Discover the Amazing Art of Metal Bending Techniques
By:Admin
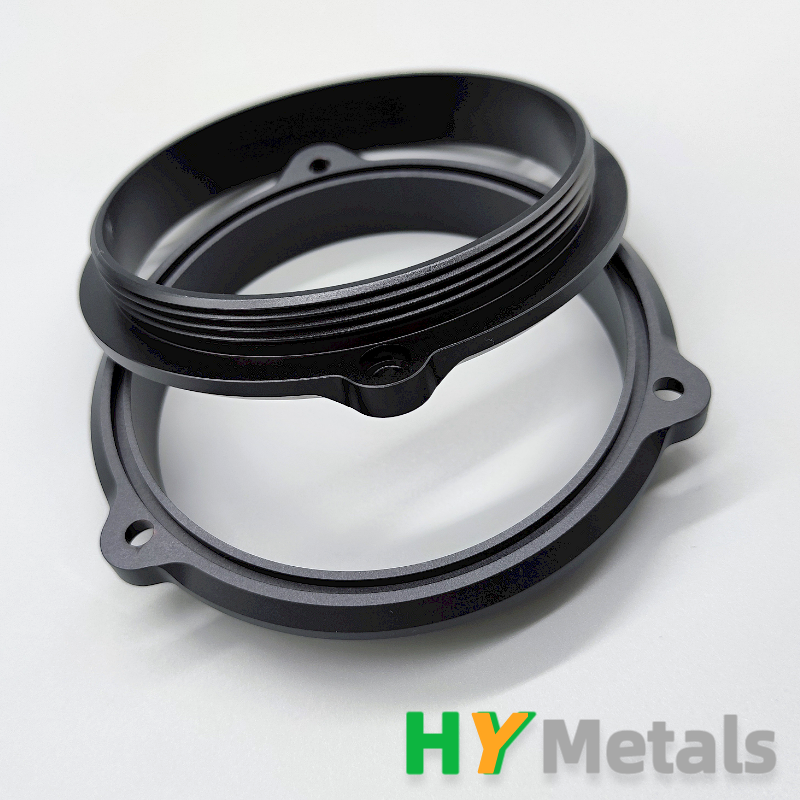
With over 20 years of experience in the industry, Metal Bending has built a reputation for excellence in metal fabrication. Their state-of-the-art facility is equipped with the latest technology and machinery, allowing them to provide a wide range of metal bending services to industries such as aerospace, automotive, construction, and more.
The new product line will further expand Metal Bending's offerings, allowing them to serve a broader range of customers and industries. The company's dedication to innovation and quality is evident in their commitment to staying at the forefront of the metal fabrication industry.
In addition to their new product line, Metal Bending also offers custom metal bending services, allowing customers to request specific designs and shapes for their projects. From simple bends to complex geometries, the company's team of highly skilled engineers and technicians can deliver precision results for any metal bending need.
Metal Bending's dedication to customer satisfaction is a driving force behind their success. The company prides itself on providing top-notch customer service, working closely with clients to understand their unique requirements and delivering solutions that meet and exceed their expectations.
Furthermore, Metal Bending is committed to sustainability and environmental responsibility. The company adheres to strict environmental regulations and utilizes eco-friendly practices in their operations. They also strive to minimize waste and optimize energy efficiency in their manufacturing processes.
As Metal Bending continues to grow and expand its product offerings, the company remains dedicated to maintaining its core values of integrity, quality, and innovation. With a focus on delivering exceptional results and exceeding customer expectations, Metal Bending is poised to continue its leadership in the metal fabrication industry.
The company's dedication to excellence has earned them a loyal customer base and a strong reputation in the industry. Metal Bending's products and services are trusted by businesses across various sectors, and their new product line is anticipated to further solidify their position as a go-to source for all metal bending needs.
As the demand for metal fabrication services continues to grow, Metal Bending is well-positioned to meet the needs of diverse industries with their unmatched expertise and commitment to quality. The company's new product line is a testament to their ongoing dedication to innovation and customer satisfaction, and it is sure to make a significant impact in the metal fabrication industry.
With a proven track record of success and a forward-thinking approach to business, Metal Bending is set to continue its impressive growth and maintain its position as a leader in the metal fabrication industry. The company's new product line is an exciting development that speaks to their ongoing commitment to excellence and innovation, and it is sure to be well-received by their customers.
Company News & Blog
Get High-Quality CNC Automation Parts for Improved Efficiency and Precision
CNC Automation Solutions' Revolutionary New Parts Drive Improved Efficiency and Precision in ManufacturingCNC Automation Solutions is proud to announce the release of its latest CNC automation parts. After years of research and development, our team of engineers has created an innovative and cutting-edge solution that promises to drive unparalleled levels of efficiency and precision within the manufacturing industry.Our latest CNC automation parts have been designed to cater to the specific needs of the manufacturing industry, by integrating leading-edge technology and incorporating the latest industry standards. Our parts are custom-designed to offer exceptional speed, precision, and reliability, catering to a broad range of manufacturing processes. With our parts, manufacturers can produce high-quality products within a precise timeline without compromising on quality.In a statement, the CEO of CNC Automation Solutions, said, "We are delighted to bring our innovative and state-of-the-art CNC automation parts to the manufacturing sector. Our team of engineers has been working tirelessly to create a solution that maximizes efficiency while eliminating the risk of human error, leading to outstanding results. Our parts are designed to meet and exceed industry standards, and we are confident that they will be highly sought after by the manufacturing community."CNC Automation Solutions has built a name for itself by delivering innovative solutions that cater to the specific needs of the manufacturing industry. Our industry expertise, coupled with our commitment to providing excellent customer service, make us the go-to company when seeking automation solutions. Our revolutionary new parts are no exception, as they provide exceptional value to our customers. By reducing the time required for set-up and changeover, with parts that are adaptable to different kinds of equipment, our parts improve overall process efficiency, as manufacturers can produce more baskets with a lesser amount of resources and time.Our latest CNC automation parts are the result of years of collaboration and development. They incorporate advanced features like cutting-edge software, modular and scalable designs, and high-quality materials that lead to improved precision and accuracy. Our parts are highly customizable, and we work closely with our clients to ensure that our products are precisely tailored to their specific needs. Whether a manufacturer is operating a small workshop or a large-scale factory, our parts are designed to cater to all kinds of operations. This adaptability allows for greater flexibility, enabling manufacturers to scale their businesses with ease.Perhaps the biggest advantage of our parts is that they help minimize the risk of human error. Traditional manufacturing methods are prone to errors due to inaccuracy that could have an adverse impact on overall efficiency. However, with our automated parts, manufacturers no longer have to worry about such errors. This advantage translates to better product quality, a lessened need for manual labor, and ultimately a significant reduction in production costs.In conclusion, CNC Automation Solutions' latest CNC automation parts represent a significant step forward in the manufacturing industry. These innovative products are set to revolutionize the world of manufacturing, promising unparalleled levels of efficiency and precision. Our parts are designed to increase productivity, reduce costs, and minimize the risk of human error. We are confident that our new parts will be warmly embraced by the manufacturing community and look forward to working with our clients, to provide them with a solution that will have a tangible impact on their businesses.
High Aspect Ratio BGA Heat Sinks: Perfect for Small PCB Spaces
article on the benefits of using BGA High Aspect Ratio Extruded heat sinks in thermal management applications.As electronic devices continue to become more compact, thermal management becomes a crucial aspect to ensure their continuous and reliable operation. To address this challenge, BGA High Aspect Ratio Extruded heat sinks have emerged as a reliable thermal management solution that delivers high performance in compact PCB environments.BGA High Aspect Ratio Extruded heat sinks are designed with a high aspect ratio or length-to-width ratio, which allows for optimal placement of fins, maximizing heat dissipation while maintaining a small footprint. The fins also provide an increased surface area, allowing for more efficient heat transfer, resulting in improved thermal performance.The use of BGA High Aspect Ratio Extruded heat sinks has many benefits. These heat sinks are ideal for compact PCB environments where space is at a premium and traditional heat sinks cannot fit without compromising other critical components. They are suitable for use in a wide range of electronic devices, including routers, switches, amplifiers, power supplies, and more.One of the main advantages of using BGA High Aspect Ratio Extruded heat sinks is their ability to dissipate heat efficiently. These heat sinks have a high aspect ratio, which means that they have a longer distance or length than the width, allowing more fins to be accommodated, providing greater surface area for heat dissipation. The more fins a heat sink has, the more efficient it is in dissipating heat.Moreover, the fins of the BGA High Aspect Ratio Extruded heat sinks are designed in such a way that they promote convective heat transfer, which results in faster and more efficient heat dissipation. With convective heat transfer, hot air moves away from the heat sink and cool air moves in, leading to a continuous cycle of thermal management.Another benefit of BGA High Aspect Ratio Extruded heat sinks is their ability to accommodate a wide range of thermal requirements. These heat sinks are available in different shapes, sizes, and configurations to suit various thermal performance requirements.In addition to their versatile size range, BGA High Aspect Ratio Extruded heat sinks are also available in different materials. Aluminum is a common material used in the fabrication of heat sinks as it is lightweight, durable, and has excellent thermal conductivity. Other materials, such as copper, can also be used for specific applications.BGA High Aspect Ratio Extruded heat sinks also have a longer lifespan when compared to other thermal management solutions. They are designed to withstand high temperatures and thermal cycles, ensuring that they can deliver optimal heat dissipation for extended periods. Overall, the use of BGA High Aspect Ratio Extruded heat sinks provides several advantages over traditional thermal management solutions. They are efficient, versatile, and reliable, making them an ideal choice for various applications where optimizing thermal performance in compact spaces is critical.In summary, BGA High Aspect Ratio Extruded heat sinks offer many benefits in thermal management applications. They maximize heat dissipation through convective heat transfer, accommodate a wide range of thermal requirements, and have a longer lifespan, and provide an optimal solution for compact spaces. As such, they are an excellent choice for electronic devices that require reliable and efficient thermal management.
Get the Best Wire Forming Machines for Sale in Melbourne - Top-notch Jigs and Templates Available!
Wire forming is a process that involves the shaping and molding of metal wires into different shapes. This process is used in a variety of industries from manufacturing to construction, and it plays an important role in the production of many different products. In this blog post, we will explore wire forming and why it's an essential process in many industries.Wire forming machinesWire forming machines are a critical tool in the wire forming process. These machines are designed to produce wire forms quickly and efficiently with precision. There are several types of wire forming machines available, including hydraulic and mechanical machines. These machines are capable of forming a range of materials, including brass, aluminum, and steel.The best wire forming machines should be easy to use, have precision controls, and offer versatility. They should also have a compact construction, making them suitable for use in small manufacturing facilities. Additionally, they should be built with durable materials that can withstand the constant wear and tear of the manufacturing process.In addition to wire forming machines, jigs and templates are commonly used in the wire forming process. These tools offer consistent and accurate wire forming results, which can increase production efficiency. They also help maintain product conformity, which is essential in industries where safety and quality are major concerns.Wire forming applicationsWire forming is a versatile process that can be used to create a vast array of products. Some of the most common applications of wire forming include:- Springs- Hooks- Wire baskets- Shelving- Clips- Hangers- Wire formsWire forming is also used in the creation of more complex products, such as automotive parts, medical devices, and electrical components. Wire forming is an important process that contributes to the safety, durability, and functionality of many everyday products.Finding a wire forming providerWhen selecting a wire forming provider, it's essential to consider several factors. Firstly, you should evaluate the provider's experience in wire forming and their track record in producing quality products. A provider that has been in the wire forming industry for many years will have a wealth of knowledge and experience. They will also have a proven track record of producing high-quality wire forms.Secondly, you should consider the provider's equipment and manufacturing facilities. Do they use the latest wire forming technology? Do they have the capacity to produce large volumes of wire forms? Choosing a provider with modern equipment and state-of-the-art facilities can help ensure that your wire forms are produced efficiently and accurately.Finally, you should consider the provider's customer service. Are they responsive and easy to work with? Do they offer technical support and guidance throughout the wire forming process? A wire forming provider with excellent customer service can make a significant difference in the success of your project.ConclusionWire forming is a crucial process in many industries, from manufacturing to construction. It allows manufacturers to create complex wire forms for use in a variety of different applications. Choosing the right wire forming provider is essential to ensure that your wire forms are produced accurately, efficiently, and to meet your specific needs. When selecting a wire forming provider, consider their experience, equipment, facilities, and customer service to ensure that you receive high-quality wire forms that meet your expectations.
Sheet Metal Bending Tools: Dies, Press Brakes, Tube & Wire Bending
Sheet metal bending is a process that involves creating a bend in a metal sheet to give it a certain shape or form. This process is done using specialized tools and equipment such as bending dies, press brakes, and tube & wire bending machines.Bending dies are the main tool used for sheet metal bending. They are used to apply force to the metal to create a bend. These dies come in different shapes and sizes depending on the shape and size of the bend required. The dies can be used with a stamping press or press brakes.Stamping presses are machines that are used to apply pressure to the metal sheet to create the desired shape. The press brake is another machine that is used for sheet metal bending. It is a large machine that uses a hydraulic system to apply force to the metal sheet. The press brake can create several bends in the metal sheet at once.There are several types of bending dies that can be used for sheet metal bending. The most common type of bending die is the progressive bending die. This die allows multiple bends to be created simultaneously, which makes the process faster and more efficient. Other types of bending dies include the wiping die, rotary die, and the air-bending die.Wire bending machines are used to create bends in wire or rod-shaped materials. These machines use specialized dies to create precise bends in the wire. The bending process is done using a combination of force and heat to create the desired shape.Tube bending machines are used for creating bends in tubes and pipes. These machines use mandrels and dies to create precise bends in the tube. The mandrel is a rod that is placed inside the tube to prevent it from collapsing during the bending process.When it comes to sheet metal bending, it is important to use the right tools and equipment to ensure that the sheet metal is bent correctly. Bending dies and tools are crucial in this process. With the right tools and equipment, it is possible to create precise bends that will meet the desired requirements.In conclusion, sheet metal bending is a complex process that requires specialized tools and equipment like bending dies, press brakes, tube & wire bending machines. Each of these pieces of equipment plays a crucial role in the bending process and is designed to create precise bends. When used correctly, these tools can help you achieve the desired shape and form for your sheet metal project.
Precision Machined Parts for Aerospace Industry
Machined Aerospace Parts plays a critical role in the aviation industry. The leading company has a longstanding reputation for providing high-quality aviation components to airlines and aircraft manufacturers. It boasts a significant market share in the aerospace industry and prides itself on a variety of CNC machining capabilities to deliver exceptional results.The company's proven track record of delivering parts that meet military and commercial aviation standards has made it a trusted supplier in the aviation industry. Customers who partner with Machined Aerospace Parts appreciate the company's focus on innovation, quality, and superior customer service. These are the essential qualities that have propelled the company to the top of the industry.Machined Aerospace Parts' capabilities are vast and diversified to meet the constantly evolving needs of the industry. The company has an array of precision equipment and utilizes the latest tools and technologies to produce a range of components. Whether it's machining parts from solid materials, producing small or large components, or creating complex structures, Machined Aerospace Parts has the expertise to get the job done.The company has a team of highly skilled professionals who are experts in the field of aviation. From engineers to production managers, all staff members are deeply passionate about the industry and take pride in their work. The team is focused on creating efficient, cost-effective solutions that meet customers' unique needs.One of the reasons Machined Aerospace Parts is a preferred supplier in the aviation industry is due to its exceptional quality control process. The company ensures that every component is subject to rigorous testing to meet the strict standards of the industry. The quality control process begins with design reviews and ends with a final inspection of finished products. These stringent checks ensure that all parts meet exacting requirements, and nothing leaves the factory until it meets the company's high standards.Machined Aerospace Parts is committed to continuous improvement, and that includes investing in cutting-edge technology and equipment. The company recently added several new machines to its assembly line, expanding its CNC machining capabilities. The machines allow the company to operate faster, which ensures quicker lead times for customers.Despite the challenges posed by the COVID-19 pandemic, Machined Aerospace Parts has continued to thrive. It has remained committed to serving its customers' needs and has adapted well to the changing landscape. The company maintains safe working conditions and adheres to all regulations and health guidelines to ensure the safety of employees and customers.As a company committed to excellence, Machined Aerospace Parts invests significantly in its people. The company has a rigorous training program that ensures all staff members are up-to-date on the latest industry developments and are equipped with the skills necessary to meet customers' needs. The company also offers training and apprenticeships to young people who want to learn about the aviation industry. By investing in young talent, the company is securing the future of the industry.In conclusion, Machined Aerospace Parts is a well-established, reputable, and innovative aviation company. With its advanced technology, highly skilled workforce, and exceptional quality control, it is no surprise that it continues to succeed in the industry. The company's commitment to providing cost-effective, efficient solutions to customers has propelled it to the top of the industry, and it remains a preferred supplier for many airlines and aircraft manufacturers. In a constantly evolving industry, Machined Aerospace Parts is poised for growth, and its future looks exceedingly bright.
Discover the Latest News on Precision CNC Machining Parts
article:CNC Machining Parts Proves to be an Essential Resource for Precision EngineeringFor many decades, the manufacturing industry has relied on CNC machines to produce high-quality end products with a precision-level of accuracy. Among these machines, CNC Machining Parts have become a fundamental resource to aid in the production of high-performance products that meet strict manufacturing specifications. In today's competitive market, achieving success in precision engineering depends on having access to the latest cutting-edge technology. This is where CNC Machining Parts come in, proving to be an essential resource that has transformed the manufacturing industry, providing a step up in the production of the highest-grade products.CNC Machining Parts are CNC-machined components that have been specifically designed to meet the stringent demands of various industries. They are produced to the most exacting standards of quality and durability, ensuring that they offer the best performance under tough and demanding circumstances. These parts are made from high-quality materials like metals, plastics, and composites that ensure that they can withstand the pressures of modern production environments.CNC Machining Parts have been designed to operate with a high degree of precision, accuracy, and reliability. CNC machines, which produce these parts, are run by computers, delivering the highest level of control and accuracy over the manufacturing process. They are programmed to perform a series of highly precise movements that create the desired end product, guaranteeing the highest levels of quality in every component produced. The CNC production process is incredibly fast and efficient, allowing for the manufacturing of large quantities of parts in a short amount of time.The CNC Machining Parts produced by {} are some of the most sophisticated and advanced in the industry. Featuring cutting-edge technology and materials, these parts have been developed to withstand the most demanding of conditions and environments. The company's production process involves the use of state-of-the-art computer-controlled machinery. The automation of this manufacturing process ensures that each part produced is a high-quality, durable component that meets the strictest demands of the manufacturing industry.CNC Machining Parts have a broad scope of applications across a range of industries. They are used in many diverse fields such as aerospace, electronics, automotive, marine, and medical industries, to mention a few. In the aerospace industry, for instance, these parts are used in the manufacture of aircraft parts, ensuring that they are highly durable and can withstand the rigors of high-altitude flight. In the automotive industry, CNC Machining Parts are used in the production of engine components, ensuring that they are efficient and can withstand high temperatures and robust driving conditions.In the medical industry, CNC Machining Parts have become instrumental in the production of high-quality medical devices and equipment. These machines produce precision components for use in surgical instruments, prosthetics, hearing aids, and other medical devices that require precise measurements. The efficiency of CNC Machining Parts has made the production of these components more accessible, cheaper, and faster, thereby improving the medical industry's level of quality.CNC Machining Parts have become essential in modern-day manufacturing. They have transformed the way manufacturing is done, offering higher levels of precision, reliability, and consistency, resulting in better-performing products. The CNC Machining Parts produced by {} are some of the best in the business and come highly recommended by satisfied customers. The company's emphasis on quality, value, and customer service has made them a leader in the industry. By utilizing cutting-edge technology, top-quality materials, and a team of skilled engineers, the company has set itself apart from its competitors, providing superior CNC Machining Parts that meet the stringent demands of various industries.In conclusion, CNC Machining Parts have become an essential resource for precision engineering. They have revolutionized the manufacturing industry by offering the highest level of precision, accuracy, and consistency, thereby producing the highest quality products. The CNC Machining Parts produced by {} are among the best on the market, utilizing state-of-the-art technology, efficient production processes, and high-quality materials. The company's focus on quality, customer service, and innovation has made it a standout performer in the industry, providing the best products and services that meet the needs of customers around the world.
Digitally Controlled Solutions for Precise Metal Bending in Steel, Stainless Steel, and Aluminum
: How Digitally Controlled Solutions Are Revolutionizing TFE Bending ServicesSheet metal bending has been an essential part of manufacturing since the industrial revolution, but advancements in digital control have allowed for greater levels of precision and efficiency. At TFE, these cutting-edge techniques are being applied to create bespoke sheet metal bending parts of the highest quality and accuracy.In 2018, TFE invested in new bending machines with digital control capabilities, allowing them to meet the increasing requirements of their clients. These machines provide the ability to bend a range of materials including steel, stainless steel, and aluminum, and the accuracy of the multi-station bending press allows for the creation of complex geometries with ease.The use of digital control allows TFE to achieve unparalleled precision, making it possible to create parts with crushed bends or plunging without the need for further reworking. This technology also ensures exceptional repeatability, allowing for a faster turnaround time on orders.The TFE bent metal parts portfolio is comprehensive, covering angular bending, variable radius bending, and crushed bends. However, TFE's capabilities don't stop there. They have also developed innovative methods for large radius stretching, an alternative to rolling or in addition to it. This approach provides unique opportunities for niche applications that require specific shapes of sheet metal parts.TFE takes great pride in their commitment to quality, and their innovative techniques guarantee a constant level of excellence. The company's digitally controlled bending methods allow for excellent man-machine complementarity, resulting in the highest levels of efficiency and productivity.In conclusion, TFE's bending services have been transformed with the integration of digitally controlled bending machines. These advanced techniques allow for the creation of bespoke parts with exceptional levels of accuracy, repeatability, and quality. If you're in the market for sheet metal bending parts, look no further than TFE for the most innovative and precise solutions. Keywords: TFE Bending, Sheet Metal Bending Parts, Digital Control, Bending Machines, Multi-Station Bending Press, Repeatability, Angular Bending, Variable Radius Bending, Crushed Bends, Large Radius Stretching, Man-Machine Complementarity, Precision, Efficiency, Productivity.
Innovative Prototype of Next-Generation Heatsink Unveiled, Revolutionizing Cooling Technology
In the world of technology, finding ways to cool devices is an essential element in ensuring their longevity and functionality. Overheating has proven to be a significant problem, especially in more advanced computers and gaming consoles. To combat this, a company has developed a prototype heatsink that offers efficient cooling with a sleek and modern design.The heatsink prototype, which is made from high-quality materials, has been tested extensively to ensure its efficiency in cooling electronics. The prototype has been developed with an eye towards aesthetics by featuring an attractive, modern design that emphasizes functionality, with a sleek black finish that will complement any computer or gaming console.According to representatives from the company, this heatsink prototype utilizes a unique combination of materials, including aluminum, copper, and nickel. These materials help to create an efficient cooling solution that will drastically reduce the risk of overheating, enabling users to work on their devices without fear of hardware malfunction.The company behind this innovative product is a leading manufacturer of computer and gaming peripherals. With years of experience and dedication, they have gained a reputation for producing high-quality products that address the needs of tech enthusiasts and professionals alike.The company has a range of computer and gaming peripherals, including headphones, keyboards, and monitors, among others. The company has attained the trust of many users due to their ability to produce innovative and reliable products consistently.The prototype of the heatsink has been developed as a part of the company's commitment to research and development. The company stated that by investing in R&D, they could remain innovative and remain committed to developing products that meet the evolving needs of their customers.The heatsink prototype is a testament to the company’s ability to create products that are both innovative and functional while meeting consumers' needs. The company's focus on aesthetics has ensured that the heatsink is not just efficient but is also visually appealing, adding an element of style to the user's computer or gaming setup.Additionally, the heatsink's materials have been carefully selected to ensure that it is durable and long-lasting, a critical factor for computer or gaming enthusiasts who invest in high-end devices that need reliable cooling solutions.The company mentioned that the prototype is currently being tested on numerous devices. The testing process is conducted under various conditions and represents real-life scenarios to ensure the heatsink provides optimal cooling results in various environments. The company is committed to ensuring that customers receive the best product by putting the finished product through rigorous testing procedures.The heatsink prototype's benefits cannot be overstated as it solves a significant problem for the technology industry while also providing a product that is both functional and aesthetically pleasing. The product's development showcases the company's commitment to innovation, investing time and money to offer sophisticated solutions to consumers' problems.While the heatsink prototype is still undergoing testing, the company aims to release the product soon. As demand for heat sinking solutions increases, the company is well-positioned to meet consumer needs. The company has assured its customers that upon the product's release, it will be widely available globally, making it easy for consumers to access the innovative product regardless of their location.In conclusion, the company that has developed the prototype heatsink is on the path to revolutionizing the cooling solutions industry. The company's commitment to researching and developing innovative products has enabled them to address the needs of computer and gaming enthusiasts successfully. As technology continues to evolve, the company seems adequately positioned to be at the forefront of offering sophisticated solutions to users. Customers eagerly wait for the release of the heatsink prototype, which promises excellent functionality and aesthetics.
3-Axis Milling Machine for Versatile Applications in Die and Mold Construction
Milling Precision Parts: Achieving Unparalleled Accuracy and Versatility with Universal Milling MachinesMilling machines are used extensively in a wide range of industrial applications to create precision parts with high accuracy and efficiency. With the advent of advanced technology and innovative engineering, milling machines have become much more versatile and capable of performing a wide range of functions. Among the most versatile of all milling machines in the market today are the 3-axis universal milling machines.Here, we will highlight the Milling machine | 3 axis | MILL E Series – a universal application offered by GF Machining Solutions. The range of HEM vertical machining center sets standards in the VMC category, and the VCE range is ideally suited for die and mold construction using a round-head cutter.The Mill E series milling machines are highly sophisticated and versatile machines capable of performing a diverse range of functions. They can create precision parts of various sizes to meet the demands of different industries, from aerospace and defense to automotive and medical.What sets the Mill E series apart from other milling machines in the market is its unique design and engineering. It features a 3-axis system that offers unparalleled accuracy and versatility, making it perfect for a range of applications. Additionally, the Mill E series is built to withstand the rigors of industrial use, ensuring reliable and precise performance.One of the main benefits of using the Mill E series milling machines is their ability to reduce production time while increasing output. The fast and precise movement of the spindle head enables them to create complex parts with high accuracy, reducing the need for manual labor and enhancing overall productivity.Moreover, the Mill E series machines are designed with user-friendliness in mind, with intuitive software and user interfaces that enable easy operation of the machines. With these machines, operators can create complex parts with ease, and the machines can be easily customized to suit the demands of different applications.The VCE range of milling machines also makes use of advanced technology and innovative engineering to offer unparalleled performance. These machines are designed to work exclusively with round head cutters, making them ideal for die and mold construction. They are built to provide high precision and repeatability during the machining process, ensuring consistent results every time.One of the main advantages of the VCE range of milling machines is their ability to perform smoothing operations on complex surfaces of molds and dies. Smoothing the surfaces of molds and dies is a critical part of the manufacturing process, as it ensures high-quality parts that are free of blemishes and imperfections.In conclusion, milling precision parts requires high accuracy, precision, and versatility, which is why the Mill E series and VCE range milling machines are ideal for any industrial application. With their ability to create complex parts with precision and accuracy, these machines are the perfect choice for industries that require high-quality parts with tight tolerances. The use of these machines not only enhances productivity but also helps to reduce production costs, making them a valuable addition to any manufacturing facility. If you are searching for a reliable and efficient milling machine to create precision parts, look no further than the Mill E series and VCE range of milling machines.
Ultimate Guide to Sheet Metal Forming Techniques for Manufacturing
article about the advancements in sheet metal forming technology.Sheet metal forming is a process used to transform flat metal sheets into various shapes and products through the application of force. This process is widely used in industries such as automotive, aerospace, construction, and manufacturing to create a wide range of products including car parts, machinery components, and household appliances.In recent years, there have been significant advancements in sheet metal forming technology that have led to improvements in efficiency, precision, and overall product quality. One company at the forefront of these advancements is {}.{} is a leading manufacturer of sheet metal forming equipment and has been instrumental in driving innovation in the industry. With a strong focus on research and development, the company has developed cutting-edge technologies that have revolutionized the sheet metal forming process.One of the key advancements that {} has introduced is the use of advanced computer-aided design (CAD) and computer-aided manufacturing (CAM) software to optimize the sheet metal forming process. This software allows manufacturers to create highly detailed and precise designs, which are then used to program the company's state-of-the-art sheet metal forming machines.In addition to software advancements, {} has also developed new techniques for controlling the temperature and pressure during the sheet metal forming process. These techniques have resulted in a more consistent and uniform shaping of the metal, leading to products with higher quality and durability.Furthermore, {} has invested heavily in automation and robotics to streamline the sheet metal forming process. By automating certain tasks, the company has been able to increase production speed and efficiency while reducing the margin of error.The advancements made by {} have not only improved the efficiency and precision of the sheet metal forming process, but they have also had a positive impact on sustainability. By optimizing the process and reducing waste, the company has been able to minimize its environmental footprint.In addition to technological advancements, {} has also focused on the training and development of its workforce. The company has a team of highly skilled engineers and technicians who are constantly pushing the boundaries of what is possible in sheet metal forming.Through their dedication to innovation and excellence, {} has solidified its position as a global leader in the sheet metal forming industry. The company's commitment to pushing the boundaries of what is possible has led to advancements that have transformed the industry and set new standards for quality and efficiency.Looking ahead, {} continues to invest in research and development to further advance sheet metal forming technology. With a focus on sustainability, efficiency, and precision, the company is poised to continue leading the way in the sheet metal forming industry.In conclusion, the advancements made by {} in sheet metal forming technology have had a profound impact on the industry. Through a combination of advanced software, temperature and pressure control techniques, automation, and a focus on sustainability, the company has raised the bar for efficiency, precision, and product quality in sheet metal forming. As {} continues to push the boundaries of what is possible, the future of sheet metal forming looks promising, with even more advancements on the horizon.