various tool types, and the machine's software can optimize cutting parameters for the specific material being machined. This ensures precision and quality in every job.In the VMC category, the MILL E Series sets the standard for milling precision parts. With its 3-axis design, it can produce complex, high-precision parts that meet tight tolerances. Moreover, the machine's high spindle speed and rigidity make it possible to maintain high precision even under heavy cutting loads. This capability makes the milling machine an excellent choice for challenging milling applications.In die and mold construction, the MILL E Series is also a valuable tool for smoothing surface finishes. When using a round-head cutter, the milling machine can deliver precise and polished surfaces, making it ideal for finishing workpieces. This capability makes the milling machine an essential tool for injection mold manufacturing, which requires smooth and polished finishes for the final product.ConclusionMilling precision parts is essential in the manufacturing industry, and having a reliable milling machine is critical in achieving precision and efficiency. GF Machining Solutions' MILL E Series offers versatile applications, high-performance, and precision in milling. Its 3-axis design, high spindle speed, and tool-changing capabilities make it ideal for milling precision parts of varying shapes, sizes, and materials. It also allows for excellent surface finishes, making it an invaluable tool in die and mold construction. So, if you are in the market for a milling machine that can deliver precision, efficiency, and versatility, consider the MILL E Series from GF Machining Solutions.
China-Based Manufacturer Offers Precision CNC Machined Parts
Wintec Precision Machining Co., Ltd: Your One-Stop Solution for CNC Precision Machined ComponentsWintec Precision Machining Co., Ltd is a leading OEM/ODM manufacturer of CNC precision machined components in China. With years of experience in the industry, Wintec has emerged as a reliable and trustworthy machining partner for businesses across the globe. Our team of highly skilled engineers and technicians, along with state-of-the-art infrastructure and advanced technology, enable us to deliver high-quality machined products that are second to none.At Wintec, we operate with a customer-first approach where customer satisfaction is our top priority. We work closely with our clients to understand their specific requirements and offer customized solutions that meet their needs. We have an extensive range of machining capabilities, including CNC turning, CNC milling, and CNC grinding, to provide accurate and precise parts that meet our client's specifications.Our CNC precision machined components are made using strict quality control measures that ensure superior product performance and reliability. We use only the highest quality raw materials that are sourced from reputable suppliers to ensure that our products meet stringent industry standards. Our commitment to quality is demonstrated by our ISO 9001:2015 certification, a testament that we deliver quality products consistently.At Wintec, we offer a broad range of CNC precision machined components, including shafts, sleeves, gears, housings, and more. We specialize in producing quality parts that cater to a wide range of industries, including the automotive, aerospace, medical, and energy sectors. Our machining capabilities allow us to create parts with intricate designs, intricate surface finishes, and tight tolerances that meet our client's exacting requirements.As a China-based manufacturer, Wintec offers our clients a cost-effective solution that does not compromise on quality. We have an extensive network of suppliers that allows us to source the best raw materials at a competitive price, passing on the savings to our clients. Our commitment to delivering cost-effective solutions makes us an attractive partner for businesses looking to reduce their production costs without sacrificing quality.In conclusion, Wintec Precision Machining Co., Ltd is a reliable partner for businesses in need of CNC precision machined components. We offer quality products, customized solutions, and cost-effective services that meet our clients' requirements. Our commitment to customer satisfaction, quality, and integrity makes us the ideal choice for your machining needs. Contact us today to learn more about our products and services.
Chinese National Arrested for Smuggling $300K Worth of Endangered Species Parts
[INTRODUCTION]In a recent development, a major player in the tech industry has announced groundbreaking innovations that are set to revolutionize the way we interact with our devices. This company, which has a long-standing reputation for pushing the boundaries of technology, is poised to disrupt the market with its latest advancements. These cutting-edge solutions promise to enhance user experiences and pave the way for a more connected and intuitive future.[PARAGRAPH 1]With a focus on improving accessibility and convenience, the company has unveiled a range of new products designed to cater to the evolving needs of consumers. One of the most notable introductions is a versatile smart device that combines functionality, aesthetics, and state-of-the-art technology. This multi-purpose gadget, which has been closely developed in response to user feedback and demands, aims to streamline daily activities and simplify the digital experience.[PARAGRAPH 2]One of the key features of this innovative product is its seamless integration with various ecosystems, allowing users to effortlessly connect and control their smart devices and services. By consolidating these capabilities into a single hub, the company aims to offer an all-encompassing solution that eliminates compatibility issues and offers a unified user interface. This holistic approach allows individuals to effortlessly manage their digital lives, from controlling smart home devices to organizing schedules and accessing entertainment options, all with a few simple taps.[PARAGRAPH 3]Moreover, this technology giant has made significant advancements in the field of artificial intelligence (AI), with the introduction of an advanced virtual assistant. Leveraging AI algorithms, this intelligent assistant is capable of understanding natural language, recognizing voices, and adapting to individual preferences. By utilizing machine learning, the assistant becomes increasingly adept at providing personalized recommendations, answering queries, and anticipating user needs. This groundbreaking development brings us one step closer to a future where technology seamlessly integrates into our lives and assists us in our day-to-day tasks.[PARAGRAPH 4]Understanding the importance of privacy and security, the company has also focused on fortifying its devices against potential risks and threats. By implementing robust encryption algorithms and stringent data protection measures, users can rest assured that their personal information remains secure. Additionally, comprehensive user controls have been embedded within the system, allowing individuals to fine-tune their privacy settings and determine the extent to which their data is shared with external services.[PARAGRAPH 5]As part of its commitment to sustainability and environmental responsibility, this technology leader has made significant strides in minimizing its carbon footprint. With a focus on developing energy-efficient devices and employing eco-friendly manufacturing processes, the company aims to contribute towards building a greener future. By prioritizing the use of sustainable materials and adopting recycling initiatives, it aligns with the growing demand for environmentally conscious practices.[PARAGRAPH 6]The impact of these revolutionary developments is expected to extend beyond the consumer market. Industries such as healthcare, transportation, and education are also poised to benefit from these technological breakthroughs. With the ability to seamlessly integrate into existing infrastructure, these advancements have the potential to transform various sectors, enabling greater efficiency, connectivity, and innovation.[CONCLUSION]In conclusion, the recent news from this prominent technology company represents a significant leap forward in the realm of smart devices and AI technology. With a focus on enhancing user experiences and solving real-world problems, the innovations announced are set to redefine the way we interact with technology. As this company continues to push boundaries and drive innovation, it is clear that the future holds exciting possibilities for technology enthusiasts and consumers worldwide.