Precision Grinding of CNC Machined Parts for Increased Durability and Performance
By:Admin
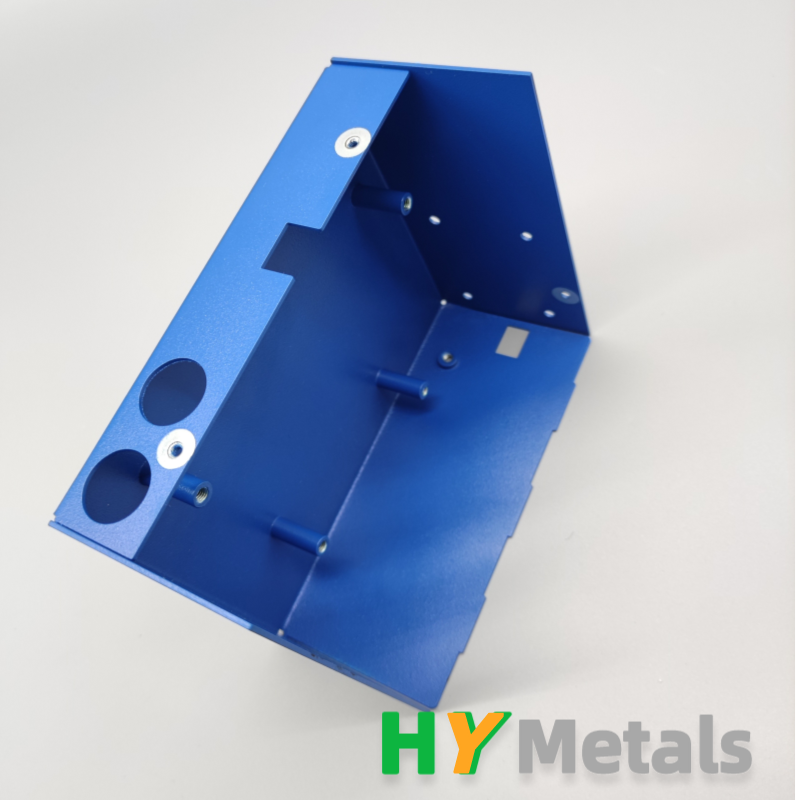
Introduction (approx. 80 words):
In the fast-paced world of manufacturing, the demand for precision-engineered components is at an all-time high. Addressing this need, a leading company in the field has made significant breakthroughs in CNC Machined Parts Grinding. By combining cutting-edge technology and industry expertise, they are revolutionizing the production of machined parts, offering unparalleled precision, efficiency, and reliability. With the ability to remove imperfections with remarkable accuracy, their advanced grinding techniques enhance product quality, reduce production time, and maximize cost-effectiveness.
Innovation in CNC Machined Parts Grinding (approx. 200 words):
Building on decades of experience and a commitment to continuous innovation, the company has introduced state-of-the-art advancements in CNC Machined Parts Grinding. By leveraging advanced robotic systems, high-precision tools, and computer numerical control (CNC) technology, they have transformed the grinding process, setting new standards in the industry.
The integration of robotic systems has enabled precise handling and positioning of components, ensuring consistent grinding quality. This automation enhances productivity, eliminates human error, and optimizes production throughput. Additionally, it allows for multitasking capabilities, enabling simultaneous grinding of multiple parts, saving valuable time without compromising precision.
Furthermore, the utilization of high-precision tools and cutting-edge abrasives guarantees the removal of imperfections with exceptional accuracy. By employing a combination of grinding wheels, belts, and discs designed for specific applications, the company ensures the highest level of precision, ensuring superior surface finishes and dimensional accuracy.
To enhance the grinding process's efficiency, the company has incorporated CNC technology into their machining centers. This allows for seamless coordination between various machining operations, eliminating the need for multiple setups and tool changes. The result is faster cycle times, reduced downtime, and improved overall productivity.
Benefits and Applications (approx. 250 words):
The advancements in CNC Machined Parts Grinding have numerous benefits that make them indispensable for various manufacturing industries. The precision achieved through these techniques ensures the exact dimensions and tolerances required, eliminating the risk of errors and rework. By improving product quality and reducing rejects, manufacturers can establish a reputation for delivering superior components consistently.
Moreover, these advancements have considerably reduced production time. With increased automation, multitasking capabilities, and efficient integration of CNC technology, companies can significantly improve throughput. This accelerates the delivery of finished parts, enabling manufacturers to meet tight deadlines without compromising quality.
The cost-effectiveness of CNC Machined Parts Grinding is another crucial advantage. By streamlining processes and minimizing waste, manufacturers can optimize resource utilization and reduce production costs. In addition, the ability to complete complex grinding operations in a single setup reduces labor costs and machine downtime.
The applications for CNC Machined Parts Grinding span various industries, including aerospace, automotive, robotics, medical, and more. In the aerospace sector, for instance, the precision grinding techniques are indispensable for creating intricate components that withstand the extreme demands of aircraft engines. Similarly, in the medical field, these advancements enable the production of high-precision parts for surgical instruments and prosthetics, ensuring utmost reliability and patient safety.
Conclusion (approx. 70 words):
Through their relentless pursuit of innovation, the company has transformed CNC Machined Parts Grinding, positioning themselves as industry leaders. With a focus on precision, efficiency, and cost-effectiveness, their advanced grinding techniques have revolutionized the manufacturing sector. By embracing these advancements, manufacturers can forge a path towards increased productivity, improved quality, and enhanced competitiveness in the global market.
Company News & Blog
Latest Updates on the World of Electronic Dance Music
[Company Name Removed] Expands Its Footprint in the Dynamic World of Electronic Dance Music (EDM)(Date)The global electronic dance music (EDM) industry has witnessed an unprecedented surge in popularity in recent years. As this vibrant genre continues to captivate millions of music lovers worldwide, [Company Name Removed], a leading player in the music industry, is excited to announce its expanding presence in the EDM scene.With over two decades of experience in curating and promoting extraordinary music events, [Company Name Removed] has cemented its position as a visionary force in the music industry. The company has successfully organized some of the most iconic concerts and festivals, leaving an indelible mark on the hearts of music enthusiasts across the globe.The decision to venture into EDM is a strategic move for [Company Name Removed], considering its immense potential and ever-growing fan base. The genre's fusion of infectious beats, captivating rhythms, and electrifying energy has transcended borders and united people from various cultural backgrounds.As part of its foray into EDM, [Company Name Removed] aims to introduce a fresh wave of artistic talent and provide a platform for emerging DJs and producers. By scouting new talents through collaborations with established EDM artists, the company seeks to foster the growth of the genre and inspire a new generation of music creators.The expansion into EDM will also see [Company Name Removed] launching its own record label specifically dedicated to this genre. With a strong focus on nurturing talents and exploring cutting-edge sounds, the record label aims to become a breeding ground for chart-topping EDM hits and groundbreaking collaborations.In addition to discovering new talents, [Company Name Removed] plans to organize an array of EDM events and festivals to showcase the genre's vast diversity. These events will provide an immersive experience for attendees, combining stunning visual effects, state-of-the-art production, and performances from the biggest names in the EDM scene.[Company Name Removed] also recognizes the importance of technology in shaping the future of music consumption. Thus, the company is actively investing in cutting-edge technologies to enhance the overall experience of EDM enthusiasts. By leveraging virtual reality (VR) and augmented reality (AR), [Company Name Removed] aims to transport its audience into a digital realm where they can feel the pulsating beats and immerse themselves in an otherworldly atmosphere.To further solidify its position in the EDM industry, [Company Name Removed] plans to collaborate with leading EDM festivals and organizations across the globe. By forging strategic partnerships and sharing expertise, the company aims to create a worldwide network that will open doors for collaboration and mutually beneficial ventures.Furthermore, [Company Name Removed]'s expansion into the world of EDM is driven by a strong commitment to sustainability and community welfare. The company aims to organize eco-friendly festivals and events, ensuring responsible waste management and promoting environmental awareness among its audience. Additionally, [Company Name Removed] plans to collaborate with local communities and charitable organizations, using the power of EDM to bring about positive social change.As [Company Name Removed] gears up to enter the electrifying realm of EDM, music enthusiasts can expect groundbreaking collaborations, mesmerizing events, and the discovery of new and innovative sounds. With its unparalleled track record in event organization and artist promotion, [Company Name Removed] is poised to make a lasting impact on the vibrant world of electronic dance music.
Discover the Art of Shaping Sheet Metal: A Comprehensive Guide
Title: Industry Leader Revolutionizes Sheet Metal ManufacturingIntroduction:In an era of constant innovation and advancement, the sheet metal manufacturing industry continues to evolve. One company, known for its groundbreaking techniques and commitment to excellence, has significantly contributed to the advancements of this sector. With their state-of-the-art production methods and cutting-edge technology, they have revolutionized the sheet metal manufacturing process, ensuring high-quality products and enhanced efficiency. Here, we delve into the key elements that make this company a leader in the industry.Research and Development:At the forefront of the company's success lies its relentless pursuit of research and development. By investing heavily in this area, they have been able to continuously discover and implement novel techniques and technologies into their manufacturing process. With an in-house team of highly skilled engineers and technicians, they consistently break new ground in the sheet metal industry. This dedication to R&D has allowed them to offer innovative solutions to their clients, overcoming challenges and meeting the ever-changing demands of the market.Advanced Machinery and Equipment:The company's commitment to cutting-edge technology is evident in its extensive use of advanced machinery and equipment. The production floor is equipped with high-precision lasers, computer numerical control (CNC) machines, and automated robotics, ensuring accuracy and consistency in every step of the manufacturing process. The integration of such advanced technology not only enhances the quality of the products but also improves overall operational efficiency, reducing production time and costs.Skilled Workforce:A company is only as good as its employees, and this industry leader understands the significance of a skilled workforce. They have assembled a team of highly trained professionals with extensive experience in sheet metal manufacturing. From machine operators and welders to quality control specialists and project managers, their employees possess the necessary expertise to meet the diverse needs of their clients. The company promotes a culture of continuous learning and advancement, providing regular training programs to keep pace with the ever-evolving industry requirements.Quality Assurance and Certifications:The company takes pride in its commitment to delivering the highest quality sheet metal products to its customers. Stringent quality control measures are in place throughout the manufacturing process to ensure that each product meets or exceeds industry standards. By employing cutting-edge inspection techniques and quality assurance protocols, they guarantee the durability, reliability, and precision of their sheet metal products. Additionally, the company holds various certifications, such as ISO 9001:2015 and ISO 14001:2015, further demonstrating their dedication to meeting global quality and environmental standards.Eco-Friendly Practices:In addition to quality manufacturing, the company prioritizes sustainability and environmental responsibility in its operations. By implementing eco-friendly practices, such as the use of energy-efficient machinery and recycling programs, they aim to minimize their carbon footprint. They continuously explore new ways to reduce waste and optimize resource utilization, contributing to a cleaner and greener planet while manufacturing superior sheet metal products.Customer-Centric Approach:Unlike many others in the industry, this company places a strong emphasis on building long-term relationships with its clients. They understand that each customer has unique requirements and tailor their services accordingly. By actively involving clients in the design process and offering personalized solutions, they ensure customer satisfaction throughout every project. The company's dedication to customer service has earned them a loyal clientele, with many returning for repeat business and referrals.Conclusion:In conclusion, this industry-leading company has revolutionized the sheet metal manufacturing industry through its commitment to research and development, advanced machinery, highly skilled workforce, quality assurance, sustainable practices, and customer-centric approach. By continually pushing the boundaries of innovation, they have set themselves apart as pioneers in the field. With their unmatched expertise and unwavering dedication to superior quality, this company will undoubtedly continue to shape the future of sheet metal manufacturing.
High Precision Vacuum Casting Filament for Consistent Layering and Easy Support Removal
and 3D printing.In today's fast-paced technological world, 3D printing has become increasingly popular, revolutionizing the way we design and create products. One of the key features of 3D printing is the new range of materials available which can produce high-quality and accurate printed products. Vaccum Casting is one such material that is perfect for the production of complex or intricate parts.Vaccum Casting is a thermoplastic elastomer that is commonly used in 3D printing. Its unique properties make it a perfect choice for printing objects that require precision and accuracy. With an extrusion temperature ranging from 175-200C, Vaccum Casting is an ideal option for printing small and delicate parts. The filament also has high roundness and precision of +/- 0.01 mm, ensuring that your print is accurate and of high quality.One of the key benefits of Vaccum Casting is that it sticks nicely to glass/kapton tape heated bed, resulting in no first-layer problem. This makes it easier to work with as it ensures that the print stays in place while printing. Additionally, the filament extrudes precisely for fast printing and consistent layering, which results in better prints overall.Filament comes in a light/compact spool, in a sealed package with a bag of desiccant, which ensures that the filament remains dry and of high quality. The desiccant is a moisture-absorbing material, which means that even if the filament is kept in a humid environment, it will not absorb the moisture and will be of high quality during printing.Another key benefit of Vaccum Casting is that it is easy to remove support material. When printing complex or intricate parts, support material is often required to ensure that the parts maintain their shape and structure. Vaccum Casting's easy-to-remove support material feature ensures that you can quickly and easily remove the material and finish your prints.In conclusion, Vaccum Casting is an excellent material for 3D printing, with its unique properties making it ideal for producing small and complex parts. Its high roundness and precision make it ideal for printing objects that require accuracy and precision. The ease of removing support material and the ability to stick nicely to a heated bed are other benefits that make Vaccum Casting a preferred option for 3D printing. So, if you're looking for a reliable and precise filament for 3D printing, be sure to try Vaccum Casting.
Wire Bending Techniques: Exploring the Art of Precision and Versatility
Wire Bending Innovations Revolutionize Manufacturing ProcessesWire bending is an essential technique used in various industries such as automotive, aerospace, and electronics to shape wires into precise designs. The traditional process involves manual labor and is often time-consuming and prone to human errors. However, recent advancements in wire bending technology have presented a new era of efficiency and accuracy. Companies like {} are at the forefront of this revolution, introducing state-of-the-art wire bending machines that are transforming manufacturing processes.Wire bending machines developed by {} utilize cutting-edge technology to automate the wire shaping process. By incorporating computer numerical control (CNC) systems, these machines can precisely determine and execute complex wire bending patterns. This level of automation significantly reduces the need for manual labor, minimizing operational costs and increasing production efficiency.One of the key advantages of {}'s wire bending machines is their versatility. The machines can work with wires of various materials and diameters, allowing manufacturers to produce a wide range of products. Whether it is small intricate components for electronics or larger structural parts for automobiles, these machines can handle the task with utmost precision.The accuracy achieved by these wire bending machines is truly remarkable. They can consistently produce wire shapes that adhere to strict tolerances, ensuring repeatable quality in mass production. This level of precision is crucial in industries where even a minor dimensional variation can lead to defective products or compromised safety.Apart from the accuracy, one of the notable features of {}'s wire bending machines is their speed. By automating the wire bending process, these machines can operate at higher speeds compared to manual labor. This leads to shorter production cycles, enabling manufacturers to meet growing market demands effectively.Additionally, {}'s wire bending machines integrate advanced software that allows for seamless programming and control. Manufacturers can design wire patterns through intuitive computer-aided design (CAD) software and transfer the instructions to the wire bending machine. The ease of programming ensures quicker setup times and reduces the likelihood of errors. As a result, manufacturers can achieve faster time-to-market while maintaining the highest quality standards.Another positive aspect of {}'s wire bending machines is their user-friendly interface. The machines are designed to be easily operated by technicians with minimal training. Intuitive controls and clear visual feedback make it convenient for operators to monitor and adjust the wire bending process as needed. This simplicity provides manufacturers with the flexibility to quickly adapt to changing production requirements.The adoption of {}'s wire bending machines has had significant impacts on manufacturing businesses. Manufacturers have reported increased productivity, reduced production costs, and improved product quality. By automating wire bending processes, companies can achieve higher volumes of production while minimizing human errors and associated costly rework.Moreover, {}'s wire bending machines have also opened up opportunities for innovative designs. With the ability to produce intricate wire shapes effortlessly, manufacturers can explore new product possibilities that were previously limited by manual wire bending. This level of flexibility empowers companies to stay ahead of the competition and cater to evolving customer demands.In conclusion, the advancements in wire bending technology, as exemplified by {}'s innovative machines, have revolutionized manufacturing processes. By automating wire bending, manufacturers can now achieve higher productivity, superior product quality, and faster time-to-market. With the ability to work with different wire materials and diameters, these machines provide unparalleled versatility. As manufacturers continue to embrace these cutting-edge technologies, the future of efficient and precise wire bending looks promising.
Innovative Prototype of Next-Generation Heatsink Unveiled, Revolutionizing Cooling Technology
In the world of technology, finding ways to cool devices is an essential element in ensuring their longevity and functionality. Overheating has proven to be a significant problem, especially in more advanced computers and gaming consoles. To combat this, a company has developed a prototype heatsink that offers efficient cooling with a sleek and modern design.The heatsink prototype, which is made from high-quality materials, has been tested extensively to ensure its efficiency in cooling electronics. The prototype has been developed with an eye towards aesthetics by featuring an attractive, modern design that emphasizes functionality, with a sleek black finish that will complement any computer or gaming console.According to representatives from the company, this heatsink prototype utilizes a unique combination of materials, including aluminum, copper, and nickel. These materials help to create an efficient cooling solution that will drastically reduce the risk of overheating, enabling users to work on their devices without fear of hardware malfunction.The company behind this innovative product is a leading manufacturer of computer and gaming peripherals. With years of experience and dedication, they have gained a reputation for producing high-quality products that address the needs of tech enthusiasts and professionals alike.The company has a range of computer and gaming peripherals, including headphones, keyboards, and monitors, among others. The company has attained the trust of many users due to their ability to produce innovative and reliable products consistently.The prototype of the heatsink has been developed as a part of the company's commitment to research and development. The company stated that by investing in R&D, they could remain innovative and remain committed to developing products that meet the evolving needs of their customers.The heatsink prototype is a testament to the company’s ability to create products that are both innovative and functional while meeting consumers' needs. The company's focus on aesthetics has ensured that the heatsink is not just efficient but is also visually appealing, adding an element of style to the user's computer or gaming setup.Additionally, the heatsink's materials have been carefully selected to ensure that it is durable and long-lasting, a critical factor for computer or gaming enthusiasts who invest in high-end devices that need reliable cooling solutions.The company mentioned that the prototype is currently being tested on numerous devices. The testing process is conducted under various conditions and represents real-life scenarios to ensure the heatsink provides optimal cooling results in various environments. The company is committed to ensuring that customers receive the best product by putting the finished product through rigorous testing procedures.The heatsink prototype's benefits cannot be overstated as it solves a significant problem for the technology industry while also providing a product that is both functional and aesthetically pleasing. The product's development showcases the company's commitment to innovation, investing time and money to offer sophisticated solutions to consumers' problems.While the heatsink prototype is still undergoing testing, the company aims to release the product soon. As demand for heat sinking solutions increases, the company is well-positioned to meet consumer needs. The company has assured its customers that upon the product's release, it will be widely available globally, making it easy for consumers to access the innovative product regardless of their location.In conclusion, the company that has developed the prototype heatsink is on the path to revolutionizing the cooling solutions industry. The company's commitment to researching and developing innovative products has enabled them to address the needs of computer and gaming enthusiasts successfully. As technology continues to evolve, the company seems adequately positioned to be at the forefront of offering sophisticated solutions to users. Customers eagerly wait for the release of the heatsink prototype, which promises excellent functionality and aesthetics.
Maximizing Efficiency and Precision: Unlocking the Potential of Investment Casting
Prototype Investment Casting (PIC) is revolutionizing the manufacturing industry with its cutting-edge technology and innovative approach to investment casting. With a strong focus on quality, efficiency, and customer satisfaction, PIC is quickly becoming a go-to solution for businesses worldwide. By utilizing state-of-the-art equipment and a highly skilled team, PIC is able to deliver superior results and unmatched precision.PIC’s investment casting process begins with the creation of a prototype. Using advanced computer-aided design (CAD) software and 3D printing technology, the engineers at PIC are able to transform a concept into a physical model. This allows for better visualization and understanding of the final product, enabling any necessary adjustments to be made before proceeding to the casting stage.Once the prototype is finalized, PIC employs a unique investment casting method that involves creating a ceramic mold around the prototype. This mold is then filled with molten metal, which takes the shape of the prototype as it cools and solidifies. The ceramic mold is subsequently broken away, revealing the finished product with exceptional precision and surface finish.One of the key advantages of PIC’s investment casting process is its ability to produce complex and intricate parts with ease. Traditional manufacturing methods often struggle with intricate designs, but PIC’s advanced technology allows for the creation of highly detailed parts with minimal limitations. This versatility opens up a world of possibilities for industries such as aerospace, automotive, and medical, where precise components are crucial.In addition to its superior casting capabilities, PIC also places great importance on quality control. Every step of the manufacturing process is closely monitored to ensure that the final product meets the highest standards. From the initial design phase to the mold creation and casting, each component undergoes rigorous inspection and testing. This dedication to quality has earned PIC a reputation for delivering outstanding products that exceed customer expectations.Furthermore, PIC understands the importance of sustainability in the manufacturing industry. By employing an optimized production process and utilizing materials efficiently, PIC strives to minimize waste and reduce its environmental impact. The company also actively seeks out environmentally friendly materials and processes to integrate into its operations. Through its commitment to sustainability, PIC aims to contribute to a greener and more sustainable future for the industry.With its exceptional expertise and commitment to innovation, PIC has successfully served a wide range of industries, including aerospace, automotive, defense, and medical. Its ability to produce high-quality, intricate components has made it a trusted partner for many prominent companies. Whether it’s creating prototypes for new products or producing parts for existing ones, PIC’s investment casting process offers unmatched precision and efficiency.Looking ahead, PIC is continuing to expand its capabilities and refine its processes. The company invests heavily in research and development to stay at the forefront of technological advancements in the industry. By continuously exploring new techniques and materials, PIC aims to further enhance its offerings and remain a leader in investment casting.In conclusion, Prototype Investment Casting (PIC) is spearheading a new era in investment casting, delivering exceptional precision, quality, and efficiency. With its state-of-the-art technology, highly skilled team, and dedication to customer satisfaction, PIC is setting the standard for the manufacturing industry. As it continues to innovate and expand, PIC is poised to revolutionize the way products are made, offering endless possibilities for businesses worldwide.
What is Water-jet Technology and How Does it Work?
Water-jet technology has evolved significantly over the years, providing a versatile and efficient solution for a range of industrial applications. This technology involves the use of a high-pressure pump to create a stream of water that can be used to cut, clean, and shape different materials. Water-jet technology is fast becoming the go-to option for many employers in varied industries.The process of water-jet cutting starts by using a high-pressure pump that pumps water through a nozzle, which produces a super-fast stream of water that is directed onto the material to be cut. The water pressure can be adjusted to suit the type of material being cut, from soft materials like plastic, rubber, and foam to hard materials like metals, ceramics, and glass.One of the most significant benefits of water-jet technology is its ability to perform intricate cuts without creating heat-affected zones (HAZ). Thermal distortion, discoloration, and other undesirable effects are often seen when traditional cutting methods are used, like plasm cutting. However, water-jet cutting ensures material integrity through cold cutting, making it ideal for precision machining, intricate architectural designs, medical equipment, aerospace, and automotive parts.Traditional cutting methods such as laser and plasma can produce toxic fumes or debris that can be dangerous to the environment and human health. In contrast, water-jet cutting is eco-friendly and safe. The water used in this process can be recycled and reused, and the cutting operation produces no hazardous waste, allowing companies to reduce their environmental footprint considerably.Moreover, water-jet technology requires no special tooling, which means changing between different materials and designs is a breeze. This makes water-jet cutting an even more attractive option for manufacturers who need to switch between various production requirements quickly. Additionally, with advancements in technology, 5-axis cutting technology and robotics can be utilized, allowing greater flexibility and increased accuracy in cutting, ensuring more efficient and cost-effective production.The benefits of water-jet technology are not limited to cutting and shaping applications, as it has other uses too. Water-jet cleaning is another application of this technology. It involves the use of high-pressure water streams to remove dirt and grime from surfaces, making it an effective cleaning option for many businesses. Cleaning using a water-jet is particularly useful in the food and beverage industry, where sanitation is critical.Another advantage of using water-jet technology in cleaning is that it does not require any chemicals to aid the cleaning process. This, in turn, ensures that the cleaned surfaces are safe for human consumption, eliminating the need for chemical-based cleaning agents harmful to the environment and humans. The use of water-jet technology in cleaning can significantly reduce washing times and increase production efficiency, making it an ideal solution for many businesses.In conclusion, water-jet technology presents an innovative and eco-friendly solution for many manufacturing and cleaning applications. Its benefits are unrivaled when compared to traditional cutting and cleaning technologies. From increased production efficiency to reduced environmental footprint to the ability to perform intricate and precise cuts, water-jet technology has fast become a sought-after option for many businesses looking to improve their bottom line. Companies that have not yet implemented this technology in their operations are urged to give it a try and discover the numerous cost and time-saving benefits it can offer.
Discover the Artistry of Custom Metal Work for Exquisite Designs
Custom Metal Work Expands Portfolio With Innovative SolutionsCustom Metal Work, a leading provider of metal fabrication solutions, is excited to announce the addition of several new products and services to their extensive portfolio. With over two decades of experience, the company has built a reputation for delivering high-quality, customized metalwork to a wide range of industries.As a trusted name in the metal fabrication industry, Custom Metal Work takes pride in their ability to cater to the unique needs of each client. By combining state-of-the-art technology with a team of skilled craftsmen, the company consistently delivers innovative solutions that meet the highest standards of quality and precision.One of the latest additions to Custom Metal Work’s portfolio is their line of cutting-edge laser cutting services. Using cutting-edge machinery, the company can now provide precise and intricate metal cutting, ensuring a superior finish with minimal material waste. This new capability allows them to serve industries such as automotive, aerospace, and construction more efficiently and effectively.In addition to their laser cutting services, Custom Metal Work also offers a diverse range of metal fabrication solutions. From custom sheet metal forming to precision welding, the company can fulfill even the most complex design requirements. Their team of experts work closely with clients to understand their unique needs, providing tailored solutions that exceed expectations.One of the key features that sets Custom Metal Work apart is their commitment to sustainability. The company utilizes advanced recycling techniques and environmentally friendly materials to minimize their impact on the environment. By adopting a greener approach, they not only contribute to a healthier planet but also help clients achieve their sustainability goals.Custom Metal Work’s dedication to innovation and continuous improvement has earned them numerous accolades within the industry. The company’s relentless pursuit of excellence has resulted in long-standing partnerships with leading companies across various sectors, bolstering its reputation as a reliable, customer-centric metal fabrication specialist.“We are thrilled to expand our portfolio with these exciting new products and services,” stated [company spokesperson]. “Our team has worked tirelessly to equip ourselves with the latest technology and expertise to meet the evolving demands of our clients. With these additions, we are confident that we can continue to deliver top-notch metal fabrication solutions that drive success for our clients.”Clients who have worked with Custom Metal Work express their satisfaction with the company’s ability to deliver quality products within budget and on time. Their attention to detail and commitment to customer service sets them apart from competitors in the industry. From large-scale industrial projects to small-scale custom designs, Custom Metal Work has consistently proven their ability to handle projects of any size and complexity.Moving forward, Custom Metal Work aims to remain at the forefront of the metal fabrication industry by continuously exploring new technologies and refining their processes. With their expanded portfolio of services and unwavering dedication to customer satisfaction, the company is poised to bring even greater value to clients across the globe.About Custom Metal Work:Custom Metal Work is a leading provider of innovative metal fabrication solutions. With over twenty years of experience, the company specializes in custom sheet metal forming, precision welding, and laser cutting services. Combining cutting-edge technology with skilled craftsmanship, Custom Metal Work delivers customized metalwork that meets the highest standards of quality and precision. Their commitment to sustainability and attention to detail set them apart from competitors in the industry.
Revolutionary Multi-Axis Turning: Unleashing New Possibilities in Precision Engineering
Multi-Axis Turning: Revolutionizing Precision MachiningPrecision machining has long been a staple in various industries, ensuring the production of high-quality components and products that meet the stringent demands of modern technology. In this regard, one technology has been making waves in the field - Multi-Axis Turning.Through its advanced capabilities and exceptional precision, Multi-Axis Turning has revolutionized the world of machining, providing numerous benefits to manufacturers, engineers, and ultimately, end-users. This cutting-edge technology combines state-of-the-art machinery with innovative software solutions to produce intricate designs and complex geometries with unmatched accuracy. By removing the constraints of traditional machining processes, Multi-Axis Turning sets new standards in terms of speed, versatility, and efficiency.One of the key features of Multi-Axis Turning is its ability to simultaneously move and rotate the component being machined, allowing for multi-directional cutting. This unique motion control enables the creation of complex shapes and contours that would otherwise be extremely difficult to achieve using conventional turning methods. By utilizing multiple cutting axes, manufacturers can perform intricate operations in a single machine setup, reducing production time and costs while ensuring exceptional precision.Moreover, Multi-Axis Turning minimizes the need for manual intervention, as much of the setup and tool positioning is automated. The integration of sophisticated software systems streamlines the machining process, eliminating human error and ensuring consistent results. This high degree of automation enhances productivity, increases throughput, and reduces the dependency on skilled labor, which ultimately translates into significant cost savings for manufacturers.One notable advantage of Multi-Axis Turning is its versatility. It can handle a wide range of materials, including metals, plastics, and composites, making it suitable for various industries such as aerospace, automotive, medical, and electronics. The ability to work with different materials expands the applications of Multi-Axis Turning, enabling manufacturers to produce intricate parts for diverse products with ease.Furthermore, Multi-Axis Turning excels in producing parts with exceptional surface finishes, a crucial aspect in industries where aesthetics, accuracy, and functionality go hand in hand. The simultaneous multi-axis movement allows for smoother tool paths, minimizing vibrations and enhancing surface quality. This capability is particularly important for critical components used in industries such as medical devices, where precision and superior finish are paramount.In recent years, a company at the forefront of Multi-Axis Turning technology has emerged - {}. With their cutting-edge machinery and industry-leading expertise, they have been instrumental in advancing the field of precision machining. Their state-of-the-art equipment boasts unmatched capabilities, offering multi-axis milling, turning, and drilling in a single setup. Moreover, their comprehensive software solutions enable seamless integration between design, simulation, and manufacturing processes, ensuring optimal results and increased efficiency.By pioneering Multi-Axis Turning, {} has revolutionized precision machining in terms of accuracy, speed, and versatility. Their commitment to innovation and continuous improvement has propelled the industry forward, enabling manufacturers to achieve new heights in manufacturing excellence. With their comprehensive range of machinery and software solutions, {} is poised to shape the future of precision machining, empowering industries worldwide.In conclusion, Multi-Axis Turning has emerged as a game-changer in the field of precision machining. Its ability to produce complex geometries, enhance surface finishes, and streamline the manufacturing process has made it indispensable for modern industries. With its wide range of applications and technological advancements, Multi-Axis Turning holds immense potential for transforming the way we manufacture and design components, setting new standards of precision and efficiency.
Production-Grade 3D Printer Enables MTConnect Integration for Aerospace and Industrial Applications
, F900 3D printer, production applications, aerospace industry, MTConnect protocol.Additive manufacturing has revolutionized the manufacturing industry with the ability to create complex geometries with high precision and speed. One of the leading players in the additive manufacturing market is the F900 3D printer, designed for production applications in the aerospace industry and other high-performance industries. This blog discusses the latest development in the F900 3D printer, which now features an MTConnect-ready interface, offering enhanced connectivity and data exchange capabilities.The F900 3D printer is known for its high-performance capabilities, reliability, and large-scale printing. The printer uses the Fused Deposition Modeling (FDM) technology, which involves building 3D models layer by layer by depositing material in a melted state. The FDM technology provides a high degree of design flexibility, allowing the production of complex geometries without the need for additional machining or assembly processes.The F900 3D printer has been widely used in the aerospace industry for the production of complex parts, such as ducting, brackets, and housings. These parts require high precision and accuracy, and the F900 has proven to be a reliable and cost-effective solution for their manufacturing. Additionally, the F900 has been used in other industries, such as automotive, defense, and medical, where the demand for high-performance parts is also high.The latest development in the F900 3D printer is its integration with the MTConnect protocol. MTConnect is an open-source communication protocol used in manufacturing equipment to facilitate data exchange and collection. The protocol offers a standardized way of communicating machine data, making it easier to integrate different systems and devices.With its MTConnect-ready interface, the F900 3D printer can now connect to other manufacturing systems, such as Enterprise Resource Planning (ERP) systems, Manufacturing Execution Systems (MES), and other machines in the production line. This enables better coordination between different manufacturing processes, leading to higher efficiency and productivity. Additionally, the MTConnect protocol allows for real-time monitoring of the printing process, giving operators better control and visibility over the manufacturing process.The integration of the MTConnect protocol into the F900 3D printer is a significant step towards enhancing the connectivity and data sharing capabilities of the printer. This development enables the printer to be integrated into a broader manufacturing ecosystem, allowing for seamless data exchange and coordination between different systems. This integration is highly relevant in the aerospace industry, where the demand for high-performance parts is only increasing.In conclusion, the F900 3D printer is a high-performance system designed for production applications in the aerospace industry and other high-performance industries. With its latest development, the integration of the MTConnect protocol, the printer now offers enhanced connectivity and data exchange capabilities, making it easier to integrate into a broader manufacturing ecosystem. This development ensures the F900 3D printer remains one of the leading additive manufacturing systems in the market today.