Top Quality Extruded Aluminum Heatsinks for Efficient Heat Dissipation
By:Admin
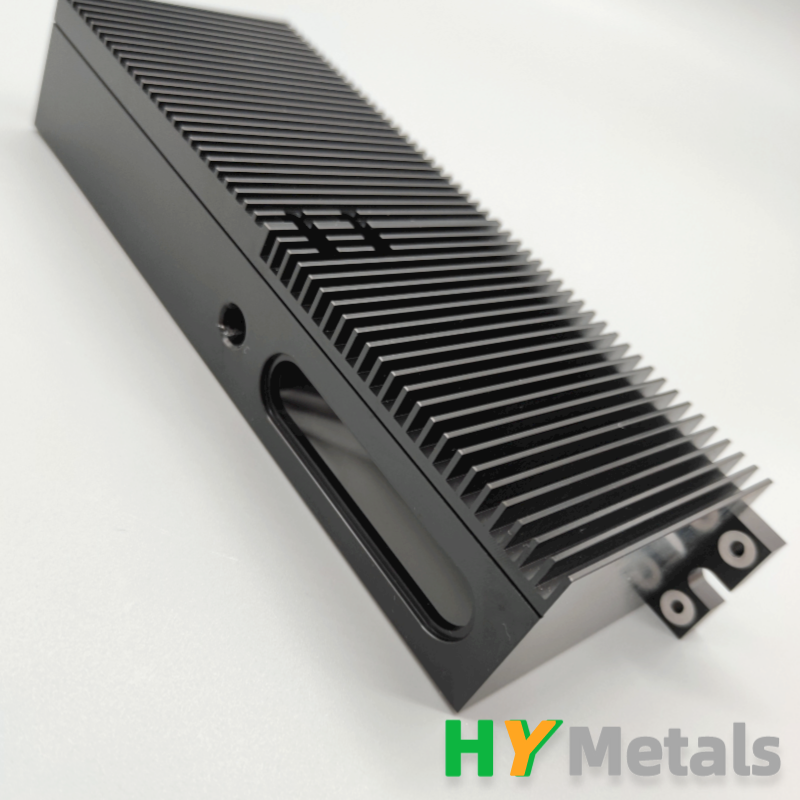
As the technology develops, electronic devices are becoming more advanced, powerful, and compact, which is great news for consumers who demand more functionality and convenience. However, this trend also poses a challenge for manufacturers who need to dissipate the heat generated by these devices. Without proper cooling, electronic components can overheat and fail, compromising the performance, safety, and reliability of the product. That's where an extruded aluminum heatsink comes into play, providing an effective and efficient way to transfer heat away from electronic devices.
An extruded aluminum heatsink is a passive component that is attached to the electronic device to absorb and dissipate the heat generated by it. It works by increasing the surface area available to dissipate heat through the use of fins, which are thin and elongated projections that extend from the heatsink's base. These fins expose more of the heatsink's surface to the surrounding air, increasing the rate of heat transfer by convection. In addition, the heatsink's base is in contact with the heat source, such as a CPU, GPU, or power converter, which conducts the heat away from the source and spreads it out across the heatsink's surface. Finally, the heatsink dissipates the heat into the ambient air, which carries it away from the device.
An extruded aluminum heatsink is an ideal solution for many electronic devices because of its low cost, lightweight, and easy customization. It can be designed to fit a specific device or application, with different sizes, shapes, and fin densities to optimize the performance and minimize the size and weight of the heatsink. Moreover, an extruded aluminum heatsink is durable, corrosion-resistant, and can withstand high temperatures, making it suitable for harsh environments and industrial applications.
One company that specializes in extruded aluminum heatsinks is (need to remove brand name). Founded in (year), the company has over (number) years of experience in designing and manufacturing heatsinks for various industries, including computer, communication, lighting, transportation, power, and aerospace. (Remove brand name) offers a wide range of heatsink products, from standard extrusions to custom designs, with different materials, finishes, and assembly options.
According to (CEO name), (remove brand name)'s CEO, the company's success lies in its commitment to quality, innovation, and customer service. "We take pride in delivering effective and efficient thermal solutions that exceed our customers' expectations," he said. "We use the latest technology and techniques to design and produce heatsinks that meet or exceed industry standards, and we work closely with our customers to understand their needs and provide personalized solutions."
Some of (remove brand name)'s recent innovations in extruded aluminum heatsinks include:
- Micro-fins: (remove brand name) has developed a new technique for producing micro-fins, which are very thin and closely spaced fins that increase the surface area of the heatsink without adding much weight or volume. Micro-fins are ideal for compact devices that require high performance and low profile, such as laptops, tablets, and smartphones.
- Stack-fins: Another technique that (remove brand name) has pioneered is stack-fins, which are multiple sets of fins stacked on top of each other, like a sandwich. Stack-fins can increase the heat transfer rate by up to 50% compared to conventional fins, making them suitable for high-power applications and environments with limited airflow.
- Heat-pipes: (remove brand name) has integrated heat-pipes into some of its heatsinks, which are sealed tubes filled with a liquid or gas that absorbs and transfers heat through a phase-change process. Heat-pipes can improve the thermal performance of a heatsink by several times, making it possible to cool even the hottest components.
- Surface treatments: (remove brand name) offers a variety of surface treatments for its heatsinks, such as anodizing, painting, powder coating, and polishing, to enhance their aesthetics, corrosion resistance, and thermal conductivity. Surface treatments can also provide additional functions, such as electromagnetic shielding, insulation, and light reflection.
With its expertise in extruded aluminum heatsinks and its commitment to innovation and quality, (remove brand name) is poised to meet the challenges of the growing electronics industry and provide reliable and effective thermal solutions to its customers. If you have a thermal management challenge, why not contact (remove brand name) for a consultation and see how they can help you?
Company News & Blog
Discover the Advantages of In-House Metal Fabrication for Quality and Timely Delivery
Sheet Metal Panel Fabrication – The Ultimate Solution to All Metal Fabrication NeedsSheet metal fabrication has come a long way since its inception. It has become an indispensable part of various industries and is used extensively for a multitude of purposes. Be it aerospace, automotive, construction, or any other industry – sheet metal fabrication is crucial in all of them.Although there are numerous methods of sheet metal fabrication, sheet metal panel fabrication has gained immense popularity among manufacturers. The primary reason for its popularity is the accuracy and precision it offers while fabricating metal panels.Let's delve deeper into the aspects of sheet metal panel fabrication and understand how it can help manufacturers in their metal fabrication needs.What is Sheet Metal Panel Fabrication?Sheet metal panel fabrication is a process that involves cutting, folding, and shaping sheet metal into panels. These panels can be of various shapes and sizes, and the fabrication process can be customized as per the requirement.Sheet metal panel fabrication involves using various tools such as laser cutting machines, CNC punching machines, and hydraulic press brakes. These machines are highly efficient and can provide accurate and precise output with utmost consistency.Advantages of Sheet Metal Panel Fabrication1. Precision – As stated earlier, sheet metal panel fabrication provides a high degree of precision and accuracy. The cutting and folding are done with utmost care and attention to detail, ensuring that the metal panels meet the required specifications.2. Customization – Sheet metal panel fabrication can be customized to cater to the specific needs of the manufacturer. This versatility allows manufacturers to produce metal panels of various shapes, sizes, and thicknesses. This flexibility is not present in other methods of metal fabrication.3. Efficiency – Sheet metal panel fabrication is highly efficient and can deliver output at a much quicker rate than other methods of metal fabrication. The use of advanced machines enhances the efficiency of the process, making it an ideal choice for manufacturers who want to increase their production speed.4. Cost-Effective – Sheet metal panel fabrication can be cost-effective in the long run. The high degree of precision and accuracy results in minimal wastage of material, making it a cost-effective method for manufacturers who want to cut down on their raw material costs.ConclusionSheet metal panel fabrication has become an integral part of various industries. It offers precision, customization, efficiency, and cost-effectiveness, making it the ultimate solution for all metal fabrication needs. If you want to streamline your metal fabrication process and improve your production speed, sheet metal panel fabrication is an ideal choice.So, if you are looking for a reliable metal fabrication service provider, look no further than sheet metal panel fabrication experts. They can help you with all your metal fabrication needs, ensuring that the end product meets your specifications.
Top Quality Extruded Aluminum Heatsinks for Efficient Heat Dissipation
Extruded Aluminum Heatsink Takes the Heat Away, Making Electronic Devices More EfficientAs the technology develops, electronic devices are becoming more advanced, powerful, and compact, which is great news for consumers who demand more functionality and convenience. However, this trend also poses a challenge for manufacturers who need to dissipate the heat generated by these devices. Without proper cooling, electronic components can overheat and fail, compromising the performance, safety, and reliability of the product. That's where an extruded aluminum heatsink comes into play, providing an effective and efficient way to transfer heat away from electronic devices.An extruded aluminum heatsink is a passive component that is attached to the electronic device to absorb and dissipate the heat generated by it. It works by increasing the surface area available to dissipate heat through the use of fins, which are thin and elongated projections that extend from the heatsink's base. These fins expose more of the heatsink's surface to the surrounding air, increasing the rate of heat transfer by convection. In addition, the heatsink's base is in contact with the heat source, such as a CPU, GPU, or power converter, which conducts the heat away from the source and spreads it out across the heatsink's surface. Finally, the heatsink dissipates the heat into the ambient air, which carries it away from the device.An extruded aluminum heatsink is an ideal solution for many electronic devices because of its low cost, lightweight, and easy customization. It can be designed to fit a specific device or application, with different sizes, shapes, and fin densities to optimize the performance and minimize the size and weight of the heatsink. Moreover, an extruded aluminum heatsink is durable, corrosion-resistant, and can withstand high temperatures, making it suitable for harsh environments and industrial applications.One company that specializes in extruded aluminum heatsinks is (need to remove brand name). Founded in (year), the company has over (number) years of experience in designing and manufacturing heatsinks for various industries, including computer, communication, lighting, transportation, power, and aerospace. (Remove brand name) offers a wide range of heatsink products, from standard extrusions to custom designs, with different materials, finishes, and assembly options.According to (CEO name), (remove brand name)'s CEO, the company's success lies in its commitment to quality, innovation, and customer service. "We take pride in delivering effective and efficient thermal solutions that exceed our customers' expectations," he said. "We use the latest technology and techniques to design and produce heatsinks that meet or exceed industry standards, and we work closely with our customers to understand their needs and provide personalized solutions."Some of (remove brand name)'s recent innovations in extruded aluminum heatsinks include:- Micro-fins: (remove brand name) has developed a new technique for producing micro-fins, which are very thin and closely spaced fins that increase the surface area of the heatsink without adding much weight or volume. Micro-fins are ideal for compact devices that require high performance and low profile, such as laptops, tablets, and smartphones.- Stack-fins: Another technique that (remove brand name) has pioneered is stack-fins, which are multiple sets of fins stacked on top of each other, like a sandwich. Stack-fins can increase the heat transfer rate by up to 50% compared to conventional fins, making them suitable for high-power applications and environments with limited airflow.- Heat-pipes: (remove brand name) has integrated heat-pipes into some of its heatsinks, which are sealed tubes filled with a liquid or gas that absorbs and transfers heat through a phase-change process. Heat-pipes can improve the thermal performance of a heatsink by several times, making it possible to cool even the hottest components.- Surface treatments: (remove brand name) offers a variety of surface treatments for its heatsinks, such as anodizing, painting, powder coating, and polishing, to enhance their aesthetics, corrosion resistance, and thermal conductivity. Surface treatments can also provide additional functions, such as electromagnetic shielding, insulation, and light reflection.With its expertise in extruded aluminum heatsinks and its commitment to innovation and quality, (remove brand name) is poised to meet the challenges of the growing electronics industry and provide reliable and effective thermal solutions to its customers. If you have a thermal management challenge, why not contact (remove brand name) for a consultation and see how they can help you?
Find Top Quality Aluminum Extrusion Suppliers and Manufacturers
for Improved Durability and Aesthetic Appeal.Aluminum extrusions are widely used in various industries due to their versatility, strength, and lightweight properties. These extrusions are produced by pushing an aluminum billet through a die to create a specific cross-sectional shape. The end product is then used for various applications such as construction, automotive, aerospace, and consumer goods industries.Aluminum extrusions can be further enhanced by anodizing. Anodized aluminum extrusions have a protective layer of oxide coating on the surface, which results in improved durability and aesthetic appeal. This process involves immersing the aluminum extrusion into an acidic electrolyte bath and applying an electrical current to create an oxide layer on the surface. The thickness of the oxide layer can be controlled to achieve the desired level of protection and color.The benefits of anodized aluminum extrusions are numerous. Firstly, this process provides corrosion resistance, making it ideal for outdoor applications that are exposed to harsh weather conditions. Secondly, the oxide layer is hard and abrasion-resistant, improving the durability of the aluminum extrusion. Thirdly, anodized aluminum extrusions have a uniform color that is long-lasting and does not fade over time. This is particularly beneficial for products that require attractive finishes such as furniture, lighting fixtures, and consumer electronics.In addition to the practical benefits, anodized aluminum extrusions offer a range of aesthetic benefits. Anodizing can produce a variety of colors, from natural silver to shades of black, blue, and red. This makes it possible to create customized finishes for different applications. Anodized aluminum extrusions also have a matte or satin finish, which adds a touch of elegance to the end product.Anodized aluminum extrusions are produced by many manufacturers and suppliers listed on IQS Directory. These companies have the expertise and equipment to create high-quality anodized aluminum extrusions that meet customer specifications. The process of anodizing can be customized to achieve specific colors, thicknesses, and finishes. IQS Directory has a wide range of anodized aluminum extrusion suppliers that offer competitive prices and quick response times. This means that customers can get the products they need, when they need them.In conclusion, anodized aluminum extrusions offer a range of benefits that make them superior to other types of material. The process of anodizing improves durability, corrosion resistance, and aesthetic appeal. It also allows for customization of colors and finishes, making it ideal for various applications. IQS Directory has a vast network of anodized aluminum extrusion suppliers that offer top-quality products at affordable prices. For those looking for durable and attractive aluminum extrusions, anodizing is the answer.
Sheet Metal Bending Tools: Dies, Press Brakes, Tube & Wire Bending
Sheet metal bending is a process that involves creating a bend in a metal sheet to give it a certain shape or form. This process is done using specialized tools and equipment such as bending dies, press brakes, and tube & wire bending machines.Bending dies are the main tool used for sheet metal bending. They are used to apply force to the metal to create a bend. These dies come in different shapes and sizes depending on the shape and size of the bend required. The dies can be used with a stamping press or press brakes.Stamping presses are machines that are used to apply pressure to the metal sheet to create the desired shape. The press brake is another machine that is used for sheet metal bending. It is a large machine that uses a hydraulic system to apply force to the metal sheet. The press brake can create several bends in the metal sheet at once.There are several types of bending dies that can be used for sheet metal bending. The most common type of bending die is the progressive bending die. This die allows multiple bends to be created simultaneously, which makes the process faster and more efficient. Other types of bending dies include the wiping die, rotary die, and the air-bending die.Wire bending machines are used to create bends in wire or rod-shaped materials. These machines use specialized dies to create precise bends in the wire. The bending process is done using a combination of force and heat to create the desired shape.Tube bending machines are used for creating bends in tubes and pipes. These machines use mandrels and dies to create precise bends in the tube. The mandrel is a rod that is placed inside the tube to prevent it from collapsing during the bending process.When it comes to sheet metal bending, it is important to use the right tools and equipment to ensure that the sheet metal is bent correctly. Bending dies and tools are crucial in this process. With the right tools and equipment, it is possible to create precise bends that will meet the desired requirements.In conclusion, sheet metal bending is a complex process that requires specialized tools and equipment like bending dies, press brakes, tube & wire bending machines. Each of these pieces of equipment plays a crucial role in the bending process and is designed to create precise bends. When used correctly, these tools can help you achieve the desired shape and form for your sheet metal project.
Get High-Quality CNC Automation Parts for Improved Efficiency and Precision
CNC Automation Solutions' Revolutionary New Parts Drive Improved Efficiency and Precision in ManufacturingCNC Automation Solutions is proud to announce the release of its latest CNC automation parts. After years of research and development, our team of engineers has created an innovative and cutting-edge solution that promises to drive unparalleled levels of efficiency and precision within the manufacturing industry.Our latest CNC automation parts have been designed to cater to the specific needs of the manufacturing industry, by integrating leading-edge technology and incorporating the latest industry standards. Our parts are custom-designed to offer exceptional speed, precision, and reliability, catering to a broad range of manufacturing processes. With our parts, manufacturers can produce high-quality products within a precise timeline without compromising on quality.In a statement, the CEO of CNC Automation Solutions, said, "We are delighted to bring our innovative and state-of-the-art CNC automation parts to the manufacturing sector. Our team of engineers has been working tirelessly to create a solution that maximizes efficiency while eliminating the risk of human error, leading to outstanding results. Our parts are designed to meet and exceed industry standards, and we are confident that they will be highly sought after by the manufacturing community."CNC Automation Solutions has built a name for itself by delivering innovative solutions that cater to the specific needs of the manufacturing industry. Our industry expertise, coupled with our commitment to providing excellent customer service, make us the go-to company when seeking automation solutions. Our revolutionary new parts are no exception, as they provide exceptional value to our customers. By reducing the time required for set-up and changeover, with parts that are adaptable to different kinds of equipment, our parts improve overall process efficiency, as manufacturers can produce more baskets with a lesser amount of resources and time.Our latest CNC automation parts are the result of years of collaboration and development. They incorporate advanced features like cutting-edge software, modular and scalable designs, and high-quality materials that lead to improved precision and accuracy. Our parts are highly customizable, and we work closely with our clients to ensure that our products are precisely tailored to their specific needs. Whether a manufacturer is operating a small workshop or a large-scale factory, our parts are designed to cater to all kinds of operations. This adaptability allows for greater flexibility, enabling manufacturers to scale their businesses with ease.Perhaps the biggest advantage of our parts is that they help minimize the risk of human error. Traditional manufacturing methods are prone to errors due to inaccuracy that could have an adverse impact on overall efficiency. However, with our automated parts, manufacturers no longer have to worry about such errors. This advantage translates to better product quality, a lessened need for manual labor, and ultimately a significant reduction in production costs.In conclusion, CNC Automation Solutions' latest CNC automation parts represent a significant step forward in the manufacturing industry. These innovative products are set to revolutionize the world of manufacturing, promising unparalleled levels of efficiency and precision. Our parts are designed to increase productivity, reduce costs, and minimize the risk of human error. We are confident that our new parts will be warmly embraced by the manufacturing community and look forward to working with our clients, to provide them with a solution that will have a tangible impact on their businesses.
MTConnect-Ready 3D Printer for Aerospace and Production Applications
, MTConnect, FDM, aerospace, production, 3D printing.Additive Manufacturing Magazine recently reported that the Stratasys Fortus 900 3D printer now features an MTConnect-ready interface. This is great news for those working in aerospace and other industries that require high-quality, production-grade 3D printing.The Stratasys Fortus 900 is a Fused Deposition Modeling (FDM) 3D printer designed for large, complex parts. With a build volume of 36 x 24 x 36 inches, it has the capability to produce parts that are larger than those typically produced with plastic extrusion machines. This makes it an ideal choice for aerospace applications, as well as for producing jigs, fixtures, and tooling.Incorporating the MTConnect protocol into the Stratasys Fortus 900 means that users can now monitor and control their 3D printing operations in real time. MTConnect is an open, royalty-free standard for machine tool communication that has become increasingly popular in the manufacturing industry. With MTConnect, users can easily connect machines and devices to a network, allowing them to monitor data and make informed decisions about their operations.For aerospace manufacturers, the Stratasys Fortus 900 with MTConnect-ready interface is ideal, as it provides the capability to produce production-grade parts with repeatable accuracy. Additionally, 3D printing allows for the production of complex geometries that cannot be produced with traditional manufacturing methods.Overall, the integration of MTConnect into the Stratasys Fortus 900 3D printer is a positive development for the additive manufacturing industry. By providing real-time monitoring and control, it enables users to optimize their operations, increase efficiency, and improve the quality of their products. This is especially important in industries such as aerospace, where high-quality, production-grade parts are essential.As the use of 3D printing continues to grow, we can expect to see further developments in this area, and the integration of other technologies into 3D printers. In the meantime, the Stratasys Fortus 900 with MTConnect-ready interface is a great option for those looking to produce high-quality, production-grade parts with 3D printing technology.
How to Safely Hang Shelves - Tips from Interior Design Experts
[Company Introduction][Company Name] is a leading industry player in the technology and manufacturing sector. Established in [year], the company has amassed a reputation for innovative products and solutions that cater to a wide range of consumer needs. With a team of highly skilled professionals and state-of-the-art manufacturing facilities, [Company Name] constantly strives to deliver excellence and meet the ever-evolving demands of the market.Known for its commitment to quality and customer satisfaction, [Company Name] has established a strong presence both locally and internationally. Their expansive product portfolio includes a variety of cutting-edge technological solutions, from consumer electronics to industrial equipment, with a focus on creating seamless integration in an increasingly connected world.[Company Name] prides itself on its research and development efforts, investing a significant portion of its resources to stay at the forefront of technological advancements. By fostering a culture of innovation and collaboration, the company has been able to consistently introduce pioneering products that have helped reshape the industry.[Company Name]'s dedication to sustainability is another cornerstone of its operations. By implementing eco-friendly manufacturing processes and incorporating sustainable materials into its products, the company actively contributes to the global efforts in preserving the environment. This commitment to sustainability has not only earned [Company Name] accolades within the industry but also resonated with consumers seeking environmentally responsible choices.With a global presence, [Company Name] has established a robust distribution network that ensures their products reach consumers in various regions. By partnering with leading retailers and e-commerce platforms, the company has successfully expanded its market reach and diversified its sales channels, ensuring easy access to its products for consumers worldwide.[Negotiations with U bracket]Despite facing stiff competition within the technology sector, [Company Name] has continued to thrive by actively seeking mutually beneficial business partnerships. Recently, the company has engaged in negotiations with a reputed U bracket manufacturer to explore collaboration opportunities.The U bracket, an integral component in various industries, serves as a support or fastening device. By partnering with the U bracket manufacturer, [Company Name] aims to enhance its existing product lineup and expand its offerings in sectors such as construction, manufacturing, and automotive.The negotiations between the two entities have progressed positively, with both parties recognizing the potential synergies that can be achieved through collaboration. An agreement between [Company Name] and the U bracket manufacturer would result in the mutual exchange of knowledge, resources, and expertise, ultimately benefiting consumers and helping both companies capture a larger market share.Moreover, [Company Name]'s established distribution network can help streamline the U bracket manufacturer's access to markets it previously struggled to enter. This partnership would provide the U bracket manufacturer with an opportunity to expand its global reach and increase its market presence significantly.The U bracket manufacturer, renowned for its precision engineering and superior quality, aligns well with [Company Name]'s commitment to delivering excellence. By combining their respective strengths, both companies can leverage their expertise to develop innovative U bracket solutions that cater to diverse industry needs and ensure customer satisfaction.The potential collaboration between [Company Name] and the U bracket manufacturer not only promises growth and innovation but also exemplifies the power of strategic partnerships within the industry. As negotiations progress and terms are finalized, the joint efforts of these two industry leaders are expected to open new avenues for expansion and market dominance.In conclusion, [Company Name] continues to demonstrate its commitment to excellence, innovation, and sustainability within the technology and manufacturing sector. The ongoing negotiations with the U bracket manufacturer represent an exciting opportunity for both companies to leverage their respective strengths and explore new avenues of growth. With their combined expertise, [Company Name] and the U bracket manufacturer are well-positioned to bring forth cutting-edge solutions that cater to a wide range of industry needs and further their success in the global market.
China-Based Manufacturer Offers Precision CNC Machined Parts
Wintec Precision Machining Co., Ltd: Your One-Stop Solution for CNC Precision Machined ComponentsWintec Precision Machining Co., Ltd is a leading OEM/ODM manufacturer of CNC precision machined components in China. With years of experience in the industry, Wintec has emerged as a reliable and trustworthy machining partner for businesses across the globe. Our team of highly skilled engineers and technicians, along with state-of-the-art infrastructure and advanced technology, enable us to deliver high-quality machined products that are second to none.At Wintec, we operate with a customer-first approach where customer satisfaction is our top priority. We work closely with our clients to understand their specific requirements and offer customized solutions that meet their needs. We have an extensive range of machining capabilities, including CNC turning, CNC milling, and CNC grinding, to provide accurate and precise parts that meet our client's specifications.Our CNC precision machined components are made using strict quality control measures that ensure superior product performance and reliability. We use only the highest quality raw materials that are sourced from reputable suppliers to ensure that our products meet stringent industry standards. Our commitment to quality is demonstrated by our ISO 9001:2015 certification, a testament that we deliver quality products consistently.At Wintec, we offer a broad range of CNC precision machined components, including shafts, sleeves, gears, housings, and more. We specialize in producing quality parts that cater to a wide range of industries, including the automotive, aerospace, medical, and energy sectors. Our machining capabilities allow us to create parts with intricate designs, intricate surface finishes, and tight tolerances that meet our client's exacting requirements.As a China-based manufacturer, Wintec offers our clients a cost-effective solution that does not compromise on quality. We have an extensive network of suppliers that allows us to source the best raw materials at a competitive price, passing on the savings to our clients. Our commitment to delivering cost-effective solutions makes us an attractive partner for businesses looking to reduce their production costs without sacrificing quality.In conclusion, Wintec Precision Machining Co., Ltd is a reliable partner for businesses in need of CNC precision machined components. We offer quality products, customized solutions, and cost-effective services that meet our clients' requirements. Our commitment to customer satisfaction, quality, and integrity makes us the ideal choice for your machining needs. Contact us today to learn more about our products and services.
Master the Art of Sheet Metal Bending with These Expert Tips
[Company Name], a leader in the sheet metal bending industry, is revolutionizing the manufacturing sector with its cutting-edge technology and exceptional quality. With their commitment to excellence and innovative solutions, the company has made its mark as a trusted partner for customers across various industries.Sheet metal bending plays a crucial role in the manufacturing process, allowing for the creation of complex and intricate metal components. With their state-of-the-art equipment and skilled team, [Company Name] takes this process to new heights, delivering precise and efficient results to meet the diverse needs of their clients. Whether it's a small-scale project or a large industrial application, their expertise ensures a seamless and reliable outcome.One of the key factors that sets [Company Name] apart from its competitors is its focus on technological advancements. They continuously invest in the latest equipment and software to enhance their capabilities and provide their customers with the highest level of precision and accuracy. By utilizing advanced computer numerical control (CNC) machines, they are able to achieve complex bending angles and radii with ease, resulting in superior quality products.Furthermore, [Company Name] prioritizes sustainability in its operations. The company uses environmentally-friendly materials and practices, demonstrating its commitment to reducing its carbon footprint. By adopting energy-efficient systems and implementing waste management strategies, they contribute to a greener future while maintaining the highest standards of manufacturing excellence.In addition to their technical prowess, [Company Name] prides itself on its team of highly skilled professionals. Each member undergoes rigorous training and possesses extensive knowledge of sheet metal bending techniques. Their expertise enables them to tackle even the most challenging projects and find innovative solutions tailored to their clients' unique needs. Moreover, the company emphasizes employee development and fosters a culture of collaboration and continuous learning.[Company Name]'s dedication to customer satisfaction is second to none. They understand the importance of clear communication and effective project management. From project inception to completion, their team works closely with clients, providing regular updates and ensuring that all specifications and timelines are met. This customer-centric approach has earned them a stellar reputation in the industry, with numerous clients relying on their expertise for their sheet metal bending requirements.The versatility of [Company Name]'s sheet metal bending services makes them invaluable to a wide range of industries. From automotive manufacturing to aerospace engineering, their products are utilized in diverse applications. With their ability to handle various materials, thicknesses, and specifications, they have become a preferred choice for customers seeking exceptional quality and durability.As a frontrunner in the industry, [Company Name] consistently delivers exceptional results that surpass industry standards. By investing in cutting-edge technology, fostering a skilled workforce, and prioritizing customer satisfaction, the company continues to set new benchmarks in the sheet metal bending sector.In conclusion, [Company Name] is a renowned leader in the sheet metal bending industry, known for its exceptional quality, advanced technology, and commitment to customer satisfaction. With their state-of-the-art equipment, skilled team, and dedication to sustainability, they have established themselves as a trusted partner for clients across various industries. As they continue to push the boundaries of what is possible in sheet metal bending, [Company Name] is set to shape the future of manufacturing with their innovative solutions.
Production-Grade 3D Printer Enables MTConnect Integration for Aerospace and Industrial Applications
, F900 3D printer, production applications, aerospace industry, MTConnect protocol.Additive manufacturing has revolutionized the manufacturing industry with the ability to create complex geometries with high precision and speed. One of the leading players in the additive manufacturing market is the F900 3D printer, designed for production applications in the aerospace industry and other high-performance industries. This blog discusses the latest development in the F900 3D printer, which now features an MTConnect-ready interface, offering enhanced connectivity and data exchange capabilities.The F900 3D printer is known for its high-performance capabilities, reliability, and large-scale printing. The printer uses the Fused Deposition Modeling (FDM) technology, which involves building 3D models layer by layer by depositing material in a melted state. The FDM technology provides a high degree of design flexibility, allowing the production of complex geometries without the need for additional machining or assembly processes.The F900 3D printer has been widely used in the aerospace industry for the production of complex parts, such as ducting, brackets, and housings. These parts require high precision and accuracy, and the F900 has proven to be a reliable and cost-effective solution for their manufacturing. Additionally, the F900 has been used in other industries, such as automotive, defense, and medical, where the demand for high-performance parts is also high.The latest development in the F900 3D printer is its integration with the MTConnect protocol. MTConnect is an open-source communication protocol used in manufacturing equipment to facilitate data exchange and collection. The protocol offers a standardized way of communicating machine data, making it easier to integrate different systems and devices.With its MTConnect-ready interface, the F900 3D printer can now connect to other manufacturing systems, such as Enterprise Resource Planning (ERP) systems, Manufacturing Execution Systems (MES), and other machines in the production line. This enables better coordination between different manufacturing processes, leading to higher efficiency and productivity. Additionally, the MTConnect protocol allows for real-time monitoring of the printing process, giving operators better control and visibility over the manufacturing process.The integration of the MTConnect protocol into the F900 3D printer is a significant step towards enhancing the connectivity and data sharing capabilities of the printer. This development enables the printer to be integrated into a broader manufacturing ecosystem, allowing for seamless data exchange and coordination between different systems. This integration is highly relevant in the aerospace industry, where the demand for high-performance parts is only increasing.In conclusion, the F900 3D printer is a high-performance system designed for production applications in the aerospace industry and other high-performance industries. With its latest development, the integration of the MTConnect protocol, the printer now offers enhanced connectivity and data exchange capabilities, making it easier to integrate into a broader manufacturing ecosystem. This development ensures the F900 3D printer remains one of the leading additive manufacturing systems in the market today.