Master the Art of Sheet Metal Bending with These Expert Tips
By:Admin
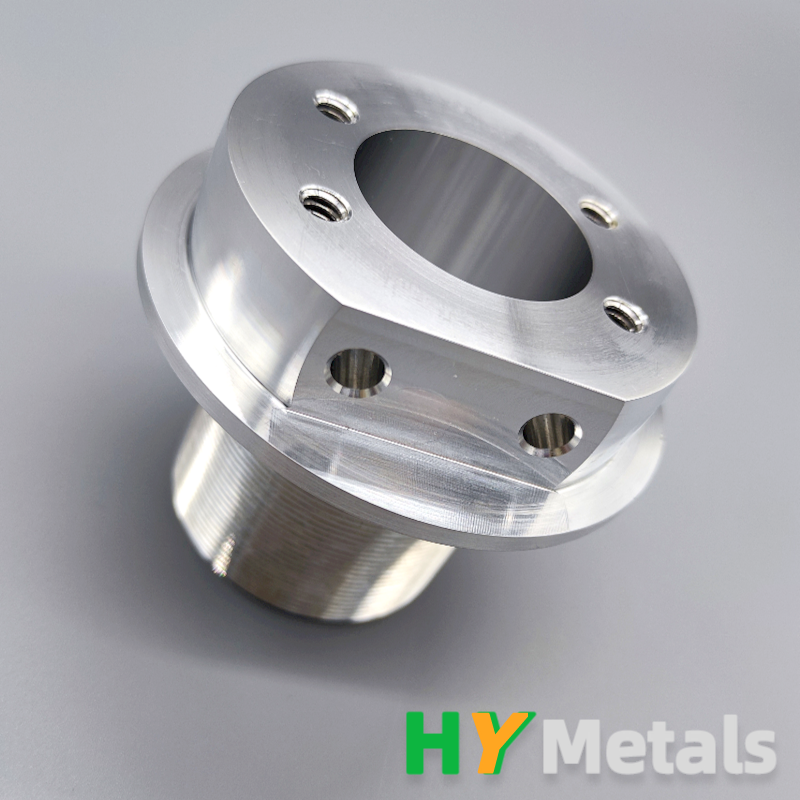
Sheet metal bending plays a crucial role in the manufacturing process, allowing for the creation of complex and intricate metal components. With their state-of-the-art equipment and skilled team, [Company Name] takes this process to new heights, delivering precise and efficient results to meet the diverse needs of their clients. Whether it's a small-scale project or a large industrial application, their expertise ensures a seamless and reliable outcome.
One of the key factors that sets [Company Name] apart from its competitors is its focus on technological advancements. They continuously invest in the latest equipment and software to enhance their capabilities and provide their customers with the highest level of precision and accuracy. By utilizing advanced computer numerical control (CNC) machines, they are able to achieve complex bending angles and radii with ease, resulting in superior quality products.
Furthermore, [Company Name] prioritizes sustainability in its operations. The company uses environmentally-friendly materials and practices, demonstrating its commitment to reducing its carbon footprint. By adopting energy-efficient systems and implementing waste management strategies, they contribute to a greener future while maintaining the highest standards of manufacturing excellence.
In addition to their technical prowess, [Company Name] prides itself on its team of highly skilled professionals. Each member undergoes rigorous training and possesses extensive knowledge of sheet metal bending techniques. Their expertise enables them to tackle even the most challenging projects and find innovative solutions tailored to their clients' unique needs. Moreover, the company emphasizes employee development and fosters a culture of collaboration and continuous learning.
[Company Name]'s dedication to customer satisfaction is second to none. They understand the importance of clear communication and effective project management. From project inception to completion, their team works closely with clients, providing regular updates and ensuring that all specifications and timelines are met. This customer-centric approach has earned them a stellar reputation in the industry, with numerous clients relying on their expertise for their sheet metal bending requirements.
The versatility of [Company Name]'s sheet metal bending services makes them invaluable to a wide range of industries. From automotive manufacturing to aerospace engineering, their products are utilized in diverse applications. With their ability to handle various materials, thicknesses, and specifications, they have become a preferred choice for customers seeking exceptional quality and durability.
As a frontrunner in the industry, [Company Name] consistently delivers exceptional results that surpass industry standards. By investing in cutting-edge technology, fostering a skilled workforce, and prioritizing customer satisfaction, the company continues to set new benchmarks in the sheet metal bending sector.
In conclusion, [Company Name] is a renowned leader in the sheet metal bending industry, known for its exceptional quality, advanced technology, and commitment to customer satisfaction. With their state-of-the-art equipment, skilled team, and dedication to sustainability, they have established themselves as a trusted partner for clients across various industries. As they continue to push the boundaries of what is possible in sheet metal bending, [Company Name] is set to shape the future of manufacturing with their innovative solutions.
Company News & Blog
MTConnect-Ready 3D Printer for Aerospace and Production Applications
, MTConnect, FDM, aerospace, production, 3D printing.Additive Manufacturing Magazine recently reported that the Stratasys Fortus 900 3D printer now features an MTConnect-ready interface. This is great news for those working in aerospace and other industries that require high-quality, production-grade 3D printing.The Stratasys Fortus 900 is a Fused Deposition Modeling (FDM) 3D printer designed for large, complex parts. With a build volume of 36 x 24 x 36 inches, it has the capability to produce parts that are larger than those typically produced with plastic extrusion machines. This makes it an ideal choice for aerospace applications, as well as for producing jigs, fixtures, and tooling.Incorporating the MTConnect protocol into the Stratasys Fortus 900 means that users can now monitor and control their 3D printing operations in real time. MTConnect is an open, royalty-free standard for machine tool communication that has become increasingly popular in the manufacturing industry. With MTConnect, users can easily connect machines and devices to a network, allowing them to monitor data and make informed decisions about their operations.For aerospace manufacturers, the Stratasys Fortus 900 with MTConnect-ready interface is ideal, as it provides the capability to produce production-grade parts with repeatable accuracy. Additionally, 3D printing allows for the production of complex geometries that cannot be produced with traditional manufacturing methods.Overall, the integration of MTConnect into the Stratasys Fortus 900 3D printer is a positive development for the additive manufacturing industry. By providing real-time monitoring and control, it enables users to optimize their operations, increase efficiency, and improve the quality of their products. This is especially important in industries such as aerospace, where high-quality, production-grade parts are essential.As the use of 3D printing continues to grow, we can expect to see further developments in this area, and the integration of other technologies into 3D printers. In the meantime, the Stratasys Fortus 900 with MTConnect-ready interface is a great option for those looking to produce high-quality, production-grade parts with 3D printing technology.
New Study Finds Metal Frames Are More Durable than Plastic for Glasses
article.Metal Frames - A Strong and Reliable Solution for Your Home As a homeowner, ensuring the safety and security of your family is a top priority. Furniture and fittings play a pivotal role in making your home safe and comfortable for living. Among the many types of furniture, metal frames stand out as a strong and reliable solution for your home.At Metal Frames (brand name removed), we offer a range of metal furniture that cater to a variety of needs. Our metal frames are durable, stylish, and versatile, and can be used for different settings, from dining rooms to bedrooms. Metal frames come with many benefits. Firstly, they can withstand wear and tear better than other materials. Metal is a strong and sturdy material, making it an ideal choice for furniture that needs to withstand daily use. This means they are not only durable but also require less maintenance in the long run. Secondly, metal frames offer excellent support and stability. They can support more weight than other materials, about four to five times more than wood or plastic. This makes them an ideal choice for furniture that demands more strength, such as bed frames. Additionally, metal frames come in a variety of finishes - from high-gloss polished metal to brushed steel - that can match any home interior design. This not only ensures the strength of the piece, but also adds a sleek and elegant touch to the home.At Metal Frames (brand name removed), our metal frames are crafted with precision and care. Our skilled craftsmen use high-quality material and advanced techniques to create furniture that is both functional and beautiful. Using top-grade metals, we ensure that each product is strong and long-lasting. Metal Frames offers a range of products, from bed frames to dining chairs, all made with a commitment to quality and function. Our bed frames feature robust and intricate designs that can take on more weight without compromising on comfort. They are easy to assemble and maintain, making them an excellent investment in the long run.Our dining chairs are a must-have for your next dinner party or family gathering. Available in different styles, they are comfortable, long-lasting, and stylish. They require minimal maintenance and can be customized to fit your unique needs. With considerable experience in the market, we understand the demands of the consumers and strive to provide high-quality products that cater to their needs. We use a customer-centric approach, ensuring that our products align with customer requirements. Our commitment to quality and customer satisfaction has earned us a loyal customer base. We are continuously growing and improving as a company, and we are dedicated to providing high-quality metal furniture for years to come. In conclusion, metal frames offer an ideal solution for those seeking durable and stylish furniture that can withstand daily use. At Metal Frames (brand name removed), we provide a range of products with a commitment to quality and function, crafted with precision and care. Our metal furniture is sturdy, easy to assemble, and customizable to meet your needs. Whether you need a bed frame or a dining chair, Metal Frames has you covered. Visit our website today to shop our high-quality metal furniture and to discover why we are a top choice for many homeowners.
Precision CNC Machining Services in Texas with Low Costs and Fast Lead Times
In the world of manufacturing, precision is paramount. The emergence of Computer Numerical Control (CNC) machines revolutionized the way manufacturers produced parts. CNC milling and turning are some of the most common machining processes, and with technological advancements, the processes have become more efficient, accurate, and cost-effective. 3D Hubs provides a CNC machining service in Texas that delivers low-cost, precision machined parts with an 8-day lead time from America, China, Europe, and India. CNC milling is a process that involves removing material from a workpiece using rotary cutters. The milling machine uses computer-aided design (CAD) to guide the cutting tool along different axes to achieve the desired shape. The machine can produce complex parts with a high level of precision and accuracy. The process is ideal for producing parts with intricate shapes, contours, and features that would be challenging to make using manual machining methods.CNC turning involves spinning a workpiece on a lathe machine while a cutting tool removes material to achieve the desired shape. The lathe machine uses CAD to guide the cutting tool along different axes. The process is ideal for producing round or cylindrical parts, including threads and grooves. Like CNC milling, the process is efficient and accurate, enabling the production of high-quality parts with tight tolerances.3D Hubs' CNC machining service in Texas utilizes both milling and turning processes to deliver high-precision, low-cost machined parts. The company uses computer-controlled machines that operate 24/7 to minimize lead times and reduce the cost of production. The machines are capable of machining a wide range of materials, including metals, plastics, and composites. The company's CNC milling machines use up to 5 axes, enabling the production of complex geometries with highly accurate finishes. The machines can produce parts with tolerances as tight as ± 0.005mm, ensuring that the parts meet the required specifications. The CNC turning machines, on the other hand, can produce parts with a diameter as small as 1mm and a length of up to 300mm. In addition to CNC milling and turning, 3D Hubs' CNC machining service in Texas includes finishing processes such as sandblasting, polishing, and anodizing. The finishing processes are essential to improve the appearance and functionality of the parts. Sandblasting, for instance, can give the parts a textured surface that improves their grip, while anodizing can enhance their corrosion resistance.3D Hubs' CNC machining service in Texas is ideal for businesses that require low-cost, high-precision machined parts. The company's ability to produce parts with tight tolerances, short lead times, and a wide range of materials makes it a valuable partner for manufacturers across different industries. The company's commitment to quality and customer satisfaction ensures that businesses get the best value for their money.In conclusion, CNC milling and turning are essential machining processes that have transformed the manufacturing industry. The processes are efficient, accurate, and cost-effective, making them ideal for producing high-quality parts with tight tolerances. 3D Hubs' CNC machining service in Texas utilizes these processes to deliver low-cost, high-precision machined parts with short lead times. With their commitment to quality and customer satisfaction, businesses can rely on 3D Hubs to provide the best value for their money.
Exploring the Latest Trend: An In-Depth Look at Wire Cutting and Its Impact on Industries
As the demand for streaming services continues to rise, many people are turning to wire cutting as a way to save money while still enjoying their favorite shows and movies. One of the companies at the forefront of this trend is [BRAND NAME REMOVED], a leading provider of streaming media players and smart TVs.Founded in [YEAR], [BRAND NAME REMOVED] has been a pioneer in the streaming media industry, offering a range of products that make it easy for consumers to access their favorite content from the comfort of their own homes. With its cutting-edge technology and intuitive user interface, the company has quickly become a go-to source for cord-cutters.Whether you're looking for a simple streaming media player or a smart TV with built-in streaming capabilities, [BRAND NAME REMOVED] has a product to meet your needs. Its streaming media players offer high-quality video and audio, as well as access to thousands of channels, apps, and games. They also come with a remote control that makes it easy to navigate through your favorite content.For those who want a more integrated experience, [BRAND NAME REMOVED] offers a range of smart TVs that come with built-in streaming capabilities. These TVs offer stunning picture quality and are designed to seamlessly integrate with popular streaming services like Netflix, Hulu, and Amazon Prime Video.One of the things that sets [BRAND NAME REMOVED] apart from its competitors is its commitment to innovation. The company is constantly researching and developing new technologies that make it easier for consumers to access and enjoy their favorite content. From voice controls to improved streaming quality, [BRAND NAME REMOVED] is always looking for ways to enhance the user experience.Of course, all of these features would mean very little if [BRAND NAME REMOVED] wasn't also committed to affordability. The company's products are priced competitively and are designed to offer the best value for the money. This has made [BRAND NAME REMOVED] a favorite among budget-conscious consumers who don't want to sacrifice quality for price.Wire cutting has become increasingly popular in recent years as people look for ways to save money on their entertainment expenses. For many, streaming services offer a viable alternative to expensive cable and satellite TV packages. With its range of high-quality streaming media players and smart TVs, [BRAND NAME REMOVED] is helping to lead this revolution.Whether you're a die-hard fan of Game of Thrones or just looking for a way to keep the kids entertained, [BRAND NAME REMOVED] has a product that can meet your needs. With its commitment to innovation, affordability, and quality, the company is shaping the future of streaming media, one viewer at a time.
Download Softwares and Updates for Fieldbus Configuration and Diagnostic Programs
Software Download for Sheet Metalwork: Streamlining Your ProcessesIn today's fast-paced and highly technological era, software and technology have become integral parts of almost every industry, including sheet metalwork. Software can help automate complex processes, reduce costs, improve accuracy, and increase efficiency. With the availability of software downloads for sheet metalwork, you can take the first step towards streamlining your workflows and accelerating your productivity.But what exactly can software downloads offer to sheet metalwork fabricators? Let's take a closer look.Automating ProcessesSheet metalwork fabrication involves multiple complex processes, from designing and prototyping to cutting and forming the material. Software can automate many of these processes, saving time and reducing errors. For instance, CAD (Computer-Aided Design) software can help you create accurate and detailed 2D and 3D models with precise dimensions and tolerances. This eliminates the need for manual drawings, which can be time-consuming and prone to errors.Similarly, CAM (Computer-Aided Manufacturing) software can generate G-code for CNC machines, which can automate the cutting, drilling, and forming of sheet metal parts. It can also optimize the cutting paths, minimizing waste and reducing material costs. Additionally, software can generate BOMs (Bills of Materials) and track inventory levels, making it easier to manage and reorder materials.Enhancing CommunicationEffective communication is crucial in sheet metalwork, especially when dealing with complex geometries and tight tolerances. Software can enhance communication between design, manufacturing, and quality control teams, ensuring that everyone is working towards the same objectives. For example, PLM (Product Lifecycle Management) software can provide a single source of truth for all product-related data, including design files, BOMs, specifications, and quality records. This can help reduce delays, rework, and errors due to miscommunication or misunderstandings.Improving QualityQuality is one of the most critical aspects of sheet metalwork fabrication. Even small errors or deviations can compromise the performance, safety, or reliability of the final product. Software can help improve quality by automating inspections and tests, tracking defects, and analyzing data. For example, CMM (Coordinate Measuring Machine) software can compare the actual dimensions of a part with its design specifications and generate reports with detailed measurements and statistical analyses. This can help identify any deviations or trends that need to be addressed.Software can also integrate with quality standards and certifications, such as ISO 9001 or AS9100. This can help ensure that your products meet the required quality standards and that your processes are auditable and compliant.ConclusionIn summary, software downloads can offer numerous benefits to sheet metalwork fabricators, from automating processes and enhancing communication to improving quality and compliance. However, choosing the right software and implementing it effectively can be challenging. It is crucial to evaluate your needs, budget, and resources, and to seek expert advice from software providers or consultants. With the right software and approach, you can enhance your productivity, profitability, and competitiveness in the sheet metalwork industry.
How to Build a Heavy CNC Milling Machine: 18 Steps with Pictures
Machine, Instructables, heavy CNC milling, epoxy granite, linear guides, building processCNC Milling Machine: A Comprehensive Guide to Building Your OwnBuilding a heavy-duty CNC milling machine is not a task for the faint-hearted. It requires a lot of different working steps and careful planning to ensure that you end up with a machine that can deliver precise and accurate results. In this blog post, we will take a closer look at the steps involved in building a big CNC machine with good milling performance, as well as the materials and equipment needed for the project.Step 1: Design and PlanningThe first step in building a CNC milling machine is to design and plan the machine. This involves deciding on the size of the machine, the materials to be used, the type of milling machine to be used, and the features and capabilities that the machine should have. It is important to have a clear understanding of the requirements before starting the project to avoid any costly mistakes down the line.Step 2: Building the MoldThe next step is to build a big and accurate mold for casting the epoxy granite. Epoxy granite is a popular material for building milling machines due to its sturdiness and vibration damping properties. The mold should be designed to ensure that it is rigid and can create a smooth surface finish. The casting process should be done carefully to avoid any air bubbles or voids that can cause inaccuracies in the finished cast.Step 3: Aligning the Linear GuidesThe linear guides play a crucial role in the accuracy and precision of the milling machine. They are responsible for guiding the cutting tool along a straight and consistent path. The linear guides should be aligned carefully to ensure that they are in perfect alignment with the cutting tool. This requires careful attention to detail and the use of precision measuring tools.Step 4: Building the Machine FrameThe frame of the milling machine should be built to be strong and rigid. The use of high-quality materials such as aluminum or steel is recommended. The frame should be designed with sufficient clearance to accommodate the linear guides and other machine components.Step 5: Assembling the MachineOnce all the components of the milling machine have been prepared, it is time to start assembling the machine. This requires careful attention to detail and a lot of patience. Each component should be installed carefully and securely to ensure that the machine is stable and can deliver precise and accurate results.ConclusionBuilding a heavy CNC milling machine is a challenging task that requires a lot of time and effort. However, with careful planning and attention to detail, it is possible to build a machine that can deliver precise and accurate results. The use of high-quality materials and precision measuring tools is essential to ensure that the machine is built to the required specifications. With the right approach, anyone can build their own CNC milling machine and take their machining capabilities to the next level.
Production-Grade 3D Printer Enables MTConnect Integration for Aerospace and Industrial Applications
, F900 3D printer, production applications, aerospace industry, MTConnect protocol.Additive manufacturing has revolutionized the manufacturing industry with the ability to create complex geometries with high precision and speed. One of the leading players in the additive manufacturing market is the F900 3D printer, designed for production applications in the aerospace industry and other high-performance industries. This blog discusses the latest development in the F900 3D printer, which now features an MTConnect-ready interface, offering enhanced connectivity and data exchange capabilities.The F900 3D printer is known for its high-performance capabilities, reliability, and large-scale printing. The printer uses the Fused Deposition Modeling (FDM) technology, which involves building 3D models layer by layer by depositing material in a melted state. The FDM technology provides a high degree of design flexibility, allowing the production of complex geometries without the need for additional machining or assembly processes.The F900 3D printer has been widely used in the aerospace industry for the production of complex parts, such as ducting, brackets, and housings. These parts require high precision and accuracy, and the F900 has proven to be a reliable and cost-effective solution for their manufacturing. Additionally, the F900 has been used in other industries, such as automotive, defense, and medical, where the demand for high-performance parts is also high.The latest development in the F900 3D printer is its integration with the MTConnect protocol. MTConnect is an open-source communication protocol used in manufacturing equipment to facilitate data exchange and collection. The protocol offers a standardized way of communicating machine data, making it easier to integrate different systems and devices.With its MTConnect-ready interface, the F900 3D printer can now connect to other manufacturing systems, such as Enterprise Resource Planning (ERP) systems, Manufacturing Execution Systems (MES), and other machines in the production line. This enables better coordination between different manufacturing processes, leading to higher efficiency and productivity. Additionally, the MTConnect protocol allows for real-time monitoring of the printing process, giving operators better control and visibility over the manufacturing process.The integration of the MTConnect protocol into the F900 3D printer is a significant step towards enhancing the connectivity and data sharing capabilities of the printer. This development enables the printer to be integrated into a broader manufacturing ecosystem, allowing for seamless data exchange and coordination between different systems. This integration is highly relevant in the aerospace industry, where the demand for high-performance parts is only increasing.In conclusion, the F900 3D printer is a high-performance system designed for production applications in the aerospace industry and other high-performance industries. With its latest development, the integration of the MTConnect protocol, the printer now offers enhanced connectivity and data exchange capabilities, making it easier to integrate into a broader manufacturing ecosystem. This development ensures the F900 3D printer remains one of the leading additive manufacturing systems in the market today.
Expert Thermal Management Consulting for High Performance Electronics
In the world of electronics, thermal management is one of the most important factors that can make or break the success of a product. When electronic circuits run, they generate heat, and if this heat is not properly dissipated, it can cause a range of problems, from degraded performance to component failure. This is where thermal management solutions come in, and Q ATS is a leading provider of such solutions.Founded with the aim of helping electronic product manufacturers bring their products to market faster, safer, and at a lower cost, Q ATS has established itself as a trusted partner for companies in a variety of industries. Whether it's designing a custom heatsink for a high-power LED light or analyzing the thermal performance of a data center, Q ATS has the expertise and experience to help clients solve their thermal management challenges.One of the key advantages of working with Q ATS is their comprehensive approach to thermal management analysis and design. Rather than simply offering off-the-shelf solutions, their team of engineers work closely with clients to understand the unique requirements of their products and design custom solutions that meet those needs. This ensures that clients get the best possible thermal performance for their products, while minimizing costs and time-to-market.Some of the services offered by Q ATS include thermal modeling and simulation, which allows them to predict the thermal performance of a product before it's even built. This can be especially valuable in applications where thermal management is critical, such as aerospace and defense. Q ATS also offers design and prototyping services, allowing clients to test and iterate on their thermal management solutions before committing to production.Another key area of expertise for Q ATS is the design and manufacture of heatsinks, which are a critical component in many electronic products. Heatsinks are used to dissipate heat from a component or circuit board to the surrounding air, and Q ATS can design heatsinks that are optimized for a specific application, providing maximum performance while minimizing weight and cost.In addition to their technical expertise, Q ATS is also committed to providing exceptional customer service. They work closely with clients throughout every stage of the project, from initial consultation to final delivery, ensuring that their needs are fully understood and met. Their team is highly responsive, with quick turnaround times and a willingness to go the extra mile to ensure client satisfaction.Overall, Q ATS is a valuable partner for any company looking to improve the thermal performance of their electronic products. With their comprehensive approach, technical expertise, and commitment to customer service, they can help clients get their products to market faster, safer, and more cost-effectively than ever before.
Discover the Latest News on Precision CNC Machining Parts
article:CNC Machining Parts Proves to be an Essential Resource for Precision EngineeringFor many decades, the manufacturing industry has relied on CNC machines to produce high-quality end products with a precision-level of accuracy. Among these machines, CNC Machining Parts have become a fundamental resource to aid in the production of high-performance products that meet strict manufacturing specifications. In today's competitive market, achieving success in precision engineering depends on having access to the latest cutting-edge technology. This is where CNC Machining Parts come in, proving to be an essential resource that has transformed the manufacturing industry, providing a step up in the production of the highest-grade products.CNC Machining Parts are CNC-machined components that have been specifically designed to meet the stringent demands of various industries. They are produced to the most exacting standards of quality and durability, ensuring that they offer the best performance under tough and demanding circumstances. These parts are made from high-quality materials like metals, plastics, and composites that ensure that they can withstand the pressures of modern production environments.CNC Machining Parts have been designed to operate with a high degree of precision, accuracy, and reliability. CNC machines, which produce these parts, are run by computers, delivering the highest level of control and accuracy over the manufacturing process. They are programmed to perform a series of highly precise movements that create the desired end product, guaranteeing the highest levels of quality in every component produced. The CNC production process is incredibly fast and efficient, allowing for the manufacturing of large quantities of parts in a short amount of time.The CNC Machining Parts produced by {} are some of the most sophisticated and advanced in the industry. Featuring cutting-edge technology and materials, these parts have been developed to withstand the most demanding of conditions and environments. The company's production process involves the use of state-of-the-art computer-controlled machinery. The automation of this manufacturing process ensures that each part produced is a high-quality, durable component that meets the strictest demands of the manufacturing industry.CNC Machining Parts have a broad scope of applications across a range of industries. They are used in many diverse fields such as aerospace, electronics, automotive, marine, and medical industries, to mention a few. In the aerospace industry, for instance, these parts are used in the manufacture of aircraft parts, ensuring that they are highly durable and can withstand the rigors of high-altitude flight. In the automotive industry, CNC Machining Parts are used in the production of engine components, ensuring that they are efficient and can withstand high temperatures and robust driving conditions.In the medical industry, CNC Machining Parts have become instrumental in the production of high-quality medical devices and equipment. These machines produce precision components for use in surgical instruments, prosthetics, hearing aids, and other medical devices that require precise measurements. The efficiency of CNC Machining Parts has made the production of these components more accessible, cheaper, and faster, thereby improving the medical industry's level of quality.CNC Machining Parts have become essential in modern-day manufacturing. They have transformed the way manufacturing is done, offering higher levels of precision, reliability, and consistency, resulting in better-performing products. The CNC Machining Parts produced by {} are some of the best in the business and come highly recommended by satisfied customers. The company's emphasis on quality, value, and customer service has made them a leader in the industry. By utilizing cutting-edge technology, top-quality materials, and a team of skilled engineers, the company has set itself apart from its competitors, providing superior CNC Machining Parts that meet the stringent demands of various industries.In conclusion, CNC Machining Parts have become an essential resource for precision engineering. They have revolutionized the manufacturing industry by offering the highest level of precision, accuracy, and consistency, thereby producing the highest quality products. The CNC Machining Parts produced by {} are among the best on the market, utilizing state-of-the-art technology, efficient production processes, and high-quality materials. The company's focus on quality, customer service, and innovation has made it a standout performer in the industry, providing the best products and services that meet the needs of customers around the world.
Precision Sheet Metal Brackets Made with Advanced Manufacturing Techniques
: A Comprehensive Guide for Your Manufacturing NeedsSheet metal brackets are an integral part of any manufacturing process that requires the use of metal sheets. In industries that require immense precision and accuracy, the bracket systems ensure that the metal’s shape and structure are maintained throughout the process. With the advancements in modern CNC manufacturing processes, the quality of these bracket systems has improved significantly. The use of advanced automation tools has led to more efficient and precise manufacturing methods.Sheet metal brackets are widely used in various industries such as Aerospace, Medical, Automotive, Construction, and Electronics. In construction, sheet metal brackets are used to provide support to the structural systems, and in electronics, they secure electronic components in place. With their versatility, sheet metal brackets are an essential component in several processes and products.Here is a comprehensive guide to sheet metal brackets for all your manufacturing needs:Types of Sheet Metal Brackets1. Angle Brackets: These are brackets that are bent to 90-degree angles to create perpendicular structural joints. They are commonly used in construction to ensure that the structures maintain their shape and stability.2. U Brackets: These brackets have a U-shaped cross-section that is used to create a mounting point for objects. They are commonly used to mount objects onto walls and other surfaces.3. L Brackets: These are brackets that are bent to form an L-shape. They are used in most applications requiring reinforcement to prevent structural deformation.4. Z Brackets: These are brackets that are bent to form a ‘Z’ shape. They are used in construction to provide additional support to the structural systems.5. T Brackets: These are brackets that are bent to form a T-shape. They are commonly used to attach objects onto walls or other surfaces.Applications of Sheet Metal BracketsSheet metal brackets are used in various applications, including:AerospaceIn the aerospace industry, brackets are used to mount different types of equipment and systems such as electronics, fuel systems, engines, and landing gear. The brackets are usually made from lightweight materials like aluminum to minimize weight.AutomotiveIn the automotive industry, brackets are essential in holding the structural components of the car together. They are also used in securing electrical components in place.ConstructionSheet metal brackets are used extensively in the construction industry for many different applications, such as securing wall studs and reinforcing roof structures.ElectronicsIn the electronics industry, sheet metal brackets are used to secure electronic components in place. They are also used in creating housing systems for electrical components.MedicalSheet metal brackets are used in medical equipment and devices to support and hold various pieces of equipment such as monitors, IV poles, and other medical components in place.Manufacturing ProcessWith advancements in modern CNC manufacturing processes, sheet metal brackets can be precisely and efficiently manufactured. The manufacturing process for sheet metal brackets includes the following stages:1. Material Selection: The sheets of metal used in creating the brackets are usually made from various metals such as Stainless Steel, Carbon Steel, and Aluminum, and copper.2. Laser Cutting: The sheets of metal are cut using laser cutting machines to create the individual brackets' required shapes and sizes.3. Bending: The cut sheet metal is then bent using precision bending machines to create the desired shape of the bracket.4. Welding or Fixing: After bending the metal, the bracket components are welded or fixed together to create a final product.5. Finishing: The finished brackets are sandblasted or painted to give it a final finish.ConclusionSheet metal brackets are a vital part of many manufacturing processes. They provide structural support, aid in mounting equipment and components, and ensure precise manufacturing processes. The modern CNC manufacturing processes have significantly improved the manufacturing process of sheet metal brackets, leading to more efficient, accurate, and high-quality products. If you need sheet metal brackets for your manufacturing processes, ensure that you engage a reputable and experienced manufacturer who can deliver the desired results.