- Home
- Blog
- Digitally Controlled Solutions for Precise Metal Bending in Steel, Stainless Steel, and Aluminum
Digitally Controlled Solutions for Precise Metal Bending in Steel, Stainless Steel, and Aluminum
By:Admin
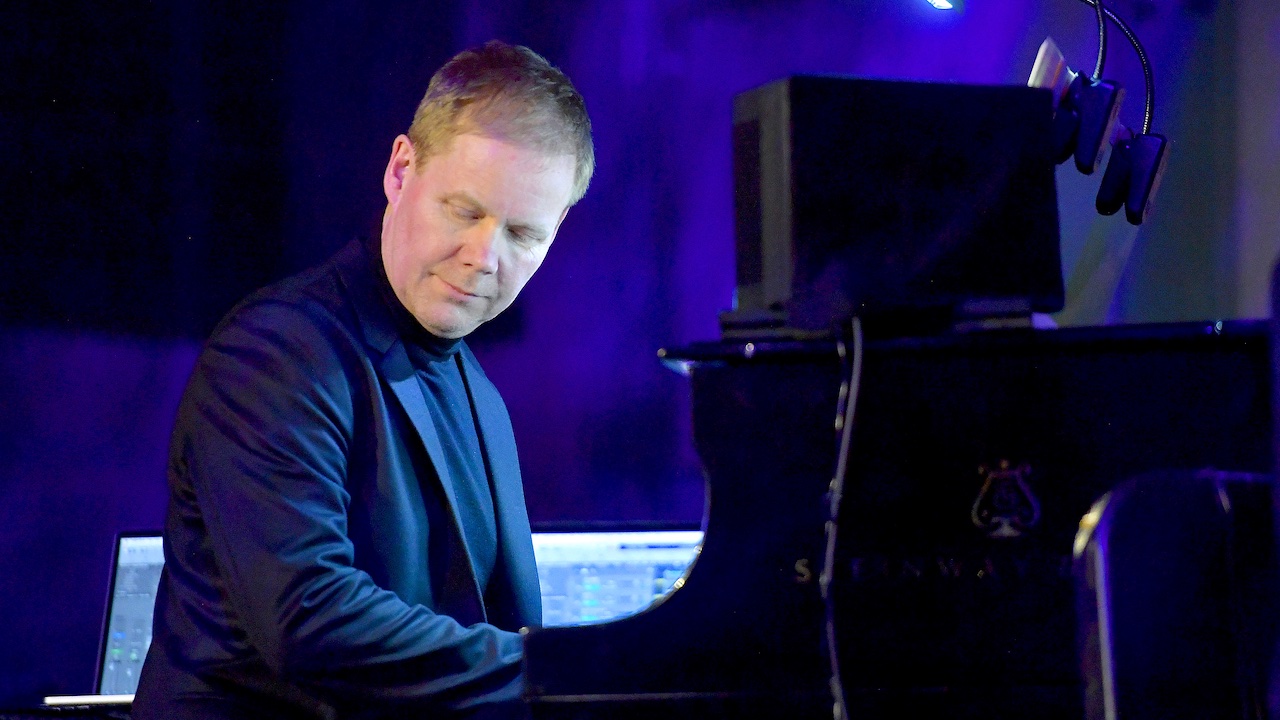
Sheet metal bending has been an essential part of manufacturing since the industrial revolution, but advancements in digital control have allowed for greater levels of precision and efficiency. At TFE, these cutting-edge techniques are being applied to create bespoke sheet metal bending parts of the highest quality and accuracy.
In 2018, TFE invested in new bending machines with digital control capabilities, allowing them to meet the increasing requirements of their clients. These machines provide the ability to bend a range of materials including steel, stainless steel, and aluminum, and the accuracy of the multi-station bending press allows for the creation of complex geometries with ease.
The use of digital control allows TFE to achieve unparalleled precision, making it possible to create parts with crushed bends or plunging without the need for further reworking. This technology also ensures exceptional repeatability, allowing for a faster turnaround time on orders.
The TFE bent metal parts portfolio is comprehensive, covering angular bending, variable radius bending, and crushed bends. However, TFE's capabilities don't stop there. They have also developed innovative methods for large radius stretching, an alternative to rolling or in addition to it. This approach provides unique opportunities for niche applications that require specific shapes of sheet metal parts.
TFE takes great pride in their commitment to quality, and their innovative techniques guarantee a constant level of excellence. The company's digitally controlled bending methods allow for excellent man-machine complementarity, resulting in the highest levels of efficiency and productivity.
In conclusion, TFE's bending services have been transformed with the integration of digitally controlled bending machines. These advanced techniques allow for the creation of bespoke parts with exceptional levels of accuracy, repeatability, and quality. If you're in the market for sheet metal bending parts, look no further than TFE for the most innovative and precise solutions.
Keywords: TFE Bending, Sheet Metal Bending Parts, Digital Control, Bending Machines, Multi-Station Bending Press, Repeatability, Angular Bending, Variable Radius Bending, Crushed Bends, Large Radius Stretching, Man-Machine Complementarity, Precision, Efficiency, Productivity.
Company News & Blog
Expert Thermal Management Consulting for High Performance Electronics
In the world of electronics, thermal management is one of the most important factors that can make or break the success of a product. When electronic circuits run, they generate heat, and if this heat is not properly dissipated, it can cause a range of problems, from degraded performance to component failure. This is where thermal management solutions come in, and Q ATS is a leading provider of such solutions.Founded with the aim of helping electronic product manufacturers bring their products to market faster, safer, and at a lower cost, Q ATS has established itself as a trusted partner for companies in a variety of industries. Whether it's designing a custom heatsink for a high-power LED light or analyzing the thermal performance of a data center, Q ATS has the expertise and experience to help clients solve their thermal management challenges.One of the key advantages of working with Q ATS is their comprehensive approach to thermal management analysis and design. Rather than simply offering off-the-shelf solutions, their team of engineers work closely with clients to understand the unique requirements of their products and design custom solutions that meet those needs. This ensures that clients get the best possible thermal performance for their products, while minimizing costs and time-to-market.Some of the services offered by Q ATS include thermal modeling and simulation, which allows them to predict the thermal performance of a product before it's even built. This can be especially valuable in applications where thermal management is critical, such as aerospace and defense. Q ATS also offers design and prototyping services, allowing clients to test and iterate on their thermal management solutions before committing to production.Another key area of expertise for Q ATS is the design and manufacture of heatsinks, which are a critical component in many electronic products. Heatsinks are used to dissipate heat from a component or circuit board to the surrounding air, and Q ATS can design heatsinks that are optimized for a specific application, providing maximum performance while minimizing weight and cost.In addition to their technical expertise, Q ATS is also committed to providing exceptional customer service. They work closely with clients throughout every stage of the project, from initial consultation to final delivery, ensuring that their needs are fully understood and met. Their team is highly responsive, with quick turnaround times and a willingness to go the extra mile to ensure client satisfaction.Overall, Q ATS is a valuable partner for any company looking to improve the thermal performance of their electronic products. With their comprehensive approach, technical expertise, and commitment to customer service, they can help clients get their products to market faster, safer, and more cost-effectively than ever before.
Sheet Metal Bending Tools: Dies, Press Brakes, Tube & Wire Bending
Sheet metal bending is a process that involves creating a bend in a metal sheet to give it a certain shape or form. This process is done using specialized tools and equipment such as bending dies, press brakes, and tube & wire bending machines.Bending dies are the main tool used for sheet metal bending. They are used to apply force to the metal to create a bend. These dies come in different shapes and sizes depending on the shape and size of the bend required. The dies can be used with a stamping press or press brakes.Stamping presses are machines that are used to apply pressure to the metal sheet to create the desired shape. The press brake is another machine that is used for sheet metal bending. It is a large machine that uses a hydraulic system to apply force to the metal sheet. The press brake can create several bends in the metal sheet at once.There are several types of bending dies that can be used for sheet metal bending. The most common type of bending die is the progressive bending die. This die allows multiple bends to be created simultaneously, which makes the process faster and more efficient. Other types of bending dies include the wiping die, rotary die, and the air-bending die.Wire bending machines are used to create bends in wire or rod-shaped materials. These machines use specialized dies to create precise bends in the wire. The bending process is done using a combination of force and heat to create the desired shape.Tube bending machines are used for creating bends in tubes and pipes. These machines use mandrels and dies to create precise bends in the tube. The mandrel is a rod that is placed inside the tube to prevent it from collapsing during the bending process.When it comes to sheet metal bending, it is important to use the right tools and equipment to ensure that the sheet metal is bent correctly. Bending dies and tools are crucial in this process. With the right tools and equipment, it is possible to create precise bends that will meet the desired requirements.In conclusion, sheet metal bending is a complex process that requires specialized tools and equipment like bending dies, press brakes, tube & wire bending machines. Each of these pieces of equipment plays a crucial role in the bending process and is designed to create precise bends. When used correctly, these tools can help you achieve the desired shape and form for your sheet metal project.
High-Quality Lathe Parts for a Perfect Fit Every Time - Installation Guides and Manuals Available
Sears PartsDirect Now Offers Top-Quality Lathe Parts for All Major Lathe BrandsSears PartsDirect is excited to announce that we are now offering a wide selection of lathe parts for all major lathe brands, ensuring that our customers can find the best-quality parts they need to keep their lathes running smoothly. Our manufacturer-approved lathe parts are designed to provide a proper fit every time, giving our customers the assurance that their machines will be restored to optimal performance with ease.Lathe machines are an essential component of many industrial processes, and often need to be repaired and maintained in order to keep them functioning as designed. That’s where Sears PartsDirect comes in – we are committed to making it easy for our customers to find the parts they need to keep their machines running smoothly.We understand that different machines have different requirements, which is why we have a large selection of lathe parts available to suit all needs. Whether it is a specialized replacement part, an upgrade or a general maintenance part, our customers can be sure that they will find what they need.Our experienced team is dedicated to helping our customers find the right parts for their machines, and we are always on hand to answer any questions or concerns they may have. Our online catalogues are easy to navigate, and we provide detailed specifications and information about each part to make it easy for our customers to find what they need.In addition to our extensive selection of lathe parts, we also offer installation guides, diagrams, and manuals to help our customers along the way. Our guides and manuals are designed to provide a step-by-step approach to repairs and maintenance, ensuring that our customers can complete the job quickly and efficiently.At Sears PartsDirect, we are committed to providing our customers with the highest quality service and products possible. Our team of experts works diligently to ensure that our customers can find the parts they need, and our dedicated support team is always available to assist them with their needs.Our commitment to quality is reflected in our manufacturer-approved parts, which are designed to meet the highest standards for performance and reliability. We are proud to offer our customers the best in the industry, and we look forward to continuing to provide top-quality parts and support for all major lathe brands.In conclusion, Sears PartsDirect is excited to announce that we are now offering a wide selection of lathe parts for all major lathe brands. Our commitment to quality and service sets us apart from the competition, and we are dedicated to providing our customers with the best possible experience. With our extensive selection of parts, expert guidance, and exceptional customer support, we are confident that we can help our customers keep their lathes running smoothly and efficiently for years to come.
Metal Sheet Cutting, Punching, Pressing and Binding Services
release:DOMEX Offers Comprehensive Sheet Metal Processing Solutions with State-of-the-Art EquipmentDOMEX, a leader in sheet metal processing, offers a comprehensive range of services that include cutting, punching, pressing, and binding of metal sheets. The company has a state-of-the-art facility equipped with modern mechanical and hydraulic presses, and a range of other equipment, making it possible to handle even complex and challenging sheet metal projects.With more than two decades of experience in the industry, DOMEX has earned a reputation for excellence in sheet metal processing and fabrication. One of the key factors behind its success is the company's focus on quality, precision, and timely delivery of projects. This is supported by their well-trained and experienced staff, who are committed to ensuring every project meets customer expectations.One of the core services offered by DOMEX is metal sheet cutting. The company has invested in the latest hydraulic guillotine shears, which can cut through even the thickest sheets of metal with ease. This equipment is ideal for cutting material for a wide range of industries, including construction, architecture, and manufacturing. Furthermore, the shears provide an impeccable level of precision and accuracy, ensuring that every cut is clean and straight.DOMEX also has an array of mechanical and hydraulic presses that can handle different metal sheet processing needs. Each press has varying pressure power levels and dimensions of working tables, making it possible for the company to provide a range of custom metal fabrication services. These include stamping, deep drawing, bending, and flanging, among others. These metal shaping processes are important in the manufacturing of products in many industries, such as automotive, aerospace, and medical devices.Quality is a top priority at DOMEX, and the company has a stringent quality control process in place to ensure that every project meets exacting standards. Their team of skilled technicians use advanced measuring equipment to check and double-check every aspect of a project before it is allowed to leave the facility. From first cut to final assembly, every step of the metal processing project is carefully monitored and inspected to ensure every component meets customer requirements.DOMEX is also committed to sustainability and environmental responsibility. They use only eco-friendly materials, and their state-of-the-art equipment has been designed to reduce waste and energy consumption. Additionally, the company strives to make sure their metal fabrication processes are as efficient as possible, reducing the use of resources and minimizing the environmental impact of their operations.With its knowledgeable staff, cutting-edge equipment, and commitment to quality and sustainability, DOMEX is a trusted partner for businesses looking for reliable sheet metal processing services. The company's services are ideal for those in the construction, architecture, manufacturing, and other related industries who require top-quality, precision sheet metal fabrication. In conclusion, DOMEX remains a leader in the sheet metal processing industry, and their commitment to excellence and sustainability sets them apart from the competition. Whether cutting, punching, pressing, or binding metal sheets, the company ensures that every project is completed to the highest standards, on time and within budget.
Production-Grade 3D Printer Enables MTConnect Integration for Aerospace and Industrial Applications
, F900 3D printer, production applications, aerospace industry, MTConnect protocol.Additive manufacturing has revolutionized the manufacturing industry with the ability to create complex geometries with high precision and speed. One of the leading players in the additive manufacturing market is the F900 3D printer, designed for production applications in the aerospace industry and other high-performance industries. This blog discusses the latest development in the F900 3D printer, which now features an MTConnect-ready interface, offering enhanced connectivity and data exchange capabilities.The F900 3D printer is known for its high-performance capabilities, reliability, and large-scale printing. The printer uses the Fused Deposition Modeling (FDM) technology, which involves building 3D models layer by layer by depositing material in a melted state. The FDM technology provides a high degree of design flexibility, allowing the production of complex geometries without the need for additional machining or assembly processes.The F900 3D printer has been widely used in the aerospace industry for the production of complex parts, such as ducting, brackets, and housings. These parts require high precision and accuracy, and the F900 has proven to be a reliable and cost-effective solution for their manufacturing. Additionally, the F900 has been used in other industries, such as automotive, defense, and medical, where the demand for high-performance parts is also high.The latest development in the F900 3D printer is its integration with the MTConnect protocol. MTConnect is an open-source communication protocol used in manufacturing equipment to facilitate data exchange and collection. The protocol offers a standardized way of communicating machine data, making it easier to integrate different systems and devices.With its MTConnect-ready interface, the F900 3D printer can now connect to other manufacturing systems, such as Enterprise Resource Planning (ERP) systems, Manufacturing Execution Systems (MES), and other machines in the production line. This enables better coordination between different manufacturing processes, leading to higher efficiency and productivity. Additionally, the MTConnect protocol allows for real-time monitoring of the printing process, giving operators better control and visibility over the manufacturing process.The integration of the MTConnect protocol into the F900 3D printer is a significant step towards enhancing the connectivity and data sharing capabilities of the printer. This development enables the printer to be integrated into a broader manufacturing ecosystem, allowing for seamless data exchange and coordination between different systems. This integration is highly relevant in the aerospace industry, where the demand for high-performance parts is only increasing.In conclusion, the F900 3D printer is a high-performance system designed for production applications in the aerospace industry and other high-performance industries. With its latest development, the integration of the MTConnect protocol, the printer now offers enhanced connectivity and data exchange capabilities, making it easier to integrate into a broader manufacturing ecosystem. This development ensures the F900 3D printer remains one of the leading additive manufacturing systems in the market today.
Precision CNC Machined Parts for Corn and Grain Agriculture Products – Manufacturer in China
CNC machining is a widely-used technology in various industries, including agriculture. Specifically, CNC machined parts are essential in corn and grain harvesting and processing activities. In Senorok.com, we offer precision CNC machined parts that provide outstanding performance and optimal efficiency. Our expert manufacturing team uses the latest technology and an extensive range of raw materials to produce high-quality machined parts for different industries.One of our most popular CNC machined parts is the SS-03,05 model, which is made of high-quality steel. Steel is a durable and robust material that can withstand extreme conditions, making it ideal for use in agricultural machinery. With our precise CAD/CAM techniques and cutting-edge CNC technology, we can manufacture highly accurate and precise machined parts that meet our clients' unique demands.Our CNC machined parts are available at a reasonable price, and we offer competitive rates that make us a reliable partner for different types of businesses. Our team has years of experience in delivering top-quality CNC machined parts, and we understand the importance of delivering products that match our clients' expectations.Apart from steel, we can also manufacture CNC milled plastic parts that are highly effective in various applications. Plastic parts are preferred in some cases because they are lightweight, affordable, and can be quickly produced in large volumes. Our CNC machines are optimized to work with different types of plastics, and we can provide custom-made solutions that suit our clients' requirements.In conclusion, CNC machining is an essential technology that contributes significantly to the agricultural sector. At Senorok.com, we are committed to delivering top-quality CNC machined parts that provide superior performance and durability. Our products are reliable, competitively priced, and manufactured with precision to meet our clients' unique needs. Please contact us today to learn more about our CNC machining services and how we can help your business succeed.
What is Water-jet Technology and How Does it Work?
Water-jet technology has evolved significantly over the years, providing a versatile and efficient solution for a range of industrial applications. This technology involves the use of a high-pressure pump to create a stream of water that can be used to cut, clean, and shape different materials. Water-jet technology is fast becoming the go-to option for many employers in varied industries.The process of water-jet cutting starts by using a high-pressure pump that pumps water through a nozzle, which produces a super-fast stream of water that is directed onto the material to be cut. The water pressure can be adjusted to suit the type of material being cut, from soft materials like plastic, rubber, and foam to hard materials like metals, ceramics, and glass.One of the most significant benefits of water-jet technology is its ability to perform intricate cuts without creating heat-affected zones (HAZ). Thermal distortion, discoloration, and other undesirable effects are often seen when traditional cutting methods are used, like plasm cutting. However, water-jet cutting ensures material integrity through cold cutting, making it ideal for precision machining, intricate architectural designs, medical equipment, aerospace, and automotive parts.Traditional cutting methods such as laser and plasma can produce toxic fumes or debris that can be dangerous to the environment and human health. In contrast, water-jet cutting is eco-friendly and safe. The water used in this process can be recycled and reused, and the cutting operation produces no hazardous waste, allowing companies to reduce their environmental footprint considerably.Moreover, water-jet technology requires no special tooling, which means changing between different materials and designs is a breeze. This makes water-jet cutting an even more attractive option for manufacturers who need to switch between various production requirements quickly. Additionally, with advancements in technology, 5-axis cutting technology and robotics can be utilized, allowing greater flexibility and increased accuracy in cutting, ensuring more efficient and cost-effective production.The benefits of water-jet technology are not limited to cutting and shaping applications, as it has other uses too. Water-jet cleaning is another application of this technology. It involves the use of high-pressure water streams to remove dirt and grime from surfaces, making it an effective cleaning option for many businesses. Cleaning using a water-jet is particularly useful in the food and beverage industry, where sanitation is critical.Another advantage of using water-jet technology in cleaning is that it does not require any chemicals to aid the cleaning process. This, in turn, ensures that the cleaned surfaces are safe for human consumption, eliminating the need for chemical-based cleaning agents harmful to the environment and humans. The use of water-jet technology in cleaning can significantly reduce washing times and increase production efficiency, making it an ideal solution for many businesses.In conclusion, water-jet technology presents an innovative and eco-friendly solution for many manufacturing and cleaning applications. Its benefits are unrivaled when compared to traditional cutting and cleaning technologies. From increased production efficiency to reduced environmental footprint to the ability to perform intricate and precise cuts, water-jet technology has fast become a sought-after option for many businesses looking to improve their bottom line. Companies that have not yet implemented this technology in their operations are urged to give it a try and discover the numerous cost and time-saving benefits it can offer.
Get the Best Wire Forming Machines for Sale in Melbourne - Top-notch Jigs and Templates Available!
Wire forming is a process that involves the shaping and molding of metal wires into different shapes. This process is used in a variety of industries from manufacturing to construction, and it plays an important role in the production of many different products. In this blog post, we will explore wire forming and why it's an essential process in many industries.Wire forming machinesWire forming machines are a critical tool in the wire forming process. These machines are designed to produce wire forms quickly and efficiently with precision. There are several types of wire forming machines available, including hydraulic and mechanical machines. These machines are capable of forming a range of materials, including brass, aluminum, and steel.The best wire forming machines should be easy to use, have precision controls, and offer versatility. They should also have a compact construction, making them suitable for use in small manufacturing facilities. Additionally, they should be built with durable materials that can withstand the constant wear and tear of the manufacturing process.In addition to wire forming machines, jigs and templates are commonly used in the wire forming process. These tools offer consistent and accurate wire forming results, which can increase production efficiency. They also help maintain product conformity, which is essential in industries where safety and quality are major concerns.Wire forming applicationsWire forming is a versatile process that can be used to create a vast array of products. Some of the most common applications of wire forming include:- Springs- Hooks- Wire baskets- Shelving- Clips- Hangers- Wire formsWire forming is also used in the creation of more complex products, such as automotive parts, medical devices, and electrical components. Wire forming is an important process that contributes to the safety, durability, and functionality of many everyday products.Finding a wire forming providerWhen selecting a wire forming provider, it's essential to consider several factors. Firstly, you should evaluate the provider's experience in wire forming and their track record in producing quality products. A provider that has been in the wire forming industry for many years will have a wealth of knowledge and experience. They will also have a proven track record of producing high-quality wire forms.Secondly, you should consider the provider's equipment and manufacturing facilities. Do they use the latest wire forming technology? Do they have the capacity to produce large volumes of wire forms? Choosing a provider with modern equipment and state-of-the-art facilities can help ensure that your wire forms are produced efficiently and accurately.Finally, you should consider the provider's customer service. Are they responsive and easy to work with? Do they offer technical support and guidance throughout the wire forming process? A wire forming provider with excellent customer service can make a significant difference in the success of your project.ConclusionWire forming is a crucial process in many industries, from manufacturing to construction. It allows manufacturers to create complex wire forms for use in a variety of different applications. Choosing the right wire forming provider is essential to ensure that your wire forms are produced accurately, efficiently, and to meet your specific needs. When selecting a wire forming provider, consider their experience, equipment, facilities, and customer service to ensure that you receive high-quality wire forms that meet your expectations.
Discover the Advantages of In-House Metal Fabrication for Quality and Timely Delivery
Sheet Metal Panel Fabrication – The Ultimate Solution to All Metal Fabrication NeedsSheet metal fabrication has come a long way since its inception. It has become an indispensable part of various industries and is used extensively for a multitude of purposes. Be it aerospace, automotive, construction, or any other industry – sheet metal fabrication is crucial in all of them.Although there are numerous methods of sheet metal fabrication, sheet metal panel fabrication has gained immense popularity among manufacturers. The primary reason for its popularity is the accuracy and precision it offers while fabricating metal panels.Let's delve deeper into the aspects of sheet metal panel fabrication and understand how it can help manufacturers in their metal fabrication needs.What is Sheet Metal Panel Fabrication?Sheet metal panel fabrication is a process that involves cutting, folding, and shaping sheet metal into panels. These panels can be of various shapes and sizes, and the fabrication process can be customized as per the requirement.Sheet metal panel fabrication involves using various tools such as laser cutting machines, CNC punching machines, and hydraulic press brakes. These machines are highly efficient and can provide accurate and precise output with utmost consistency.Advantages of Sheet Metal Panel Fabrication1. Precision – As stated earlier, sheet metal panel fabrication provides a high degree of precision and accuracy. The cutting and folding are done with utmost care and attention to detail, ensuring that the metal panels meet the required specifications.2. Customization – Sheet metal panel fabrication can be customized to cater to the specific needs of the manufacturer. This versatility allows manufacturers to produce metal panels of various shapes, sizes, and thicknesses. This flexibility is not present in other methods of metal fabrication.3. Efficiency – Sheet metal panel fabrication is highly efficient and can deliver output at a much quicker rate than other methods of metal fabrication. The use of advanced machines enhances the efficiency of the process, making it an ideal choice for manufacturers who want to increase their production speed.4. Cost-Effective – Sheet metal panel fabrication can be cost-effective in the long run. The high degree of precision and accuracy results in minimal wastage of material, making it a cost-effective method for manufacturers who want to cut down on their raw material costs.ConclusionSheet metal panel fabrication has become an integral part of various industries. It offers precision, customization, efficiency, and cost-effectiveness, making it the ultimate solution for all metal fabrication needs. If you want to streamline your metal fabrication process and improve your production speed, sheet metal panel fabrication is an ideal choice.So, if you are looking for a reliable metal fabrication service provider, look no further than sheet metal panel fabrication experts. They can help you with all your metal fabrication needs, ensuring that the end product meets your specifications.
CNC Turning Services for High-Quality Lathe Turned Parts
Service, Lathe Turned Production Parts, Prototyping, CNC Machined Parts, Manufacturing Partners, Instant CNC Turning Quote.CNC Turning Service: Your One-Stop Solution for All Your Lathe NeedsIn today's fast-paced manufacturing industry, the demand for precision and accuracy in parts production is more important than ever. Thanks to advances in technology, the CNC turning service has emerged as the go-to solution for manufacturing high-quality lathe-turned production parts. CNC Turning, with its precision, speed, and flexibility, has revolutionized the world of manufacturing and has become an essential part of modern-day production processes.At CNC Turning Service, we understand the importance of getting it right the first time, which is why we offer an exceptional range of services dedicated to providing our clients with the best possible results. Our services provide complete end-to-end solutions, from prototyping to CNC machined parts, and we deliver them with unbeatable speed, quality, and price.Our Global Network of Certified Manufacturing PartnersCNC Turning Service is proud to have a global network of 25 certified manufacturing partners, enabling us to offer our clients the best CNC turning services available. These partners have over 100 CNC turning machines, allowing us to produce everything from simple to complex parts. Our partners undergo a rigorous selection process to ensure they meet our exacting standards of quality, consistency, and efficiency. As a result, our clients benefit significantly from increased savings, faster lead times, and access to a wider range of capabilities.The Most Cost-Effective Solution for PrototypingAt CNC Turning Service, we understand that prototyping is an essential part of the production process. As such, we offer our clients the most cost-effective solution for creating high-quality prototypes. Our CNC turning service gives our clients the ability to produce prototypes that are identical to the final product in terms of specifications, tolerances, and material, which reduces the risk of design errors and allows for necessary modifications before the final production.CNC Machined Parts With Unbeatable Quality and SpeedCNC Turning Service produces CNC machined parts with unbeatable speed and quality. Our partners' CNC turning machines produce precise and accurate parts with precise tolerances, finishes, and features. Whether you need single parts or thousands, our CNC turning service can provide you with the most efficient and cost-effective production.Instant CNC Turning QuoteCNC Turning Service offers an instant CNC turning quote to our clients. Our online quote system is user-friendly, simple, and straightforward to use. Our clients can upload their designs, specify their requirements, and receive a quote instantly. With our instant quote system, our clients can access real-time pricing information and plan their production processes accordingly.ConclusionAt CNC Turning Service, we provide our clients with a complete end-to-end solution for all their lathe-turned production parts needs. Our global network of certified manufacturing partners, our cost-effective prototyping solutions, and our unbeatable quality and speed in producing CNC machined parts, make us the go-to solution for manufacturing high-quality parts. Contact us today and experience the benefits of our CNC turning services.