Exploring the Tremendous Benefits of Fast Prototyping in Modern Industries
By:Admin
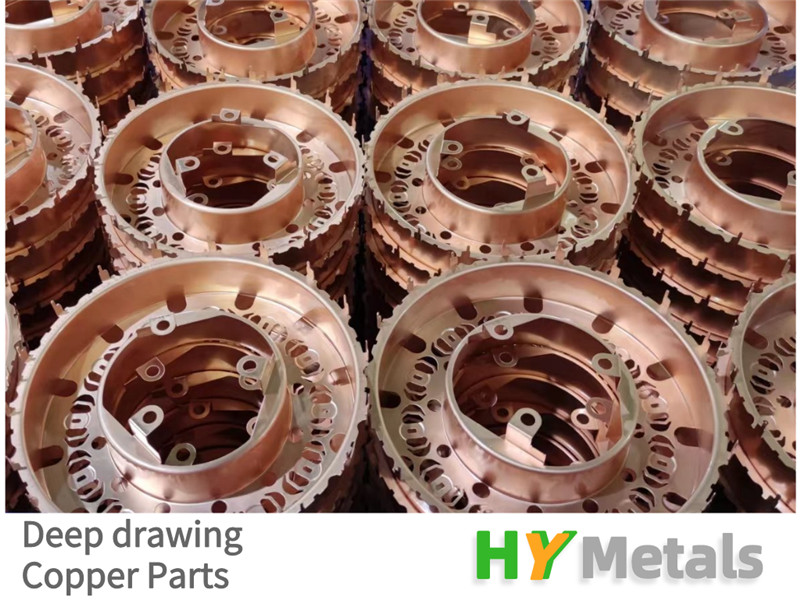
Subtitle: Pioneering the Future of Product Development and Innovation
Date: [Date]
[City], [State] - [Company Name], a renowned leader in the field of prototyping and product development, has introduced an innovative and ground-breaking technology that is set to revolutionize the industry. The company is changing the game with its cutting-edge Fast Prototyping, a process that enables businesses to bring their ideas to life quicker and more efficiently than ever before.
With a knack for pushing boundaries and an unwavering commitment to excellence, [Company Name] has always been at the forefront of technological advancements. The introduction of their Fast Prototyping technology is yet another testament to their status as industry leaders.
Fast Prototyping is a game-changer in the product development world, allowing businesses to rapidly iterate and refine their designs in order to accelerate the time-to-market. This technology enables companies to transform their concept into a physical prototype within a matter of days, significantly reducing the time and cost associated with traditional prototyping methods.
The key to Fast Prototyping lies in its use of cutting-edge 3D printing technologies. By harnessing the power of additive manufacturing, [Company Name] can create highly intricate and accurate prototypes directly from digital designs. This removes the need for costly and time-consuming manual modeling and machining processes, streamlining the entire development cycle.
Furthermore, [Company Name] has developed advanced materials specifically tailored for Fast Prototyping. These materials possess exceptional strength, durability, and surface finish properties, ensuring that the prototypes accurately represent the final product. This allows companies to make critical design decisions early on and avoid costly errors down the line.
The benefits of Fast Prototyping are not limited to design iteration speed and cost reduction. By quickly obtaining physical prototypes, businesses can test their products' ergonomics, functionality, and market appeal, gaining valuable insights that can inform further development iterations. This agile approach to product development empowers companies to meet customer demands swiftly and stay ahead of the competition.
In addition to their state-of-the-art technology, [Company Name] boasts a highly skilled team of engineers and designers who work closely with clients throughout the prototyping process. Their expertise and collaborative approach ensure that the envisioned product is accurately translated into physical form, guaranteeing customer satisfaction.
"Our innovation-driven approach has always been centered around helping businesses transform their ideas into tangible realities," said [Company Name]'s CEO. "With Fast Prototyping, we are enabling companies to prototype and iterate at an unprecedented pace, unlocking the potential for faster time-to-market and competitive advantage."
The applications of Fast Prototyping are vast and diverse. From aerospace to automotive, consumer electronics to medical devices, [Company Name] is committed to supporting a wide range of industries in their pursuit of innovation and excellence. Their technology will undoubtedly empower businesses to reimagine what is possible and bring their concepts to fruition in record time.
For companies looking to harness the power of Fast Prototyping, [Company Name] offers tailored solutions and comprehensive support throughout the entire prototyping process. This includes design optimization, material selection, and seamless integration with existing product development workflows.
As an industry leader and innovator, [Company Name] continues to revolutionize the field of product development. With Fast Prototyping, they are pioneering a new era of rapid, efficient, and cost-effective innovation, allowing businesses to turn their ideas into reality with unparalleled speed and precision.
About [Company Name]:
[Company Name] is a globally recognized leader in advanced product development and prototyping. With a team of highly skilled engineers and designers, they have been at the forefront of technological innovation for over [number of years] years. Their commitment to excellence and passion for driving innovation have cemented their position as a trusted partner for businesses across various industries.
Company News & Blog
Precision CNC Machining Services Offered by Chinese Factory
CNC machining has revolutionized the manufacturing industry, enabling companies to produce high-quality precision parts with speed and accuracy. One of the leading CNC machining factories in China offers custom precision CNC machining services, including CNC milling, CNC turning, and CNC machining. Whether you need steel machined parts or other materials, this factory can provide you with the precision parts you need.At this CNC machining factory, they use advanced technologies and state-of-the-art machines to manufacture precision parts. They have a team of highly skilled engineers and technicians who have extensive experience in manufacturing all types of precision parts. Their engineers can work with you to develop customized parts that fit your specific requirements.One of the advantages of CNC machining is that it allows for the production of complex shapes and designs with ease. The CNC machines are capable of working with a wide range of materials, including metals, plastics, and composites. The CNC machines can perform a range of operations, such as cutting, drilling, and milling, with remarkable accuracy.The factory's CNC milling services are ideal for manufacturing precise parts with complex geometries. They can produce parts up to 1 meter in length and 500mm in diameter. The CNC turning services are perfect for manufacturing precision parts with tight tolerances. They can produce parts up to 500mm in diameter and 1 meter in length.Whether you need steel machined parts for automotive applications, aerospace, medical, or any other industry, this factory can provide you with high-quality parts, precisely machined to your specifications. They use the latest technologies to accurately measure the parts and ensure that they are within the required tolerances.In addition to steel machined parts, they can provide custom CNC machining services for a wide range of materials, including aluminum, brass, titanium, and high-temperature alloys. They can also provide surface treatments, such as anodizing and painting, to give the parts the required finish.Moreover, the CNC machining factory in China offers competitive pricing for their precision CNC machining services. They have a fast turnaround time, so you can have your parts manufactured and delivered within a short time. They are committed to providing their customers with the highest quality parts and the best customer service.In conclusion, if you need steel machined parts or any other precision parts, consider working with this CNC machining factory in China. They have the expertise, technology, and equipment to manufacture high-quality precision parts to your exact specifications. They offer competitive pricing, fast turnaround time, and excellent customer service. Contact them today to learn more about their CNC machining services.
Discover the Advantages of In-House Metal Fabrication for Quality and Timely Delivery
Sheet Metal Panel Fabrication – The Ultimate Solution to All Metal Fabrication NeedsSheet metal fabrication has come a long way since its inception. It has become an indispensable part of various industries and is used extensively for a multitude of purposes. Be it aerospace, automotive, construction, or any other industry – sheet metal fabrication is crucial in all of them.Although there are numerous methods of sheet metal fabrication, sheet metal panel fabrication has gained immense popularity among manufacturers. The primary reason for its popularity is the accuracy and precision it offers while fabricating metal panels.Let's delve deeper into the aspects of sheet metal panel fabrication and understand how it can help manufacturers in their metal fabrication needs.What is Sheet Metal Panel Fabrication?Sheet metal panel fabrication is a process that involves cutting, folding, and shaping sheet metal into panels. These panels can be of various shapes and sizes, and the fabrication process can be customized as per the requirement.Sheet metal panel fabrication involves using various tools such as laser cutting machines, CNC punching machines, and hydraulic press brakes. These machines are highly efficient and can provide accurate and precise output with utmost consistency.Advantages of Sheet Metal Panel Fabrication1. Precision – As stated earlier, sheet metal panel fabrication provides a high degree of precision and accuracy. The cutting and folding are done with utmost care and attention to detail, ensuring that the metal panels meet the required specifications.2. Customization – Sheet metal panel fabrication can be customized to cater to the specific needs of the manufacturer. This versatility allows manufacturers to produce metal panels of various shapes, sizes, and thicknesses. This flexibility is not present in other methods of metal fabrication.3. Efficiency – Sheet metal panel fabrication is highly efficient and can deliver output at a much quicker rate than other methods of metal fabrication. The use of advanced machines enhances the efficiency of the process, making it an ideal choice for manufacturers who want to increase their production speed.4. Cost-Effective – Sheet metal panel fabrication can be cost-effective in the long run. The high degree of precision and accuracy results in minimal wastage of material, making it a cost-effective method for manufacturers who want to cut down on their raw material costs.ConclusionSheet metal panel fabrication has become an integral part of various industries. It offers precision, customization, efficiency, and cost-effectiveness, making it the ultimate solution for all metal fabrication needs. If you want to streamline your metal fabrication process and improve your production speed, sheet metal panel fabrication is an ideal choice.So, if you are looking for a reliable metal fabrication service provider, look no further than sheet metal panel fabrication experts. They can help you with all your metal fabrication needs, ensuring that the end product meets your specifications.
Discover the Art of Shaping Sheet Metal: A Comprehensive Guide
Title: Industry Leader Revolutionizes Sheet Metal ManufacturingIntroduction:In an era of constant innovation and advancement, the sheet metal manufacturing industry continues to evolve. One company, known for its groundbreaking techniques and commitment to excellence, has significantly contributed to the advancements of this sector. With their state-of-the-art production methods and cutting-edge technology, they have revolutionized the sheet metal manufacturing process, ensuring high-quality products and enhanced efficiency. Here, we delve into the key elements that make this company a leader in the industry.Research and Development:At the forefront of the company's success lies its relentless pursuit of research and development. By investing heavily in this area, they have been able to continuously discover and implement novel techniques and technologies into their manufacturing process. With an in-house team of highly skilled engineers and technicians, they consistently break new ground in the sheet metal industry. This dedication to R&D has allowed them to offer innovative solutions to their clients, overcoming challenges and meeting the ever-changing demands of the market.Advanced Machinery and Equipment:The company's commitment to cutting-edge technology is evident in its extensive use of advanced machinery and equipment. The production floor is equipped with high-precision lasers, computer numerical control (CNC) machines, and automated robotics, ensuring accuracy and consistency in every step of the manufacturing process. The integration of such advanced technology not only enhances the quality of the products but also improves overall operational efficiency, reducing production time and costs.Skilled Workforce:A company is only as good as its employees, and this industry leader understands the significance of a skilled workforce. They have assembled a team of highly trained professionals with extensive experience in sheet metal manufacturing. From machine operators and welders to quality control specialists and project managers, their employees possess the necessary expertise to meet the diverse needs of their clients. The company promotes a culture of continuous learning and advancement, providing regular training programs to keep pace with the ever-evolving industry requirements.Quality Assurance and Certifications:The company takes pride in its commitment to delivering the highest quality sheet metal products to its customers. Stringent quality control measures are in place throughout the manufacturing process to ensure that each product meets or exceeds industry standards. By employing cutting-edge inspection techniques and quality assurance protocols, they guarantee the durability, reliability, and precision of their sheet metal products. Additionally, the company holds various certifications, such as ISO 9001:2015 and ISO 14001:2015, further demonstrating their dedication to meeting global quality and environmental standards.Eco-Friendly Practices:In addition to quality manufacturing, the company prioritizes sustainability and environmental responsibility in its operations. By implementing eco-friendly practices, such as the use of energy-efficient machinery and recycling programs, they aim to minimize their carbon footprint. They continuously explore new ways to reduce waste and optimize resource utilization, contributing to a cleaner and greener planet while manufacturing superior sheet metal products.Customer-Centric Approach:Unlike many others in the industry, this company places a strong emphasis on building long-term relationships with its clients. They understand that each customer has unique requirements and tailor their services accordingly. By actively involving clients in the design process and offering personalized solutions, they ensure customer satisfaction throughout every project. The company's dedication to customer service has earned them a loyal clientele, with many returning for repeat business and referrals.Conclusion:In conclusion, this industry-leading company has revolutionized the sheet metal manufacturing industry through its commitment to research and development, advanced machinery, highly skilled workforce, quality assurance, sustainable practices, and customer-centric approach. By continually pushing the boundaries of innovation, they have set themselves apart as pioneers in the field. With their unmatched expertise and unwavering dedication to superior quality, this company will undoubtedly continue to shape the future of sheet metal manufacturing.
MTConnect-Ready 3D Printer for Aerospace and Production Applications
, MTConnect, FDM, aerospace, production, 3D printing.Additive Manufacturing Magazine recently reported that the Stratasys Fortus 900 3D printer now features an MTConnect-ready interface. This is great news for those working in aerospace and other industries that require high-quality, production-grade 3D printing.The Stratasys Fortus 900 is a Fused Deposition Modeling (FDM) 3D printer designed for large, complex parts. With a build volume of 36 x 24 x 36 inches, it has the capability to produce parts that are larger than those typically produced with plastic extrusion machines. This makes it an ideal choice for aerospace applications, as well as for producing jigs, fixtures, and tooling.Incorporating the MTConnect protocol into the Stratasys Fortus 900 means that users can now monitor and control their 3D printing operations in real time. MTConnect is an open, royalty-free standard for machine tool communication that has become increasingly popular in the manufacturing industry. With MTConnect, users can easily connect machines and devices to a network, allowing them to monitor data and make informed decisions about their operations.For aerospace manufacturers, the Stratasys Fortus 900 with MTConnect-ready interface is ideal, as it provides the capability to produce production-grade parts with repeatable accuracy. Additionally, 3D printing allows for the production of complex geometries that cannot be produced with traditional manufacturing methods.Overall, the integration of MTConnect into the Stratasys Fortus 900 3D printer is a positive development for the additive manufacturing industry. By providing real-time monitoring and control, it enables users to optimize their operations, increase efficiency, and improve the quality of their products. This is especially important in industries such as aerospace, where high-quality, production-grade parts are essential.As the use of 3D printing continues to grow, we can expect to see further developments in this area, and the integration of other technologies into 3D printers. In the meantime, the Stratasys Fortus 900 with MTConnect-ready interface is a great option for those looking to produce high-quality, production-grade parts with 3D printing technology.
Get the Best Wire Forming Machines for Sale in Melbourne - Top-notch Jigs and Templates Available!
Wire forming is a process that involves the shaping and molding of metal wires into different shapes. This process is used in a variety of industries from manufacturing to construction, and it plays an important role in the production of many different products. In this blog post, we will explore wire forming and why it's an essential process in many industries.Wire forming machinesWire forming machines are a critical tool in the wire forming process. These machines are designed to produce wire forms quickly and efficiently with precision. There are several types of wire forming machines available, including hydraulic and mechanical machines. These machines are capable of forming a range of materials, including brass, aluminum, and steel.The best wire forming machines should be easy to use, have precision controls, and offer versatility. They should also have a compact construction, making them suitable for use in small manufacturing facilities. Additionally, they should be built with durable materials that can withstand the constant wear and tear of the manufacturing process.In addition to wire forming machines, jigs and templates are commonly used in the wire forming process. These tools offer consistent and accurate wire forming results, which can increase production efficiency. They also help maintain product conformity, which is essential in industries where safety and quality are major concerns.Wire forming applicationsWire forming is a versatile process that can be used to create a vast array of products. Some of the most common applications of wire forming include:- Springs- Hooks- Wire baskets- Shelving- Clips- Hangers- Wire formsWire forming is also used in the creation of more complex products, such as automotive parts, medical devices, and electrical components. Wire forming is an important process that contributes to the safety, durability, and functionality of many everyday products.Finding a wire forming providerWhen selecting a wire forming provider, it's essential to consider several factors. Firstly, you should evaluate the provider's experience in wire forming and their track record in producing quality products. A provider that has been in the wire forming industry for many years will have a wealth of knowledge and experience. They will also have a proven track record of producing high-quality wire forms.Secondly, you should consider the provider's equipment and manufacturing facilities. Do they use the latest wire forming technology? Do they have the capacity to produce large volumes of wire forms? Choosing a provider with modern equipment and state-of-the-art facilities can help ensure that your wire forms are produced efficiently and accurately.Finally, you should consider the provider's customer service. Are they responsive and easy to work with? Do they offer technical support and guidance throughout the wire forming process? A wire forming provider with excellent customer service can make a significant difference in the success of your project.ConclusionWire forming is a crucial process in many industries, from manufacturing to construction. It allows manufacturers to create complex wire forms for use in a variety of different applications. Choosing the right wire forming provider is essential to ensure that your wire forms are produced accurately, efficiently, and to meet your specific needs. When selecting a wire forming provider, consider their experience, equipment, facilities, and customer service to ensure that you receive high-quality wire forms that meet your expectations.
Precision Sheet Metal Brackets Made with Advanced Manufacturing Techniques
: A Comprehensive Guide for Your Manufacturing NeedsSheet metal brackets are an integral part of any manufacturing process that requires the use of metal sheets. In industries that require immense precision and accuracy, the bracket systems ensure that the metal’s shape and structure are maintained throughout the process. With the advancements in modern CNC manufacturing processes, the quality of these bracket systems has improved significantly. The use of advanced automation tools has led to more efficient and precise manufacturing methods.Sheet metal brackets are widely used in various industries such as Aerospace, Medical, Automotive, Construction, and Electronics. In construction, sheet metal brackets are used to provide support to the structural systems, and in electronics, they secure electronic components in place. With their versatility, sheet metal brackets are an essential component in several processes and products.Here is a comprehensive guide to sheet metal brackets for all your manufacturing needs:Types of Sheet Metal Brackets1. Angle Brackets: These are brackets that are bent to 90-degree angles to create perpendicular structural joints. They are commonly used in construction to ensure that the structures maintain their shape and stability.2. U Brackets: These brackets have a U-shaped cross-section that is used to create a mounting point for objects. They are commonly used to mount objects onto walls and other surfaces.3. L Brackets: These are brackets that are bent to form an L-shape. They are used in most applications requiring reinforcement to prevent structural deformation.4. Z Brackets: These are brackets that are bent to form a ‘Z’ shape. They are used in construction to provide additional support to the structural systems.5. T Brackets: These are brackets that are bent to form a T-shape. They are commonly used to attach objects onto walls or other surfaces.Applications of Sheet Metal BracketsSheet metal brackets are used in various applications, including:AerospaceIn the aerospace industry, brackets are used to mount different types of equipment and systems such as electronics, fuel systems, engines, and landing gear. The brackets are usually made from lightweight materials like aluminum to minimize weight.AutomotiveIn the automotive industry, brackets are essential in holding the structural components of the car together. They are also used in securing electrical components in place.ConstructionSheet metal brackets are used extensively in the construction industry for many different applications, such as securing wall studs and reinforcing roof structures.ElectronicsIn the electronics industry, sheet metal brackets are used to secure electronic components in place. They are also used in creating housing systems for electrical components.MedicalSheet metal brackets are used in medical equipment and devices to support and hold various pieces of equipment such as monitors, IV poles, and other medical components in place.Manufacturing ProcessWith advancements in modern CNC manufacturing processes, sheet metal brackets can be precisely and efficiently manufactured. The manufacturing process for sheet metal brackets includes the following stages:1. Material Selection: The sheets of metal used in creating the brackets are usually made from various metals such as Stainless Steel, Carbon Steel, and Aluminum, and copper.2. Laser Cutting: The sheets of metal are cut using laser cutting machines to create the individual brackets' required shapes and sizes.3. Bending: The cut sheet metal is then bent using precision bending machines to create the desired shape of the bracket.4. Welding or Fixing: After bending the metal, the bracket components are welded or fixed together to create a final product.5. Finishing: The finished brackets are sandblasted or painted to give it a final finish.ConclusionSheet metal brackets are a vital part of many manufacturing processes. They provide structural support, aid in mounting equipment and components, and ensure precise manufacturing processes. The modern CNC manufacturing processes have significantly improved the manufacturing process of sheet metal brackets, leading to more efficient, accurate, and high-quality products. If you need sheet metal brackets for your manufacturing processes, ensure that you engage a reputable and experienced manufacturer who can deliver the desired results.
Discover the Best Stamping Tools and Beading Courses Online
and Bead Art’. Bead art has become increasingly popular over the past decade, reaching new levels of creativity and elegance. From bracelets, necklaces, and earrings to stunning home decor, beads offer a vast range of possibilities when it comes to crafting. There are numerous types of beads available in the market, each having its unique charm and quality. But, you may ask, how can you add that extra flavor to your bead art? Stamping tools can help!Stamping tools have been around for a long time and are usually used in leathercraft and metal stamping. However, they can be effectively used in creating bead art too. The technique brings out a new dimension in bead art and allows for a stylish and personalized touch.So, how do you use stamping tools in your bead art? For starters, you will need a few things: a set of stamping tools, a hammer, a workbench, and the beads that you want to stamp on. Once all these are in place, you can go ahead and start!First, you need to determine which stamping tool you want to use. There are various types of stamping tools available, including letters, numbers, and shapes. You can choose the alphabet stamping tool if you want to add a name or message onto your beads, or you could choose a pattern stamping tool to create a unique design on your beads.Once you have chosen the stamping tool, you can proceed to stamp the beads. Place the bead onto the workbench and position the stamping tool where you want it to be stamped. Then, gently tap the stamping tool with the hammer. Remember to be gentle as too much force could break the bead.Voila! You have added a personalized touch to your bead art. The possibilities are endless with stamping tools, and you can mix and match them to create unique designs on your beads.Bead It! iBEADS.com is an online store that offers classes in bead art and information about their two stores located in the island of Oahu. They have a vast range of beads and bead accessories available, including stamping tools. If you're a beginner or an experienced bead artist looking for inspiration, they offer classes catered to all levels.In conclusion, using stamping tools in bead art is an excellent way to add a personal flair to your jewelry pieces or home decor. With a little bit of creativity, you can come up with unique and stunning designs. Don't be afraid to experiment with different stamping tools and bead combinations – who knows, you might just discover your next masterpiece!
Maximizing Efficiency and Precision: Unlocking the Potential of Investment Casting
Prototype Investment Casting (PIC) is revolutionizing the manufacturing industry with its cutting-edge technology and innovative approach to investment casting. With a strong focus on quality, efficiency, and customer satisfaction, PIC is quickly becoming a go-to solution for businesses worldwide. By utilizing state-of-the-art equipment and a highly skilled team, PIC is able to deliver superior results and unmatched precision.PIC’s investment casting process begins with the creation of a prototype. Using advanced computer-aided design (CAD) software and 3D printing technology, the engineers at PIC are able to transform a concept into a physical model. This allows for better visualization and understanding of the final product, enabling any necessary adjustments to be made before proceeding to the casting stage.Once the prototype is finalized, PIC employs a unique investment casting method that involves creating a ceramic mold around the prototype. This mold is then filled with molten metal, which takes the shape of the prototype as it cools and solidifies. The ceramic mold is subsequently broken away, revealing the finished product with exceptional precision and surface finish.One of the key advantages of PIC’s investment casting process is its ability to produce complex and intricate parts with ease. Traditional manufacturing methods often struggle with intricate designs, but PIC’s advanced technology allows for the creation of highly detailed parts with minimal limitations. This versatility opens up a world of possibilities for industries such as aerospace, automotive, and medical, where precise components are crucial.In addition to its superior casting capabilities, PIC also places great importance on quality control. Every step of the manufacturing process is closely monitored to ensure that the final product meets the highest standards. From the initial design phase to the mold creation and casting, each component undergoes rigorous inspection and testing. This dedication to quality has earned PIC a reputation for delivering outstanding products that exceed customer expectations.Furthermore, PIC understands the importance of sustainability in the manufacturing industry. By employing an optimized production process and utilizing materials efficiently, PIC strives to minimize waste and reduce its environmental impact. The company also actively seeks out environmentally friendly materials and processes to integrate into its operations. Through its commitment to sustainability, PIC aims to contribute to a greener and more sustainable future for the industry.With its exceptional expertise and commitment to innovation, PIC has successfully served a wide range of industries, including aerospace, automotive, defense, and medical. Its ability to produce high-quality, intricate components has made it a trusted partner for many prominent companies. Whether it’s creating prototypes for new products or producing parts for existing ones, PIC’s investment casting process offers unmatched precision and efficiency.Looking ahead, PIC is continuing to expand its capabilities and refine its processes. The company invests heavily in research and development to stay at the forefront of technological advancements in the industry. By continuously exploring new techniques and materials, PIC aims to further enhance its offerings and remain a leader in investment casting.In conclusion, Prototype Investment Casting (PIC) is spearheading a new era in investment casting, delivering exceptional precision, quality, and efficiency. With its state-of-the-art technology, highly skilled team, and dedication to customer satisfaction, PIC is setting the standard for the manufacturing industry. As it continues to innovate and expand, PIC is poised to revolutionize the way products are made, offering endless possibilities for businesses worldwide.
Precision Grinding of CNC Machined Parts for Increased Durability and Performance
Title: Advancements in CNC Machined Parts Grinding: Delivering Precision and EfficiencyIntroduction (approx. 80 words):In the fast-paced world of manufacturing, the demand for precision-engineered components is at an all-time high. Addressing this need, a leading company in the field has made significant breakthroughs in CNC Machined Parts Grinding. By combining cutting-edge technology and industry expertise, they are revolutionizing the production of machined parts, offering unparalleled precision, efficiency, and reliability. With the ability to remove imperfections with remarkable accuracy, their advanced grinding techniques enhance product quality, reduce production time, and maximize cost-effectiveness.Innovation in CNC Machined Parts Grinding (approx. 200 words):Building on decades of experience and a commitment to continuous innovation, the company has introduced state-of-the-art advancements in CNC Machined Parts Grinding. By leveraging advanced robotic systems, high-precision tools, and computer numerical control (CNC) technology, they have transformed the grinding process, setting new standards in the industry.The integration of robotic systems has enabled precise handling and positioning of components, ensuring consistent grinding quality. This automation enhances productivity, eliminates human error, and optimizes production throughput. Additionally, it allows for multitasking capabilities, enabling simultaneous grinding of multiple parts, saving valuable time without compromising precision.Furthermore, the utilization of high-precision tools and cutting-edge abrasives guarantees the removal of imperfections with exceptional accuracy. By employing a combination of grinding wheels, belts, and discs designed for specific applications, the company ensures the highest level of precision, ensuring superior surface finishes and dimensional accuracy.To enhance the grinding process's efficiency, the company has incorporated CNC technology into their machining centers. This allows for seamless coordination between various machining operations, eliminating the need for multiple setups and tool changes. The result is faster cycle times, reduced downtime, and improved overall productivity.Benefits and Applications (approx. 250 words):The advancements in CNC Machined Parts Grinding have numerous benefits that make them indispensable for various manufacturing industries. The precision achieved through these techniques ensures the exact dimensions and tolerances required, eliminating the risk of errors and rework. By improving product quality and reducing rejects, manufacturers can establish a reputation for delivering superior components consistently.Moreover, these advancements have considerably reduced production time. With increased automation, multitasking capabilities, and efficient integration of CNC technology, companies can significantly improve throughput. This accelerates the delivery of finished parts, enabling manufacturers to meet tight deadlines without compromising quality.The cost-effectiveness of CNC Machined Parts Grinding is another crucial advantage. By streamlining processes and minimizing waste, manufacturers can optimize resource utilization and reduce production costs. In addition, the ability to complete complex grinding operations in a single setup reduces labor costs and machine downtime.The applications for CNC Machined Parts Grinding span various industries, including aerospace, automotive, robotics, medical, and more. In the aerospace sector, for instance, the precision grinding techniques are indispensable for creating intricate components that withstand the extreme demands of aircraft engines. Similarly, in the medical field, these advancements enable the production of high-precision parts for surgical instruments and prosthetics, ensuring utmost reliability and patient safety.Conclusion (approx. 70 words):Through their relentless pursuit of innovation, the company has transformed CNC Machined Parts Grinding, positioning themselves as industry leaders. With a focus on precision, efficiency, and cost-effectiveness, their advanced grinding techniques have revolutionized the manufacturing sector. By embracing these advancements, manufacturers can forge a path towards increased productivity, improved quality, and enhanced competitiveness in the global market.
Discover the Benefits and Process of Aluminum Casting for Industrial Applications
Title: Revolutionizing the Manufacturing Industry: Innovative Aluminum Casting Technology Disrupts Conventional PracticesIntroduction:In a landmark development, one of the leading pioneers in the manufacturing industry, [Company Name], has unveiled an innovative breakthrough in aluminum casting technology. By harnessing cutting-edge techniques and leveraging advanced materials, [Company Name] has successfully redefined the process of aluminum casting, revolutionizing traditional manufacturing practices.[Company Name]: A Driven Force in Manufacturing Advancements:[Company Name] has established itself as a visionary entity, consistently pushing the boundaries of innovation within the manufacturing sector. With an unwavering commitment to relentless research and development, the company has carved a niche for itself by introducing groundbreaking technologies that have transformed various industries.The company's commitment to quality, precision, and efficiency has propelled it to the forefront of the manufacturing industry. Recognized for its state-of-the-art facilities, highly skilled workforce, and dedication to sustainable practices, [Company Name] has earned an impeccable reputation as a reliable partner for global manufacturing needs.Revolutionary Aluminum Casting Technology:Through years of meticulous research, [Company Name] has successfully developed an advanced aluminum casting technique that offers unparalleled results. This groundbreaking technology leverages the strengths of aluminum and combines it with unique manufacturing processes to create durable and lightweight components, ushering in a new era of efficiency and cost-effectiveness for manufacturers worldwide.Unlike traditional casting methods that rely on molds, [Company Name]'s pioneering approach utilizes precision computer-aided design (CAD) software to create intricate designs. These designs are then transformed into physical components using a state-of-the-art 3D printing technique. This eliminates the need for expensive and time-consuming mold creation, significantly reducing lead times and costs associated with traditional casting processes.The innovative approach employed by [Company Name] allows for greater design freedom, enabling manufacturers to produce complex shapes and geometrically demanding components with ease. Additionally, this technology supports creating components with thinner walls while maintaining the required strength, resulting in lighter end products without compromising structural integrity.Key Advantages and Benefits:[Company Name]'s pioneering aluminum casting technology provides manufacturers across diverse industries with numerous significant advantages and benefits:1. Increased Efficiency: The elimination of molds and the employment of 3D printing techniques greatly reduce the time required for design iterations and overall production, leading to enhanced efficiency and faster time-to-market.2. Cost-effectiveness: The streamlined manufacturing process reduces material waste, energy consumption, and labor costs, resulting in significant savings for manufacturers.3. Versatility: The innovative technology enables the production of complex shapes and intricate designs previously deemed impractical or unattainable using conventional casting methods.4. Enhanced Performance: The resulting aluminum components offer exceptional strength-to-weight ratios, corrosion resistance, and thermal conductivity—characteristics critical for various industries, including automotive, aerospace, and consumer electronics.5. Sustainability: [Company Name]'s aluminum casting technology aligns with environmentally conscious practices by reducing waste, minimizing energy consumption, and supporting the use of recyclable materials.Future Prospects:The introduction of [Company Name]'s disruptive aluminum casting technology has already begun to reshape the manufacturing landscape. As manufacturers increasingly seek enhanced efficiency, performance, and cost-effectiveness, the demand for this innovative technology is set to soar.Furthermore, [Company Name] continues to invest in research and development, aiming to enhance the capabilities of their aluminum casting technology further. By constantly pushing the boundaries of what is achievable, [Company Name] aims to redefine industry standards while unlocking new possibilities in multiple sectors.Conclusion:In an industry known for its evolution and groundbreaking advancements, [Company Name] has emerged as a driving force behind revolutionary aluminum casting technology. This game-changing approach promises to reshape traditional manufacturing practices, offering unprecedented versatility, efficiency, and cost-effectiveness. With [Company Name] at the forefront, the manufacturing world is set to undergo a transformative shift, as this innovative aluminum casting technology powers a new era of manufacturing excellence.